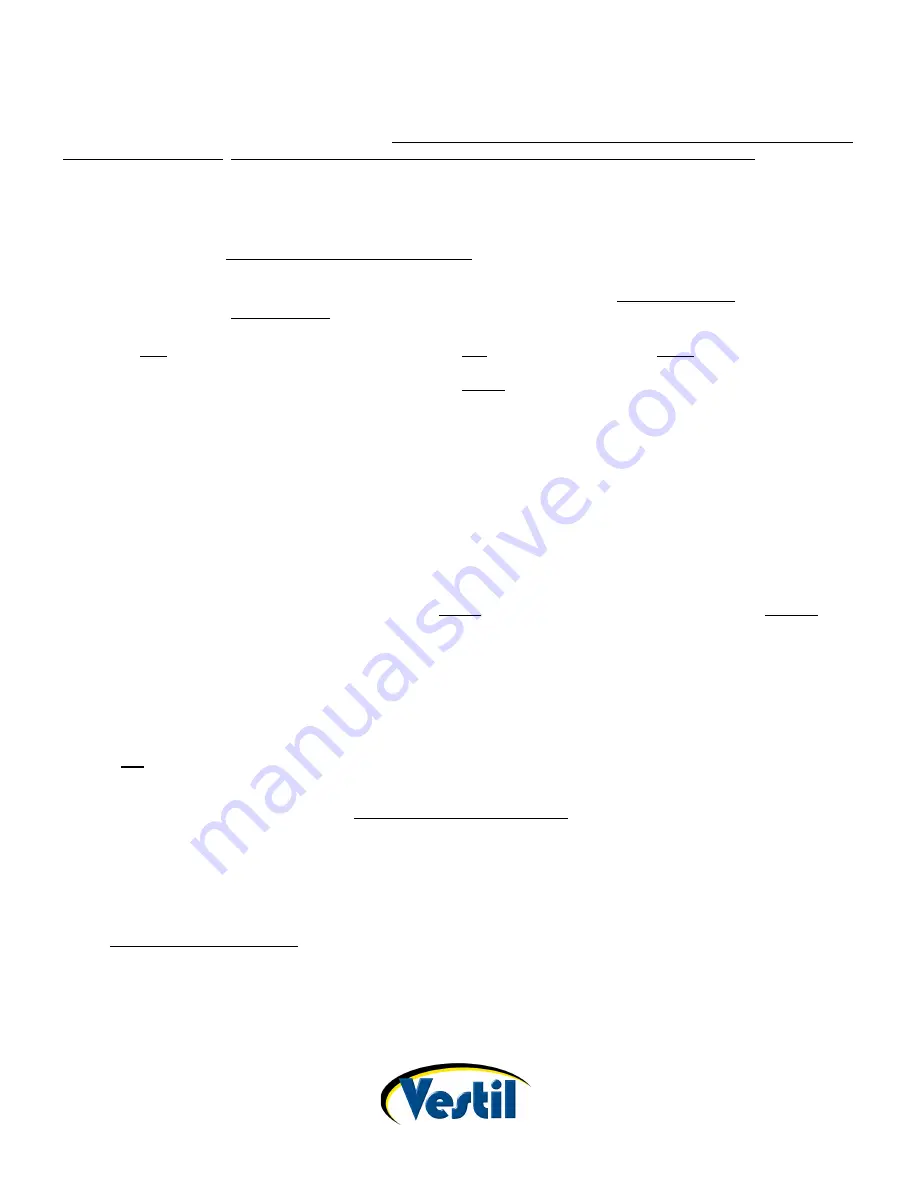
Rev. 2/21/2017
HDC-905, MANUAL
Copyright 2017 Vestil Manufacturing Corp.
Page 18 of 19
LIMITED WARRANTY
Vestil Manufacturing Corporation (“Vestil”) warrants HDC-905 series hydraulic drum crushers, excluding “Wash-down”
model HDC-905-WD (see limited warranty on following page), to be free of defects in material and workmanship during
the warranty period.
Our warranty obligation is to provide
a replacement for a defective original part
if
the part is
covered by the warranty
,
after we receive a proper request from the warrantee (you) for warranty service
.
Who may request service?
Only a warrantee may request service.
You are a warrantee
if
you purchased the product from Vestil or from an
authorized distributor AND Vestil has been fully paid.
What is an “original part”?
An original part is a part
used to make the product as shipped
to the warrantee.
What is a “proper request”?
A request for warranty service is proper if Vestil receives: 1) a photocopy of the Customer Invoice that displays the
shipping date; AND 2) a written request for warranty service including your name and phone number. Send requests
by any of the following methods:
Fax
Vestil Manufacturing Corporation
(260) 665-1339
2999 North Wayne Street, PO Box 507
Phone
Angola, IN 46703
(260) 665-7586
In the written request, list the parts believed to be defective and include the address where replacements should be
delivered.
What is covered under the warranty?
After Vestil receives your request for warranty service, an authorized representative will contact you to determine
whether your claim is covered by the warranty. Before providing warranty service, Vestil may require you to send the
entire product, or just the defective part or parts, to its facility in Angola, IN. The warranty covers defects in the
following
original
dynamic components: motors, hydraulic pumps, electronic controllers, switches and cylinders. It also
covers defects in
original
parts that wear under normal usage conditions (“wearing parts”): bearings, hoses, wheels,
seals, brushes, batteries, and the battery charger.
How long is the warranty period?
The warranty period for original dynamic components is 1 year. For wearing parts, the warranty period is 90 days. The
warranty periods begin on the date when Vestil ships the product to the warrantee. If the product was purchased from
an authorized distributor, the periods begin when the distributor ships the product. Vestil may, at its sole discretion,
extend the warranty periods for products shipped from authorized distributors by
up to
30 days to account for shipping
time.
If a defective part is covered by the warranty, what will Vestil do to correct the problem?
Vestil will provide an appropriate replacement for any
covered
part. An authorized representative of Vestil will contact
you to discuss your claim.
What is not covered by the warranty?
1. Labor;
2. Freight;
3. Occurrence of any of the following, which automatically voids the warranty:
Product misuse;
Negligent operation or repair;
Corrosion or use in corrosive environments;
Inadequate or improper maintenance;
Damage sustained during shipping;
Collisions or other incidental contacts causing damage to the product;
Unauthorized modifications: DO NOT modify the product IN ANY WAY without first receiving written
authorization from Vestil. Modification(s) might make the product unsafe to use or might cause excessive
and/or abnormal wear.
Do any other warranties apply to the product?
Vestil Manufacturing Corp.
makes no other express warranties. All implied warranties are disclaimed to the extent
allowed by law. Any implied warranty not disclaimed is limited in scope to the terms of this Limited Warranty.