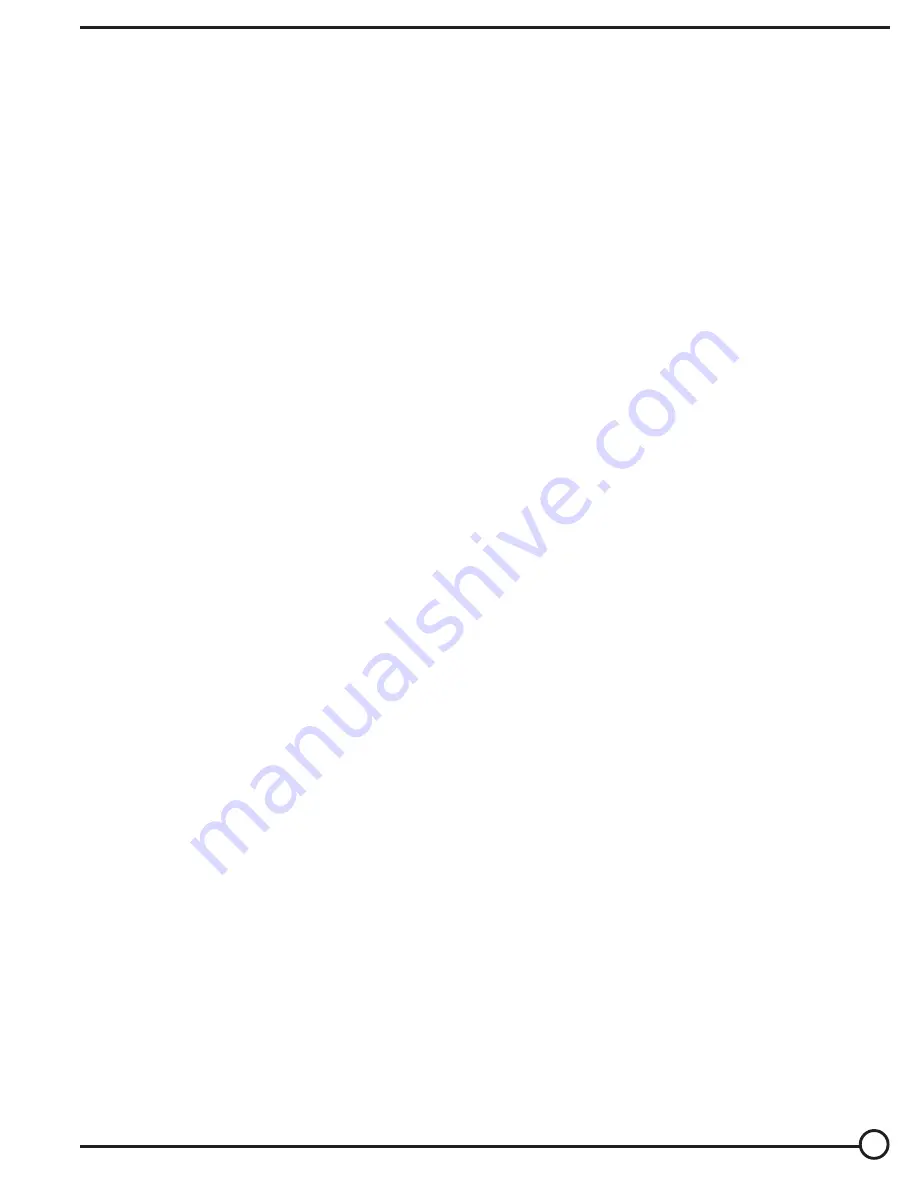
THE POWER UNIT’S OPERATION - EHLTG
The electric/hydraulic zero-clearance scissor lift table utilizes an electric motor directly coupled to a gear-type hydraulic pump
to produce the needed fluid pressure and flow to allow the cylinders to perform the work of raising a load.
A hydraulic manifold houses the hydraulic control components, and is bolted directly onto the gear pump.
The power unit’s hydraulic components are all rated for 3,000 psi working pressure.
• Important parts of the power unit include:
- The electric motor. Motors are available for operation on single- or three-phase AC supplies (all are dual-voltage capable).
- The gear pump. Its shaft is coupled directly to the shaft of the electric motor. Several displacements are available, depend-
ing on the motor horsepower used.
- The check valve. Its purpose is to prevent the backflow of fluid through the pump. In this way it allows the platform to be
held at a given elevation indefinitely.
- The pressure relief valve. Its job is to open a path for fluid to flow back to the reservoir in the event that the fluid pressure
built up by the pump exceeds 3,000 psi. Thus the system cannot see more than 3,000 psi.
- The lowering solenoid valve. This is an electrically-operated cartridge valve. It contains a screen to keep contaminants from
entering the valve.
- The pressure-compensated flow control spool. This regulates the fluid flow back to the reservoir when the valve opens. It
allows the platform to always lower at the same rate regardless of whether there is a load in the platform or not. Several
sizes are available.
- The hydraulic lifting cylinders. These are displacement-style cylinders. They have a bleeder valve located at their top end to
allow air to be bled from the hydraulic system.
- The safety velocity fuse. This is a device that is installed in the cylinder’s hose port. It closes quickly in the event of a
catastrophic hose failure to prevent the platform from collapsing down. The platform remains stationary until pressure
is reapplied to the system.
- The hydraulic fluid. The system uses HO150 hydraulic fluid. Any anti-wear hydraulic fluid with a viscosity grade of 150 SUS
at 100°F (ISO 32 @ 40°C), such as AW-32 hydraulic fluid or Dexron transmission fluid, is acceptable.
• When the platform is to be lifted, press the “RAISE” switch. The motor turns, and in turning it spins the hydraulic gear
pump. Oil is drawn from the reservoir through the suction filter and into the pump.
- The pump pushes the pressurized oil through the check valve and out to the lift cylinders. Releasing
the “RAISE” switch at any point will stop the lift, and the platform will hold at that height.
An upper travel limit switch turns off the motor when the platform is at its full lift height.
• When the platform is to be lowered, press the “LOWER” switch.
- The lowering valve opens, bypassing the check valve and allowing the oil in the cylinders to return back to the reservoir
through the return hose. The rate at which the platform lowers is regulated by the internal pressure-compensated flow
spool. Releasing the push-button at any point will stop the rotation, and the platform will hold at that height.
•
In the event that the platform creeps down slowly after releasing a “LOWER” control, it will be necessary to remove
the lowering cartridge valve (whichever is applicable) for inspection and cleaning, as follows:
- Lower the platform until it is fully lowered.
- Remove any load from the platform.
- Remove the nut holding the solenoid coil onto the valve stem, then remove the coil, and then unscrew the valve from the
manifold.
- Inspect the valve for contaminants, and the valve’s o-rings and backup washers for cuts, tears, or other damage.
- With the valve immersed in mineral spirits or kerosene, use a thin tool such as a small screwdriver or a small hex wrench to
push the poppet in and out several times from the bottom end of the valve. The valve should move freely, about 1/16” from
closed to open position. If it sticks in, the valve stem could be bent and will need to be replaced if it doesn’t free up after
cleaning. Blow the valve off with a compressed-air gun while again pushing the poppet in and out. - Inspect the bottom of the
manifold’s valve cavity for contaminants.
- Again with the thin tool, press on the middle of the flow control spool located in the bottom of the cavity. It should move down
and back up freely.
- Reinstall the valve into the manifold, tightening the valve with approximately 20 lb-ft of torque.
• If the platform lowers extremely slowly, or not at all, a cylinder’s velocity fuse could be closing. This can be caused by air
in the hydraulic cylinder. To bleed the air from the system: - Remove any load from the platform.
- Raise the platform and install the maintenance props.
- Lower the platform until the legset is supported on the props.
- Hold a rag over each cylinder’s bleeder valve (it looks like a grease zirk) and open the valve about ½ turn with a 1/4” or 5/16”
wrench. Oil and air will sputter from the valve – once no air is observed, close the valve.
9