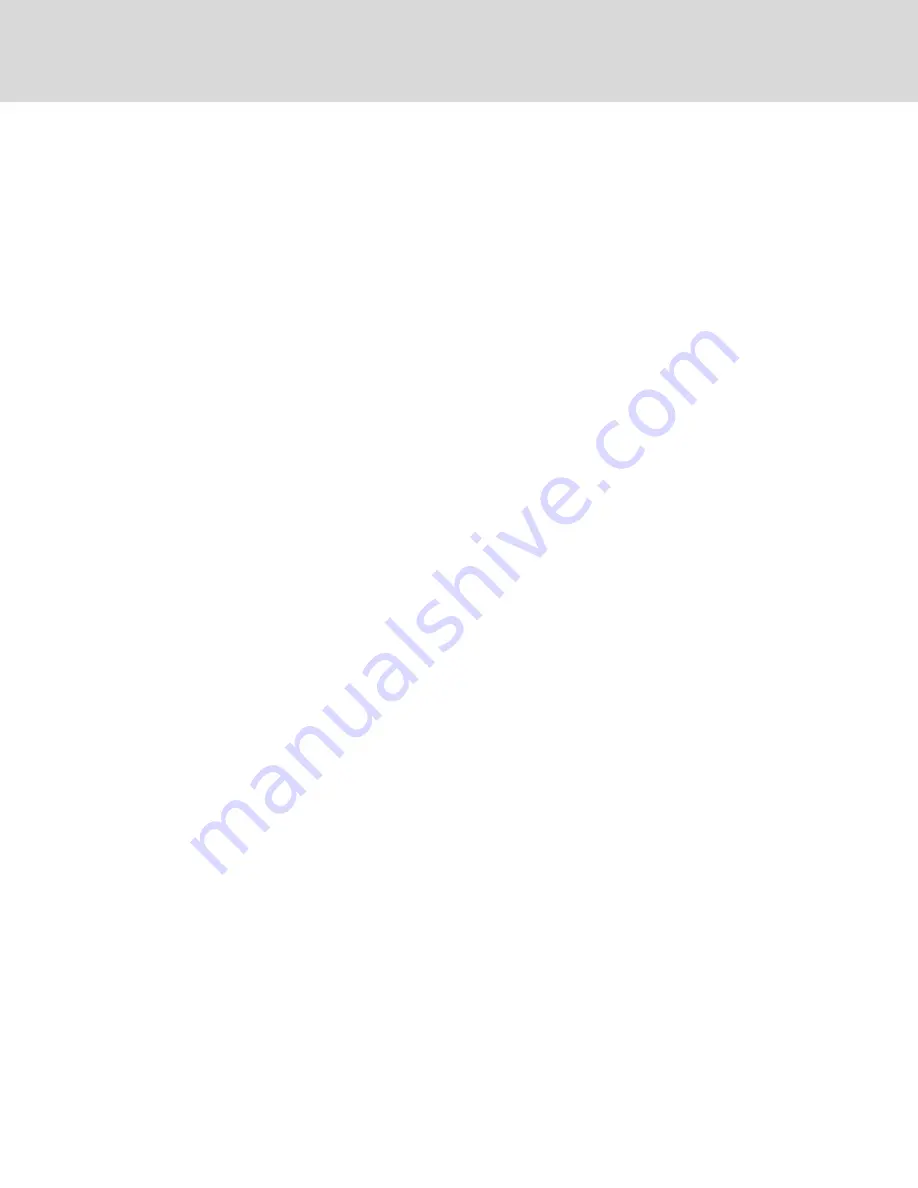
8.5.12 Evacuation, Leak Testing, and Charging
Evacuation and Leak Testing Air Cooled Systems
For proper leak check and evacuation, you must open all system valves and account for all check valves.
NOTE: The system includes a factory installed check valve and an additional downstream Schrader valve with core in
the compressor discharge line. Proper evacuation of the condenser side of the compressor can be accomplished only
using the downstream Schrader valve. See the appropriate piping schematic for your system in
1.
Starting with Circuit #1, open the services valves and place 150 PSIG (1034kPa) of dry nitrogen with a tracer of
refrigerant. Check system for leaks with a suitable leak detector.
2.
With pressure still in Circuit #1, open the compressor service valves in Circuit #2.
•
If pressure increases in Circuit #2, the system is cross-circuited and must be re-checked for proper
piping.
•
If there is no pressure increase, repeat Step 1 on Circuit #2.
3.
After completion of leak testing, release the test pressure, (observe local code) and pull an initial deep vacuum
of 500 microns on the system with a suitable pump.
4. After 4 hours, check the pressure readings and, if they have not changed, break vacuum with dry nitrogen. Pull
a second and third vacuum to 500 microns or less. Re-check the pressure after 2 hours.
When the three checks are complete, remove the jumper hose from the service valve fitting and the condenser, and proceed
to
Charging Air Cooled Systems
NOTICE
Risk of improper refrigerant charging. Can cause equipment damage.
R-410A is a blended refrigerant and must be introduced and charged from the cylinder only as a liquid.
When adding liquid refrigerant to an operating system, it may be necessary to add the refrigerant through the
compressor suction service valve. Care must be exercised to avoid damage to the compressor. We recommend
connecting a sight glass between the charging hose and the compressor suction service valve. This will permit
adjustment of the cylinder hand valve so that liquid can leave the cylinder while allowing vapor to enter the
compressor.
NOTICE
Risk of improper operation. Can cause compressor failure.
Operating the unit with the EEV closed can cause compressor failure. The reheat and humidifier are disabled. A
minimum of 20 psig (138 kPa) must be established and maintained for the compressor to operate. The
charging function can be reset as many times as required to complete.
To charge the system:
1.
Check the nameplate on the unit for refrigerant type to be used.
2.
The unit must be operating during charging. Refer to
Checklist for Completed Installation
3.
Calculate the amount of charge for the system. See
Refrigerant Piping and Charging
Vertiv | DSE Packaged Solution Installer/User Guide
44
Summary of Contents for Liebert DSE Packaged 400
Page 1: ...Liebert DSE Packaged Solution Installer User Guide 400 kW to 500 kW...
Page 24: ...Vertiv DSE Packaged Solution Installer User Guide 20 This page intentionally left blank...
Page 32: ...Vertiv DSE Packaged Solution Installer User Guide 28 This page intentionally left blank...
Page 34: ...Vertiv DSE Packaged Solution Installer User Guide 30 This page intentionally left blank...
Page 36: ...Vertiv DSE Packaged Solution Installer User Guide 32 This page intentionally left blank...
Page 68: ...Vertiv DSE Packaged Solution Installer User Guide 64 This page intentionally left blank...
Page 103: ...Vertiv DSE Packaged Solution Installer User Guide 66 This page intentionally left blank...
Page 104: ...Vertiv DSE Packaged Solution Installer User Guide...