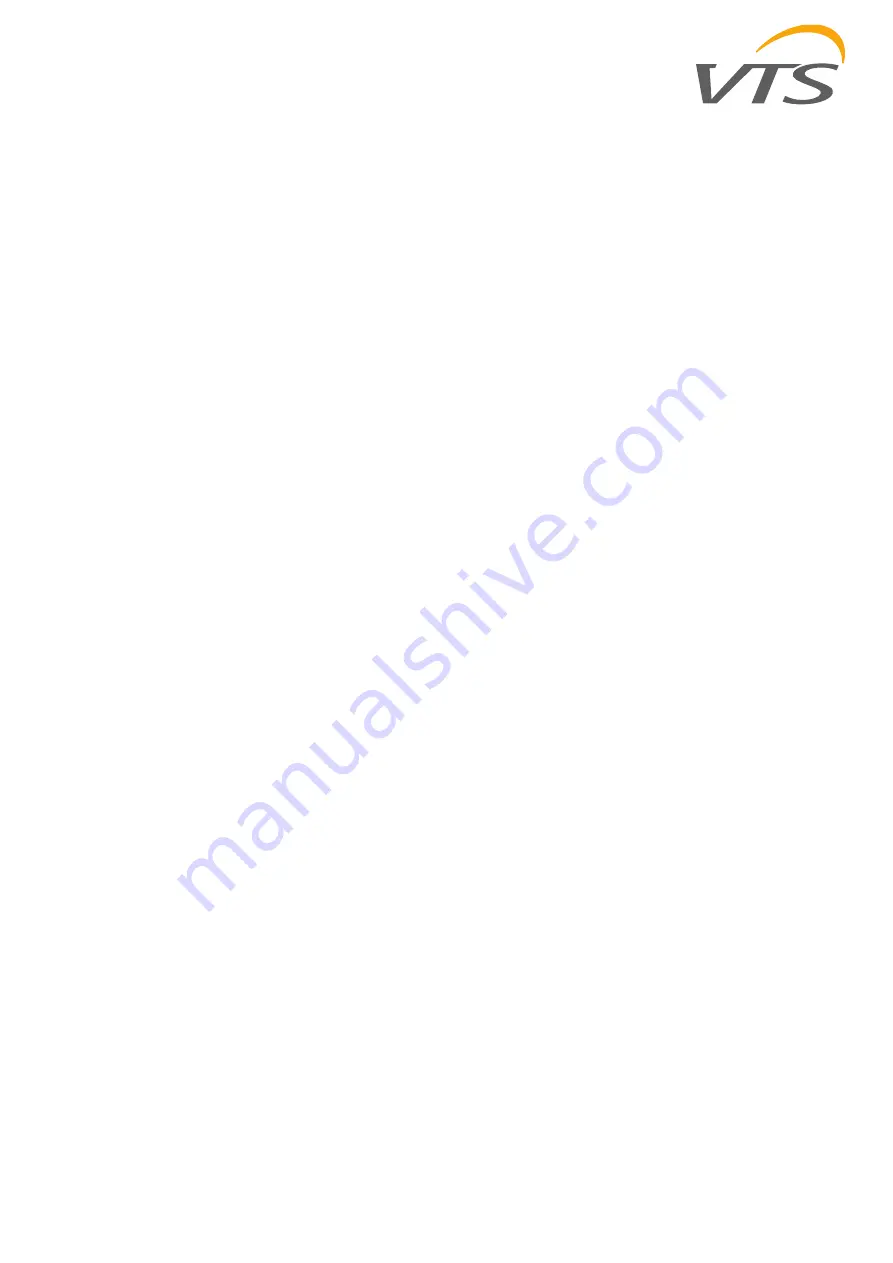
47
VTS reserves the right to implement changes without prior notice
Ventus Air Handling Units
7.3.7 Rotary exchanger
Check the exchanger every four months and inspect its technical condition as well as contamination
level of the rotor. During maintenance activities of the rotary exchanger check if:
- rotor rotates freely. Sensible resistance can be caused by too excessive hold down of sealing
brushes and touching the rotor's edges. In such a situation adjust the brushes properly. Worn out
brushes sealing should be replaced. If previously removed brush sealing is to be installed again, it
should be installed so that its direction should be in line with the rotor's rotation direction. After
replacement or adjustment of sealing brushes, the exchanger should operate 30 minutes so that
the brushes could adapt to the rotor's surface.
After this time check the motor's current and compare it with the rated current in order to find out if
the motor is not overloaded.
- drive belt is not damaged and if it is clean as well as if it does not slip on the cylindrical part of the
rotor. If despite maximal tension by the strain system the clearance still exists, the belt should be
replaced or shortened,
- air inlet holes are not covered with dust or contaminated in any other way. In order to clean the
rotor apply one of the methods designed for other exchangers.
Rolling bearings of rotor and drive motor are greased in continuous manner during operation.
Amount of grease in bearings during the exchanger assembly is enough for long-lasting operation
and there is no need to lubricate the bearings during operation. It is recommended to clean the motor
and gear from dust so as an insulation layer was not formed on the motor's surface which may lead
to increase of drive operating temperate.
7.4 Suppression section
Suppression section is equipped with slotted lever filled with non-flammable mineral wool absorbing
acoustic energy. Maintenance procedures entail checking contamination level of suppression inserts.
If cleaning is necessary the slotted levers can be removed one after another through the section
inspection holes, previously removing screws fastening the levers to the bottom and top. Re-
assembly of the slotted levers in the section should be carried out in reverse order.
leaning should be performed with a vacuum cleaner or wet wiping of all surfaces. In case of more
serious contamination you can use nylon brushes.
7.5 Fan unit
Before starting any kind of works (failure, maintenance, servicing) with AHU, especially in case
opening the inspection panels of fan section as well as removing cover plates under the drive, please
make sure if:
- the device has been properly disconnected from power supply. It applies to both main and
secondary circuits,
- rotor is not rotating,
- fan is cold and the surface temperate is safe,
- the fan is protected against unintended start-up.
7.5.1 Fans
Fans are designed for transferring dust-free of light-dusted air. They are not designed for aggressive
gases, steams or heavy-dusted air. Operating the fan in not suitable environment can lead to
damage of bearings, corrosion, unbalanced rotor or vibrations.
The fan and motor in the unit are designed for particular requirements and operation characteristics.
Fan rotation speed is adapted so as the air stream and complete fan stress concentration were
appropriate for a given ventilation system. Smaller stream of forced air results in disturbances in
correct operation and leads to loss of balance of the entire ventilation system. It can be caused by:
- slipping drive belt,
- dust settlings on the fan's rotor blades,
- incorrect direction of fan's rotations. If the centrifugal fan rotates in incorrect direction, the air flow
is carried out with significantly deteriorated output.
In case of fan maintenance activities check if:
- the rotor rotates freely,
- the rotor is well balanced,
- the rotor is firmly mounted on pivot,
- did not change a location against the inlet funnel,
- vibroisolators (if any) are firmly installed and they are not damaged,