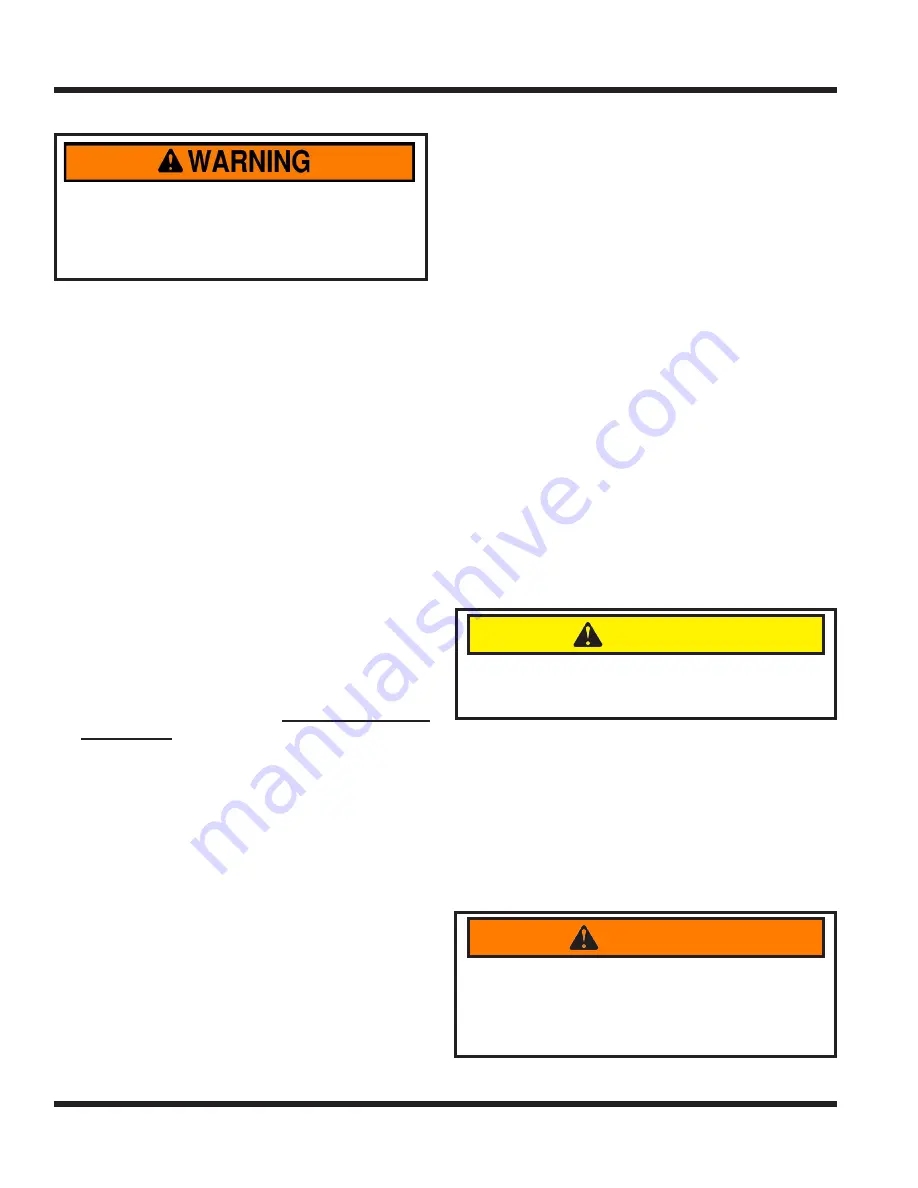
Operation - 14
GENERAL OPERATION
Daily Inspection
1.
Always set the parking brake, shut off power
unit engine, remove the ignition key, and ensure
all moving parts have come to a complete stop
before inspecting components, or attempting
any repair or adjustment.
Park machine on a level surface, with the engine
shut off and all fluids cold.
2. Perform a visual inspection of both the power unit
and the power blower. Look for loose or missing
hardware, damaged components, or signs of wear.
3.
Inspect hydraulic hoses, hydraulic fittings, and
fuel lines to ensure tight, leak free connections.
4. Inspect the power blower belts. Belts should be in
good condition. Service as required.
5. Refer to the power unit operator’s manual.
Check the power unit’s engine oil, hydraulic oil,
cooling system, tire pressure, and fuel level. Add
fluid or service as required.
6. Test the power unit’s operator safety interlock
system*.
Attaching
1. Drive the power unit slowly forward into the hitch
arms of the power blower. Align the lift arms of
the power unit with the power blower hitch arms
by raising or lowering the front hitch and com-
plete the engagement.
2. Once completely engaged, close the front hitch
locking lever.*
3.
Engage the parking brake* and shut off the engine.
4. Place the attachment belt onto the PTO drive
pulley on the power unit. Ensure the belt is prop-
erly seated in each pulley.
5. Engage the PTO tension spring.
6. Wipe hose ends clean, and connect to the
power unit’s hydraulic quick couplers. If
equipped, connect the hoses and quick couplers
so the red indicators are paired together and the
yellow indicators are paired together.
Detaching
1. Park the power unit on a level surface and set
the parking brake.*
2. Lower the power blower to the ground.
3.
Shut off power unit engine.
4. Disengage the PTO tension spring.
5. Remove the attachment belt from the PTO drive
pulley of the power unit.
6. Disconnect the hydraulic quick couplers from the
power unit and store the hose ends in the top
frame holes on the power blower.
7. Disengage the front hitch locking lever*.
8. Restart the power unit and back slowly away
from the power blower.
Manual Blower Rotation
If the power blower is equipped with a manual
rotation lock lever, stop the power unit, engage the
park brake, and disengage the PTO. Pull out on the
handle of the spring loaded lock lever, while turning
the blower housing to the desired direction. Release
the lever to lock the blower housing in position.
Hydraulic Blower Rotation
If the power blower is equipped with hydraulic blower
rotation, rotate the direction of the blower by moving
the power unit’s secondary SDLA lever* to the left or
right. Release the lever when the desired direction
has been achieved. If the rotation action seems back-
wards, reverse the quick coupler connections.
Blower Operation
Lower the power blower to the ground and place the
power unit’s primary SDLA lever* in the float position.
CAUTION
Always use float if the gauge wheels contact the
ground. The power blower gauge wheels are not
designed to carry power unit weight.
The power blower can also be operated while lifted
off the ground.
Set the discharge of the power blower to the desired
direction.
With the power unit’s engine running between 2,000
and 2,500 RPM, engage the PTO switch. Increase
the engine speed until there is sufficient force to
accomplish the blowing task. Full engine speed will
produce approximately 180 mph (290 km/h) wind at
the blower outlet.
WARNING
The power blower produces strong wind speeds
that can cause damage and/or unintentionally
displace things. Never direct the blower discharge
in the direction of people, buildings, animals,
vehicles, or other objects of value.
* Refer to power unit operator’s manual for operation of
power unit controls.