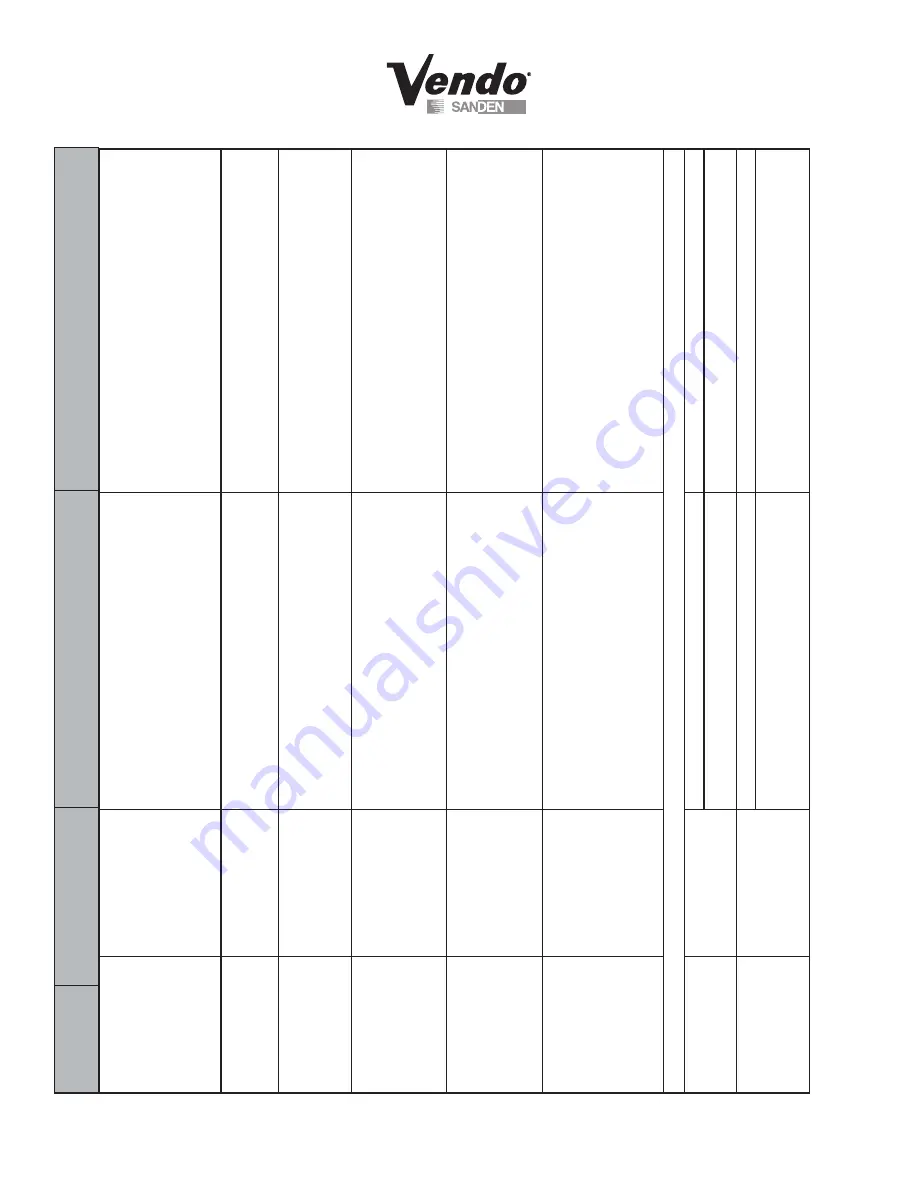
T-6
04/2005
ERROR
DESCRIPTION OF
ERROR CODE
CHECKING METHOD
CORRECTIVE
ACTION
Command Out of
Sequence
The MDB command received
is inappropriate for the
current state of the PDC.
Ex. example, if the V
end
Drop command were
received when the hand is
not waiting at the hopper to
drop a product during a V
end,
Startup, or Recovery
.
PDC will automatically ignore the command.
Command in Progress
T
est/Config Mode command
received while already
executing a
T
est/Config
command.
PDC will automatically ignore the command.
Command Data Out of
Range
T
est/Config Mode command
received that is either an
invalid comand number or
has a parameter that is out of
range for that parameter
.
VMC will retry sending the command to PDC
Command Denied Safely
A
command was rejected
because it is unsafe.
A
T
est/Config Z Movement
command was rejected
because the PDC thinks the
hand is in the pocket at the
bottom of the machine.
PDC will automatically ignore the command.
Shelf Invalid
T
est/Config commands that
have a shelf number as a
parameter can return this
error for a shelf number
, while
in range, which identifi
es a
shelf that does not exist (was
not found during discovery).
Performing Calibrations / Set Z corrections without rumming
discovery can lead to this error
.
Run Discovery 2 before performing Calibration or Corrections.
TC Failed Movement
1.When any one of the
folloing movements in X ,
Y
, Z or Clamp fail during
T
est
Motors.
2. When any of the sensors
fails. ( i.e. X,Y
, Z , Clamp
or Forward Looking Optics
Sensors )
1.Check to see if the X ,
Y
, Z or Clamp movements are
performed. On Exit from
T
est Motors the X,Y
, Z and clamp should
be at home position.
2.Check the Sensors. ( O denotes good sensor
. If the sensor is
blocked - then change the respective sensor )
Run
T
est Motors and Get Sensor Status after performing the checking
method.
V
ending Mechanism - VMC Error
Hop.Flap No Current
Hopper fl
ap motor either did
not run, or no current was
detected.
Check Hopper fl
ap harness connection.
Plug in hopper fl
ap connector
. Run
T
est Hopper Flap in
T
est Mode.
Run
T
est Hopper Flap in
T
est Mode
If motor moves, current detection circuitry has been damaged on VMC.
Replace VMC board.
Hopper Flap Jam
VMC detected high current
while running the Hopper
Flap motor without detecting
the Hopper fl
ap positioning
switch.
Run
T
est Hopper Flap in
T
est Mode
If motor does not move, replace Hopper Flap motor
.
Check to see if product is jamming the Flap
Remove the product. Run Hopper Flap
T
est.
Summary of Contents for VUE 30
Page 1: ......
Page 2: ...i 01 2008 TABLE OF CONTENTS...
Page 5: ......
Page 6: ......
Page 7: ......
Page 8: ......
Page 9: ......
Page 10: ......
Page 11: ......
Page 12: ......
Page 13: ......
Page 14: ......
Page 15: ......
Page 16: ......
Page 17: ......
Page 18: ......
Page 19: ......
Page 20: ......
Page 21: ......
Page 22: ......
Page 23: ......
Page 24: ......
Page 25: ......
Page 26: ......
Page 27: ......
Page 28: ......
Page 29: ......
Page 30: ...CL 1 04 2005 CLEANING INFORMATION SECTION...
Page 33: ...CL 4 04 2005 NOTES...
Page 34: ......
Page 35: ......
Page 36: ......
Page 37: ......
Page 38: ......
Page 39: ......
Page 40: ......
Page 41: ......
Page 42: ......
Page 43: ......
Page 44: ......
Page 45: ......
Page 46: ......
Page 47: ......
Page 48: ......
Page 49: ......
Page 50: ......
Page 51: ......
Page 52: ......
Page 53: ......
Page 54: ......
Page 55: ......
Page 56: ......
Page 57: ......
Page 58: ......
Page 59: ......
Page 60: ......
Page 61: ......
Page 62: ...C 1 11 2007 CABINET SECTION...
Page 63: ...C 2 11 2007 1 2 3 4 5 6 3 7 8 9 10 11 10 10 13 12 14 15...
Page 67: ...C 6 11 2007...
Page 69: ...C 8 11 2007...
Page 72: ...C 11 11 2007 NOTES...
Page 73: ......
Page 74: ......
Page 75: ......
Page 76: ......
Page 77: ......
Page 78: ......
Page 79: ......
Page 80: ......
Page 81: ......
Page 82: ......
Page 83: ......
Page 84: ......
Page 85: ......
Page 86: ......
Page 87: ......
Page 88: ......
Page 89: ......
Page 90: ......
Page 91: ......
Page 92: ......
Page 93: ......
Page 94: ......
Page 95: ......
Page 96: ......
Page 97: ......
Page 98: ......
Page 99: ......
Page 100: ......
Page 101: ......
Page 102: ......
Page 103: ......
Page 104: ......
Page 105: ......
Page 106: ......
Page 107: ......
Page 108: ......
Page 109: ......
Page 110: ......
Page 111: ......
Page 112: ...T 1 04 2005 TROUBLESHOOTING SECTION...
Page 125: ...T 14 04 2005 NOTES...