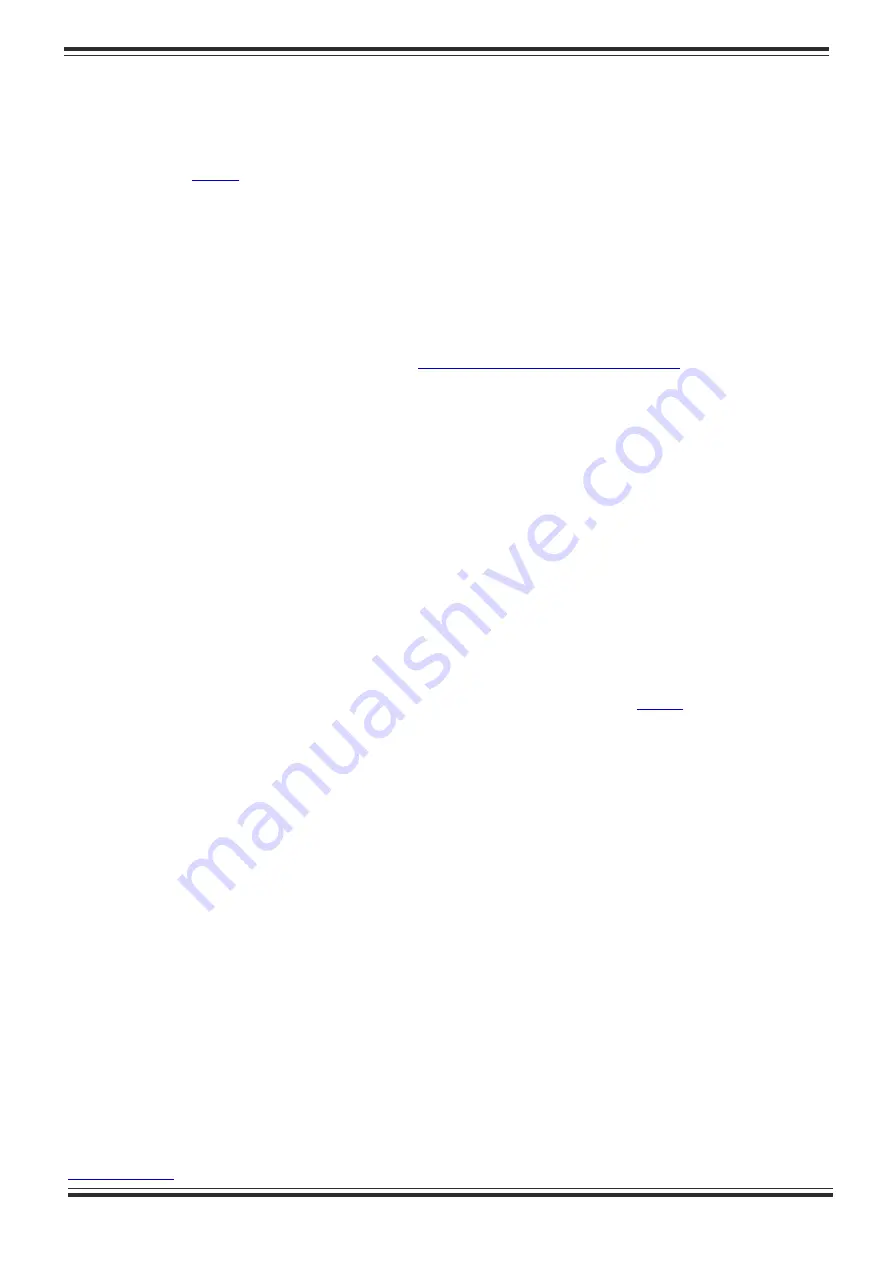
2
Five independent timers in the
are provided to
facilitate the process of welding: pressing time
(
T
), weld time (
T
), pause between
off
on
multiple sparks (
T
), cooling time (
T
) and delay time between welds (
T
) for
repetitive
p
e
d
welding
only.
Parameters and work of the controller
Introduction
Multi-spark welding
is implemented in order to achieve the best quality of
welding, especially for rounded items.
The controller can work in a direct mode of
continuous welding
.
The parameters of the controller are accessed via serial interface RS485 using
the
Modbus RTU protocol
. The welding sequence can be triggered by an external
PLC output, making it possible to integrate the welding controllers
PCN110ZP
in
automatic welding machines with several welding transformers and a complex
sequence of welding operations.
PCN1
10Z
P
power controller is used to regulate the phase angle of AC loads,
such as spot welding machines, both single or two-phase. When used with two-
phase loads
)
, a phase matching transformer
400/230
V is needed, unless it is
not provided in the controlled device. Without such a transformer as a power supply
to
PCN110ZP
, there will be a 30 degrees phase shift between controller and loads,
thus real control will not be possible.
The internal parameters of the controller are listed in the
, along with their
meaning and Modbus addresses. They can be accessed via Modbus functions
0x3
,
0x4
, 0
x6
and
0
x10 on
RS485
(38400
bps
, 8-
N-1
)
.
Modbus ID can be selected bitwise
by the
DIP-switch under the front panel of the controller
.
The welding controller works in the standard sequence of processes: pressing,
welding current in sparks/impulses, cooling off. The digital input
In
triggers one such
cycle. At the beginning of welding, the output for pressing and the
(
OUT
)
LED will
switch ON
,
the
(
RUN
)
LED will flash during initial pressing time
T
and then remain
off
illuminated during the actual welding
T
. The flashing of (
RUN
) will occur also during
on
the pauses between impulses
T
and during the final cooling stage
T
. After welding is
p
e
finished, the output and the two LEDs will switch OFF.
Powering up the controller with the digital input ON will invoke
collision
and the
input should be switched off before any further operation. Collision will occur also if
the input is re-enabled during the cooling phase of the previous welding.
he output power, regulated by the
PCN1
1
0ZP
, is divided to 100 units
(percentage of the full power). The value of 0 means that the power output of the
controller is off, whereas 100 means that it will transmit the full input power. The
for output power for each impulse are
SP
,
SP
and
SP
.
2
3