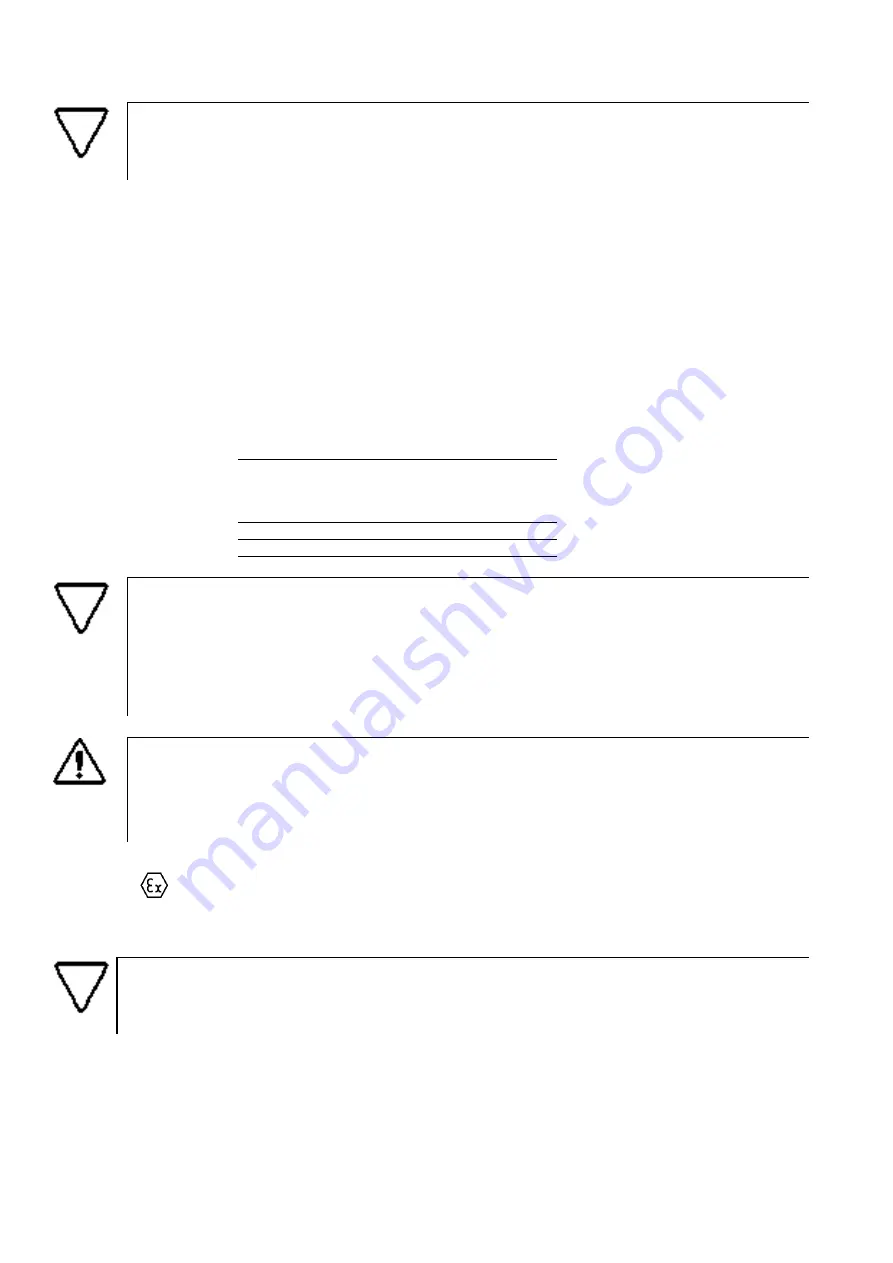
Lubrication
Please note!
In order to avoid damage the bearings and grease must be kept clean.
The deep groove ball bearings of motors up to frame size 280 are sealed on both sides and filled by the bearing manu-
facturer with a grease which is enough for normal operating conditions in 4 or multi-pole motors for 40000 operating
hours or in 2-pole motors for 20000 operating hours.
When changing the bearings, change also the shaft seals. To do so, dismount the motor so that the winding can be
cleaned at the same time. Disassembly and assembly as per the specific manufacturer repair instructions.
Motors starting from frame size 315 and motors with reinforced bearings are to be equipped with regreasing devices.
The bearings are to be regreased preferably with the motor running with a grease gun through the grease nipples lo-
cated over the bearing plates or bearing caps.
The drip space in the bearing cap for outflowing old grease is large enough to collect the outflowing grease during the
nominal bearing service life with state-of-the art regreasing.
See the plate on the motor for the specified lubricating intervals and the type and quantity of grease to be used. The
manufacturer normally uses ESSO Unirex N3, a lithium complex soap/mineral oil grease.
Table 10:
Standard regreasing intervals in hours
Ambient
temperature
Rpm up
to 1800 min
–1
Rpm up
to 3600 min
–1
40 °C
5000 h
2500 h
50 °C
2500 h
1000 h
Please note!
In motors with enhanced performance (motor type ...X), in heavy drive conditions like belt and gear
drive with additional bearing loads and in vertical designs the lubricating intervals are to be reduced
by 50%.
Observe the specified quantity of grease. Overgreasing can lead to a sharp increase in the bearing
temperature and hence to the failure of the bearing.
Caution!
If regreasing is carried out while the motor is running, provide for adequate protection against rotat-
ing parts!
Only resin-free and acid-free anti-friction bearing grease with a drop point of approx. 200°C is to be
used.
Explosion protection
The marking
(II2G), EEx de IIC T4, for instance, indicates where the motor is to be used and that it has been de-
signed, built and approved according to the relevant European standards required for operation in areas subject to
explosion hazards.
Please note!
The motor must not be altered in any way whatsoever and the operating instructions set forth
herein are to be complied with always.
If the motor is altered or repairs need to be made, these are to be performed by the manufacturer or by repair work-
shops or factories that possess the necessary know-how. Before the starting the motors again, conformity with the
requirements of EC directives 76/ 117/EEC or 94/9/EC and 99/92/EC by said sites is to be ascertained and confirmed
by means of an appropriate marking on the motor or by issuing a test report.
If these requirements are not met, the motor is no longer classified as explosion-protected and the marking - see
above - is to be removed.