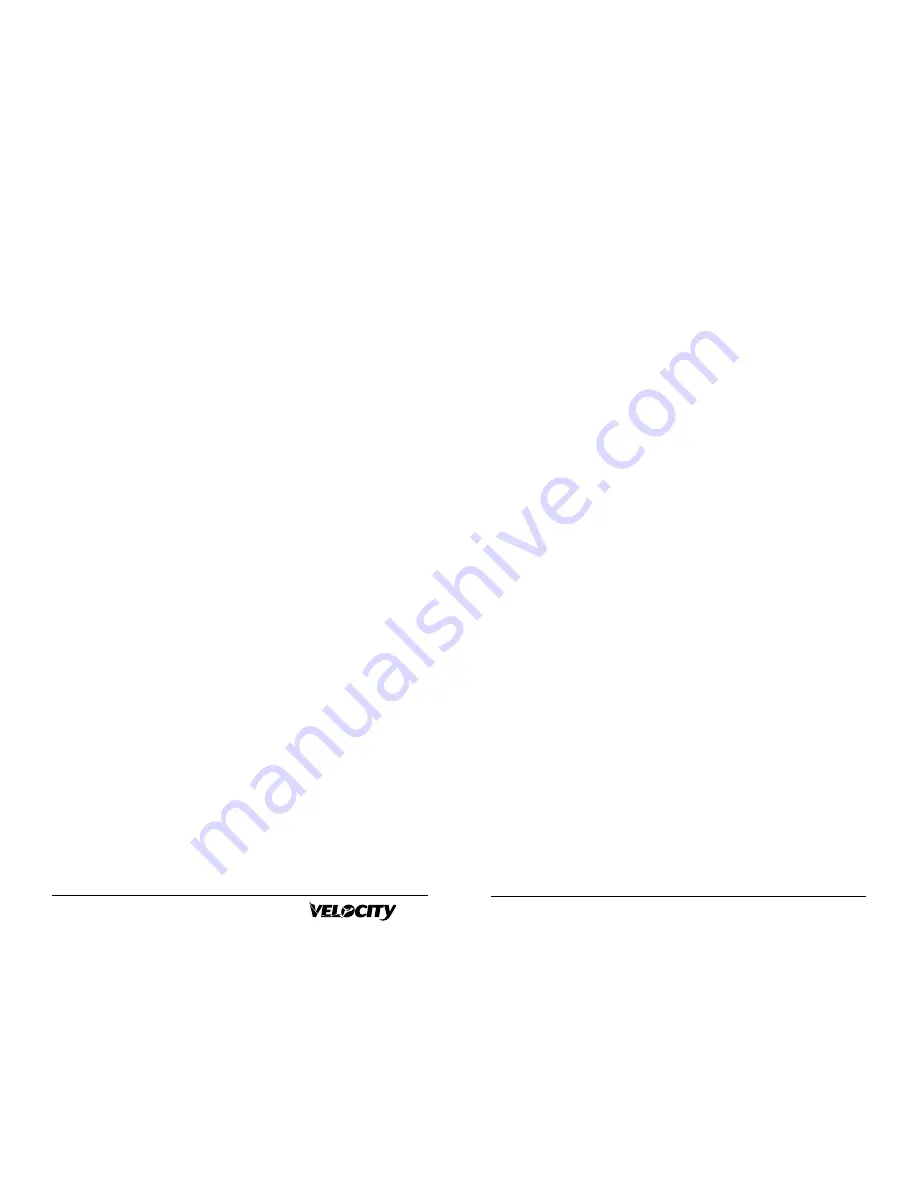
O
WNER
’
S
F
LIGHT
M
ANUAL
43
42
XL
• Propeller bolts for proper torque (refer to prop mfg recom-
mendations) and safetying
• Propeller track and cracks
• Spinner track and cracks
• Engine mount bolts for security and safety
• Oil level
• Mixture, throttle, carb heat controls for security and proper
function
• Magneto wiring. Be sure the mags are cold when the switches
are off.
• Check that the magneto impulse coupling clicks at, or after, top
dead center.
• Cowling baffles must fit tight all around the engine and cowl. If
not, overheating will result.
Fuel System
• Check that the fuel caps seal securely and the vent system is
clear without leaks.
• Calibrate your fuel gauges with the aircraft level.
CAUTION: Under no circumstances should fuel of a lower
octane rating than that specified by the manufacturer for your
engine be used. Be sure the minimum octane is clearly labeled by
each fuel cap. Color coding for 80/87 is red, 100LL is blue and
100/130 is green.Auto gas, especially the high aromatic content
no-lead, should NEVER be used.
Weight and Balance
Your final weighing before initial flight tests is very important
and should be done carefully.The measurements taken should be
recorded in the airframe log book and used in the weight and bal-
ance data kept aboard the airplane (see weight & balance section).
When loading the aircraft for the initial flight testing and for
initial pilot checkouts, it is important that the weight and CG fall
in the first flight box (see weight and balance section).
ances. Binding can occur at elevated load factors if clearance is
too small.
Landing Gear
MAIN GEAR:
• Double check that all attach bolts and axle bolts are installed
and secured.
• Check tires for proper inflation pressure (45 psi, wait 24 hours
and see if they leak).
• Adjust brakes and test for proper function. Service with fluid as
required. Bleed by flowing from drain up to master cylinder.
Recheck rudder travel 1.5” to 1.75”.
• Double check for proper main tire toe-in (1/4 to 1/2 degree
per side)
• Wheel bearing packed with grease and safetied
• Brake mechanism for safetying
NOSE GEAR:
• Nose gear tire inflation, 45 psi
• Axle nut for security and proper installation
• Shimmy damper for friction adjustment (10-12 lb. side force at
axle is required to rotate pivot)
Instrumentation
• Cylinder head temp, Oil temp, Exhaust gas temp - it is impor-
tant these gauges be accurately calibrated prior to use.This can
be accomplished using hot oil and a high-temp candy ther-
mometer.
• Pitot/static systems - leak check
• Oil Pressure,Tachometer, Fuel Pressure - Function check on
initial engine run
Powerplant
Check:
• Clock the prop for compression at the 10 o’clock position for
proper hand-propping
Summary of Contents for XL RG
Page 1: ......