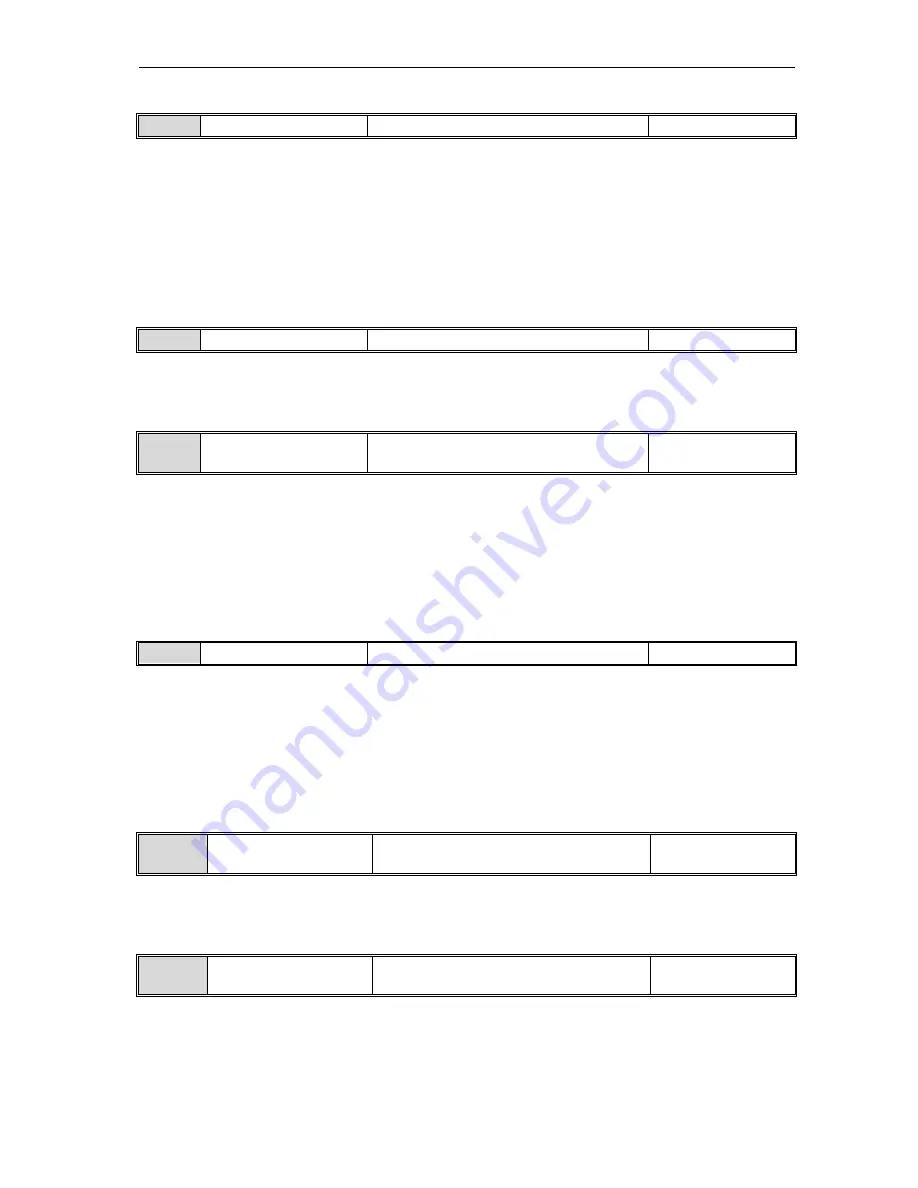
AC90 TENSION CONTROL FREQUENCY INVERTER MANUAL
Function Parameter specifications
143
9.15
Communication control function parameters
Fd.00 Main-slave
machine
Setting range: 0-1
Factory set: 0
Take inverter as main machine or slave machine while Modbus communication. Details for Modbus refer to Appendix
2:RS485 communication protocol.
0: Slave machine
Inverter is slave machine. Communication address is decided by
[Fd.01]
. Inverter accepts order
form main machine and reply or not while writing operation according
[Fd.08]
setting. Reply delay time is set by
[Fd.05]
.
1: Main machine
Inverter, as main machine, sends data to communication net by broadcast orders. All slave machines
accept orders from main machine. Mian machine sending data is set by
[Fd.09]
.
Fd.01
Machine add
Setting range: 1-247
Factory set: 1
It set communication address while inverter is slave machine. If inverter is main machine, this parameter is no meaning.
0 is broadcast address.
Fd.02
Communication baud rate
selections
Setting range: 0-5
Factory set: 3
0:1200 bps
1:2400 bps
2:4800 bps
3:9600 bps
4:19200 bps
5:38400 bps
Fd.03 Data
format
Setting
range: 0-5
Factory set: 0
0: (N, 8, 1) no checkout, Data digit: 8, Stop digit: 1
1: (E, 8, 1) even checkout, Data digit: 8, Stop digit: 1
2: (O, 8, 1) odd checkout, Data digit: 8, Stop digit: 1
3:(N,8,2) no checkout,Data digit:8, Stop digit:2
4:(E,8,2) even checkout,Data digit:8, Stop digit:2
5:(O,8,2) odd checkout,Data digit:8, Stop digit:2
Fd.04
Communication ratio
setting
Setting range: 0.00-5.00
Factory set: 1.00
The result of upper machine multiply this parameter is communication giving or feedback of this machine. Upper
machine communication order can be modified pro rate.
Fd.05
Communication answer
delay
Setting range: 0-500ms
Factory set: 0ms
While delay time is shorter than system dealing time, real delay time is same as system dealing time. While delay time
is longer than system dealing time, it has to delay while system dealing finished. It does not send data to upper machine
until delay time arrive.