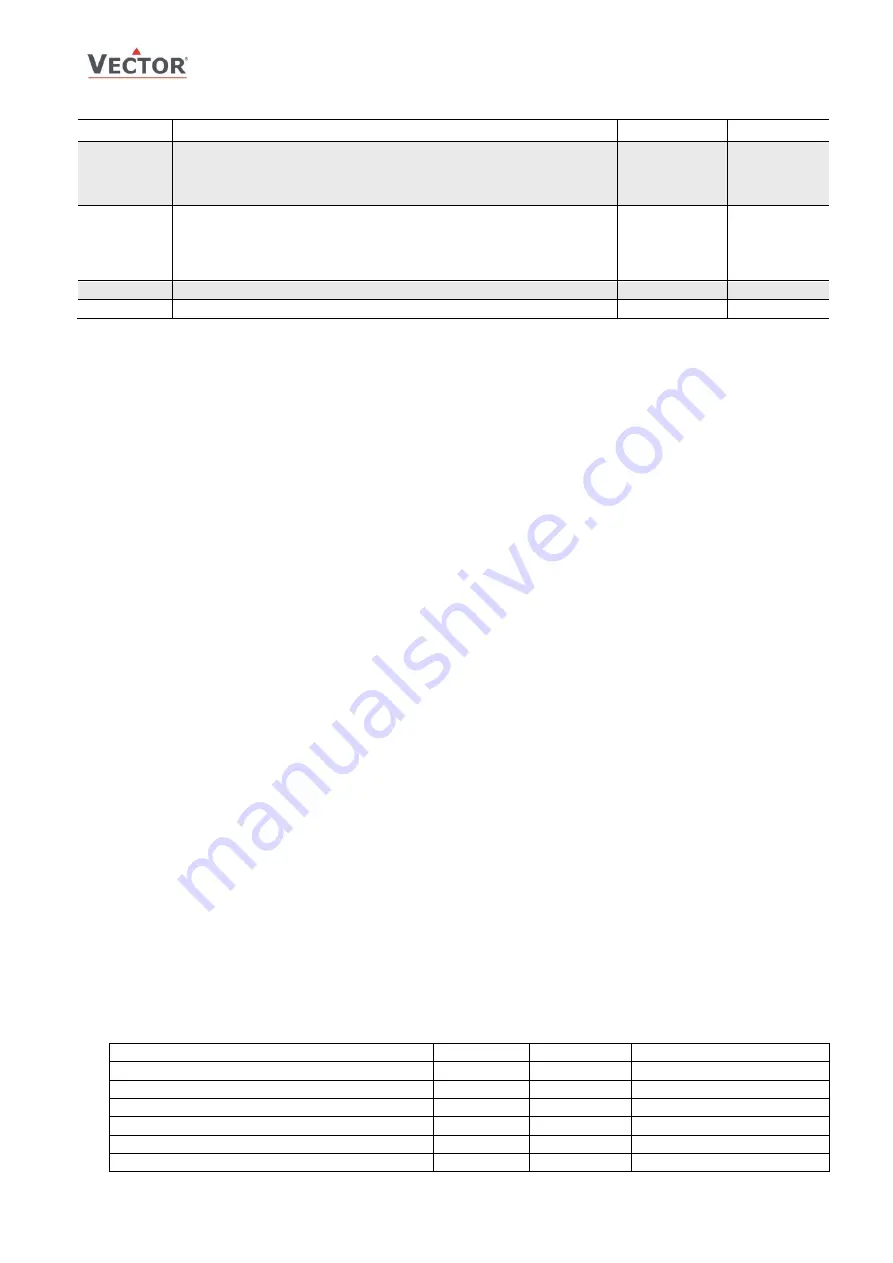
TLC3-BCR-U Thermostat
C
ONTROL
C
ONFIGURATION
Doc: 70-00-0294, V3.1, Date: 20140508
© Vector Controls GmbH, Switzerland
Page 9
Subject to alteration
Output configuration
Parameter Description
Range
Default
CP 13
Output setting, Binary, PWM or 3-point:
0 = Binary or PWM (See CP14 for assignment of Y1 and Y2)
1 = 3-point binary output (Y1 open, Y2 close)
2 = 3-point floating output (Y1 open, Y2 close)
0…2
0
Binary / PWM
CP 14
Reversing valve in binary mode
0 = no reversing valve, one stage only (Y1 Heating, Y2 Cooling)
1 = rev. valve while heating (Y1 stage 1, Y2 rev valve)
2 = rev. valve while cooling (Y1 stage 1, Y2 rev valve)
3 = no reversing valve, two stages (Y1 stage 1, Y2 stage 2)
0...3
0
CP 15
Running Time in 3-point mode
0…255 s
90 s
CP 16
PWM cycle time, 0 disables PWM mode
0…100 min
0
On-Off control
Two devices may be controlled in case the output setting is 0 (CP13). Y1 controls a heating and Y2 a cooling
device if in single stage mode. If in 2-stage mode (CP14 = 3) Y1 controls stage 1 and Y2 stage 2. The switching
span for stage 2 is defined by the P-band (X
PH
, X
PC
).
PWM output:
Fine tuned proportional control with one binary output is possible thanks to Pulse Width Modulation (PWM).
Conventional fan coil controllers will operate in an on-off control mode. The valve is opened until the setpoint is
reached and then closed. As heating or cooling systems are normally slow acting (heating slower than cooling),
this will lead to a relatively wide fluctuation of the room temperature as the temperature will overshoot the
setpoint and undershoot the hysteresis.
With PWM the ON-OFF ratio of the output is determined by the proportional controller. The interval is the PWM
cycle time. We recommend 8 min for cooling systems and 15min for heating systems. Cycle times depend on the
room and the heating or cooling device.
Set the cycle time to 0 to disable PWM and activate conventional on-off control mode (Factory default).
3-point output
A 3 point actuator has an open and a close input. Applying power to the open input will drive the valve or damper
open, applying power to the close input will drive the valve or damper to the closed position.
The running time of the actuator may be preset. We recommend to enter the maximum running time under
maximum load in order to make sure that the valve can fully close and fully open in any circumstance.
In order to open the valve or damper Y1 will be activated for the preset amount of time. After the expiration of
the running time Y1 and Y2 will be OFF. The valve is closed by activating Y2 for the preset amount of time.
3-point on-off mode
In on-off mode the actuator is either fully opened or fully closed. This is used for some (mostly fast running) zone
valves that are not equipped for frequent start – stop cycles. Binary control is active in this mode.
3-point floating mode
The actuator position is modulated by the controller using proportional control. The position is calculated based on
summarized opening and closing times. The software contains a synchronization algorithm to guarantee accurate
positioning even after extended running time. Proportional control is active.
Reversing valve
In binary output mode a reversing valve option is available. A reversing valve is used where a compressor is used
to generate heating and cooling. Select 1 if the reversing valve is to be activated while in heating mode, select 2 if
the reversing valve is active while the unit is in cooling mode.
The reversing valve will open based on its settings once the operation mode is ON and the either the heating or
the cooling sequence is active.
Control Logic if CP13 = 0
The proportional control function calculates the output based on the difference between setpoint and measured
value. The proportional band (P-band) defines the difference between setpoint and measured value which will
result in a 100% output. For example, with a heating or reverse 0-10v control sequence, and a 2.0°C (4.0°F) P-
band value, at 10v the controller will be 2.0°C (4.0°F) below setpoint. This is the working range of the
proportional control sequence.
System type
CP14
Y1
Y2
2 pipe system heat or cool
0
Heat
Cool
4 pipe system Heating mode
0
Heat
4-pipe system Cooling mode
0
Cool
4-pipe reversing valve on Heat
1
Stage 1
Rev valve (in heat mode)
4-pipe reversing valve on Cool
2
Stage 1
Rev valve (in cool mode)
2-pipe system heat of cool, 2 stages
3
Stage 1
Stage 2