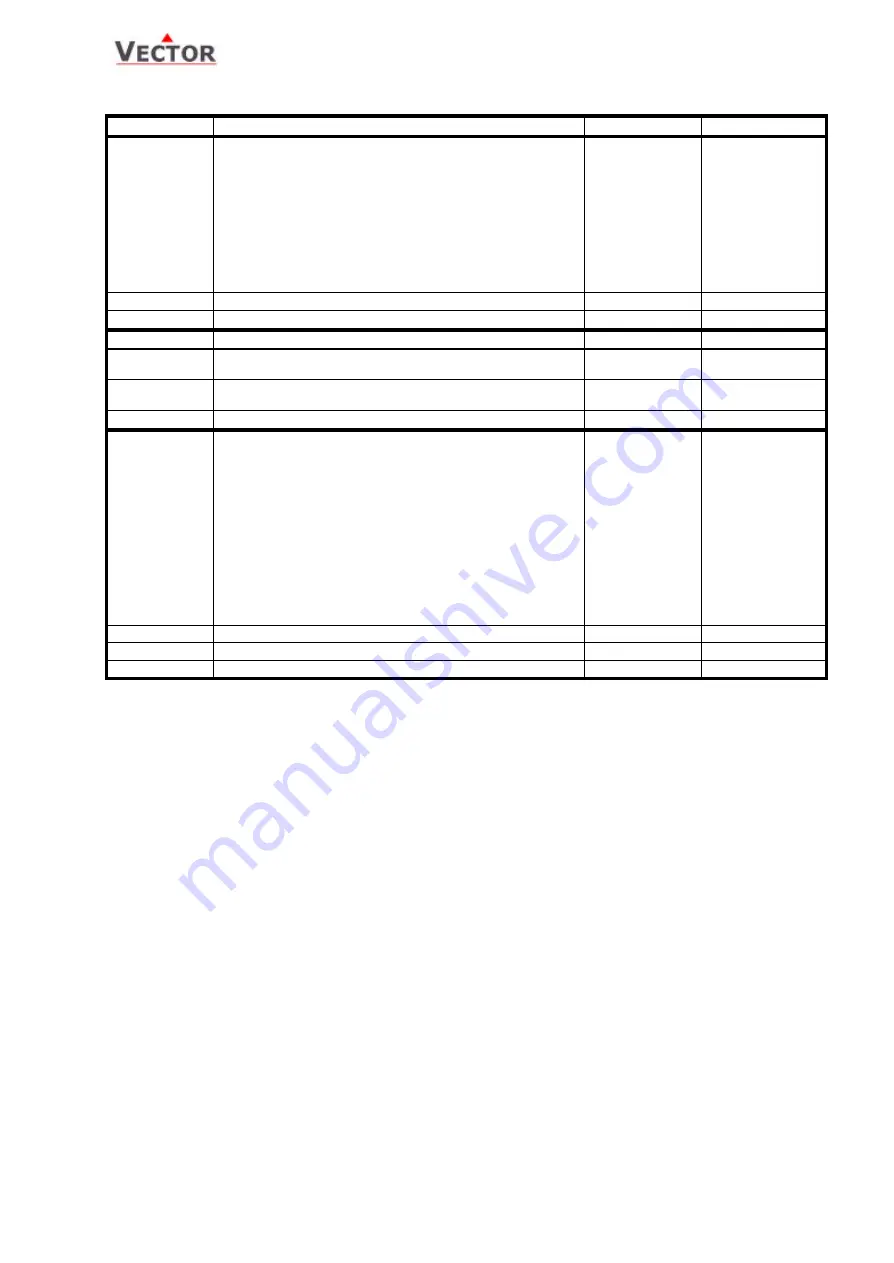
TCY-T0121 Intelligent Compact Controller
Version: 2004-07
Page 9/12
Output configuration
Parameter
Description
Range
Standard
OP 00
Configuration Output AO 1:
0 = OFF,
1 = Temperature Control Heating
2 = Temperature Control Cooling
3 = Temperature Control Heating and Cooling (2-pipe systems)
4 = Universal Control Loop Reverse Acting
5 = Universal Control Loop Direct Acting
6 = Universal Control Loop Reverse and Direct Acting
(2-pipe systems)
7 = Manual override (0 – 100%)
8 = Temperature indication 0 – 50°C
0 – 8
1
OP 01
Minimum limitation of output signal AO 1
0 – Max %
0
OP 02
Maximum limitation of output signal AO 1
Min – 100%
100%
OP 03
Enable Floating Output AO 2 (DO1, DO2 Floating)
ON – OFF
OFF
OP 04
Configuration Output AO 2 (DO1, DO2 Floating)
(if OP-03 is ON) See Parameter OP-00
0 – 7
0
OP 05
Running Time of AO 2 (Time to run from Open to Close or Close to
Open)
0 – 2500 s
90s
OP 06
Switching difference for floating signal
0 – 100%
2 %
OP 07
Configuration Output DO1 (only if OP3 = OFF)
0 = OFF
1 = 1. Stage, Heating
2 = 1. Stage, Cooling
3 = 1. Stage Heating and Cooling (2-pipe systems)
4 = 2. Stage, Heating
5 = 2. Stage Cooling
6 = 2. Stage Heating and Cooling (2-pipe systems)
7 = 2 point control Universal Loop, Reverse Acting
8 = 2 point control Universal Loop, Direct Acting
9 = 2 point control Universal Loop, Reverse and Direct Acting
(2-pipe systems)
10 = Controlled by time schedule (Deluxe only)
(Use specific time schedule for this output)
0…10 (Deluxe)
0…9 (Standard)
0
OP 08
Configuration Output DO2, (only if OP3 = OFF) see OP 07
0…10, 0…9
0
OP 09
Temperature feedback minimum temperature
-40…215 °C/F
0 °C
OP 10
Temperature feedback span
0...255 °
50 °
Mechanical Design and installation
The unit consists of three parts: The mounting plate, the power case and the front part, consisting of a module and
an outside frame. The outside frame may be replaced with a special design based on interior design and taste of the
end user. Please talk to your dealer regarding different designs, materials and colors available.
Installation
1. Arrange the wires to be connected and cut them to equal length.
2. Connect them to the terminals of the power case according to wiring diagram
3. Clip the power case to the mounting plate; pull the connection cable through the large central opening of
the mounting plate. Insert the power case into the flush mounting box. Carefully arrange power wires.
4. Install the mounting plate to the flush mounting box. Make sure that the nipple with the front holding screw
is facing to the ground. Make sure the screw heads do not stand out more than 5 mm of the surface of the
mounting plate.
5. Connect the 6-wire connection cable to the plug located on the back of the front part.
6. Slide the two latches located on the top of the front part into the hooks of the mounting plate.
7. Lower the front part until located flat on the wall and the mounting plate is not visible anymore. Make sure
the connection cable does not get into the way.
8. Tighten the front holding screw to secure the front part to the mounting plate.
Mounting location
•
On an easy accessible interior wall, approx. 1.5 m above the floor in an area of average temperature.
•
Avoid direct sunlight or other heat sources, e.g. the area above radiators and heat emitting electrical
equipment.
•
Avoid locations behind doors, outside walls and below or above air discharge grills and diffusers.
•
Location of mounting is less critical if external temperature sensors are used.