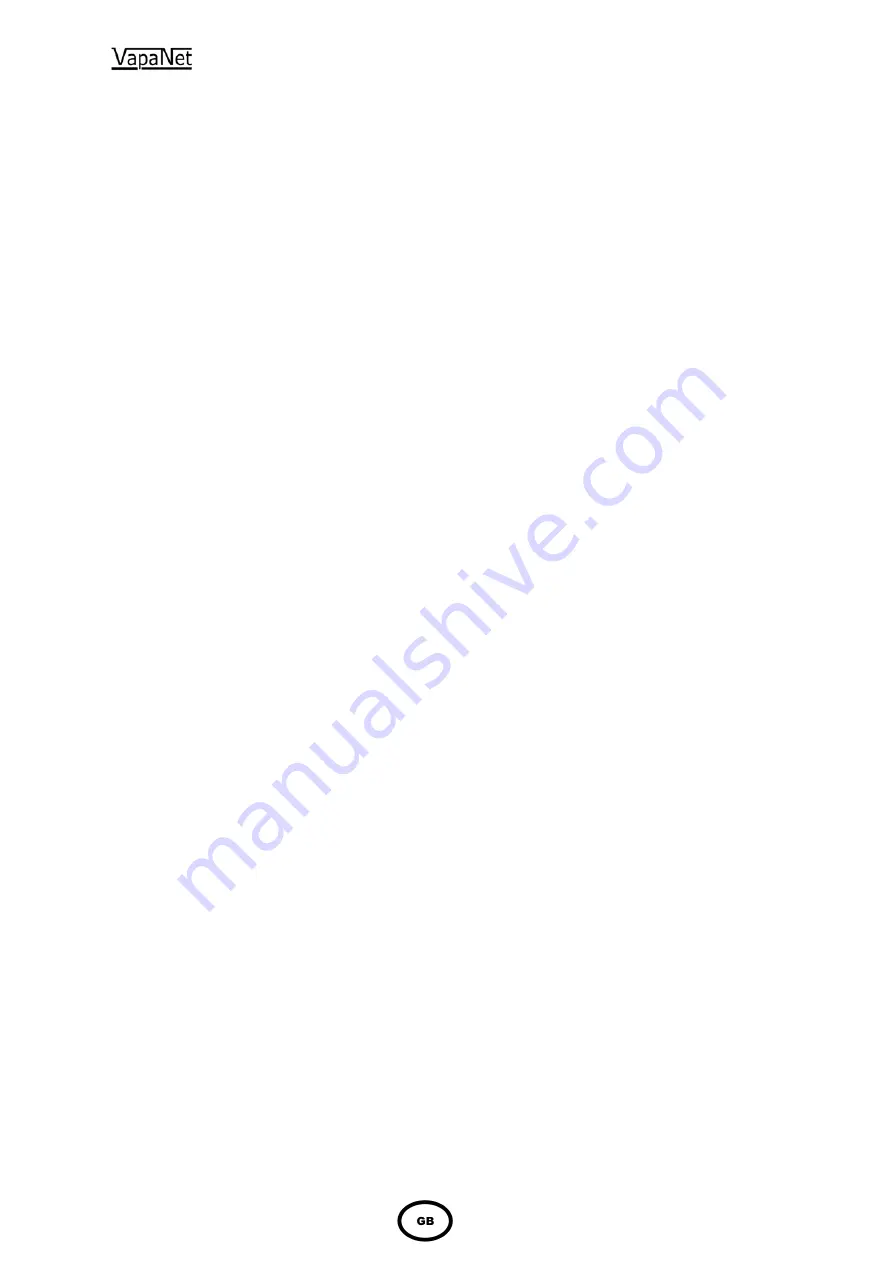
20
4.0 Trouble-shooting
Check
List
-
Use manual drain option to check pump operation
Check/Cause/Remedy
-
Check main power is connected and switched on.
-
Check power supply fuses.
Preliminary
Symptom
Power-On Neon – Off
Symbol-LED – Off
Display - Blank
Power-On Neon – On
Symbol-LED – On
Display - Blank
-
Check if security circuit is open circuit
-
Check 24V 6.3A fuse mounted at top of Microvap controller PCB 1150630
Automatic STOP – Feed Fault indicated on the Display.
Possibilities
Water is not connected
Water connected but not
reaching cylinder.
Water in cylinder and
overflowing
.
Checks
-
Check water stop valve is open
-
Check internal Vapac hose connections for a leak.
-
Check float switch operation
Unit On-Line but inadequate or no steam production
.
Possibilities
Contactor not made
MCB’s tripped
SSR’s not switching
Checks
-
Contactor coil, Float switches, Control PCB.
-
Cylinder Inspection, inspect elements, and float switch operation.
-
SSR Check as described below,
Important
Equipment needed
Procedure
SSR Replacement
Automatic Stop – Drain Fault indicated on the display.
Specialised check of the Solid State Relay
The following check should be carried out by a competent electrician
-
An AC Voltmeter, multi-meter set to full AC line voltage or suitable voltage test
instrument.
-
Remove access panels from both the steam cylinder and electrical compartments
-
Ensure that the humidifier has an operational level of water in the cylinder. Switch
unit on and check that the display indicates “Vapac on line”.
-
Apply the voltmeter, set to the ful line Voltage, across the output terminals of the
SSR being tested (i.e. the two terminals carrying the cabling to the elements).
Correct Voltmeter Response – oscillating between full and near zero Voltage.
If Voltmeter reads a constant near zero Volts, Check:
a) That the unit is not feeding water – if it is, wait until the feed valve closes and then
re-check. (reason the SSR will hold closed while the feed valve is open).
b) That the control PCB is giving the correct pulsed D.C. signal (approx 5V D.C.) to the
SSR control input terminals.
A faulty SSR should be replaced
with an SSR of the same (or higher) Voltage and
amperage rating. Disconnect the unit from the electrical supply. Disconnect the
SSR and undo the mounting screws. The SSR is bedded in thermal compound
to assist heat transfer – it is important that this is cleaned off, and a layer fresh
compound placed under the replacement SSR. When it is secured in position.
Reconnect the SSR, reconnect the electrical supply and check the SSR
function as above before replacing the access panels.
Note: Use proprietary thread locking compound on the line voltage
Possibilities
Drain pump function impaired
Float switch failure
Cylinder O/Let Blocked
Checks
-
If pump will not function, empty cylinder by disconnecting at the tundish fill-cup the
water supply hose to the cylinder and draining the water into a bucket. Remove,
dismantle and clean pump.
-
Check float switch operation
-
Check & unblock