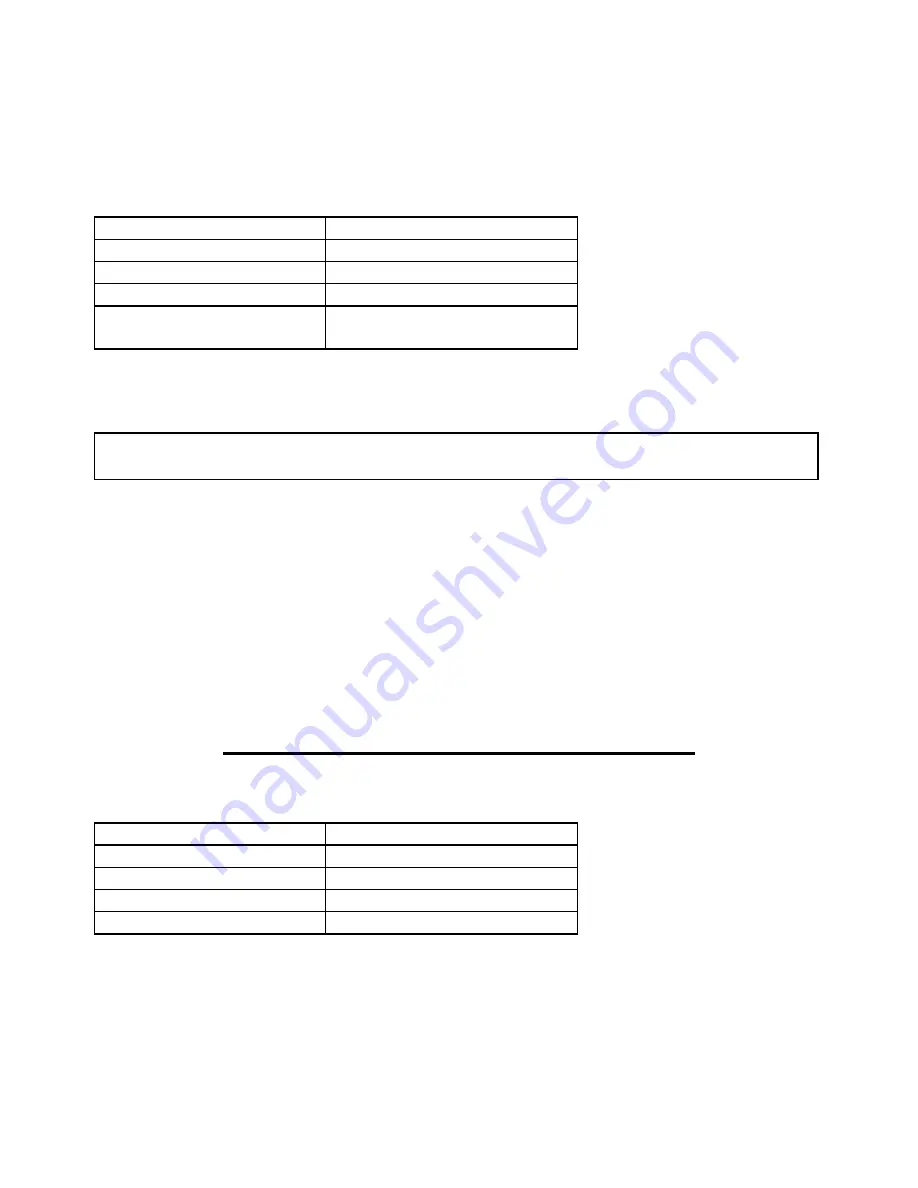
Rev: 2
Date: 11/15/18
6-8
page 5-20, Figure 16
.
5. Installation procedure is reverse of the removal procedure.
R
UDDER PEDAL REMOVAL
Expendable
Cotter pins
Replaceable
Rudder pedal
Service Rating
Line
Minimum Certification
LSA-RM, or A&P
Additional References
KAI Section 28
Matco user manual
1. Remove the fwd. tunnel side covers. (3-4)
2. Remove the rudder pedal access cover (directly aft of the horizontal tubes of the
rudder pedals) and hardware; screws (10)
●
NOTE:
T
HE MASTER CYLINDERS CAN BE REMOVED WITHOUT DISCONNECTING THE
BRAKE LINES
.
3. Label, and then remove the master cylinders (4) from the rudder pedals. (7-3)
4. Remove the rudder cable hardware from each rudder cable; cotter pin, bolt,
washers (3) and nut.
5. Remove the rudder pedal-block hardware; bolts (2) and washers (2), from each
of the rudder pedal-blocks (3).
6. Remove rudder pedal assembly.
I
NSTALLATION
1. Installation procedure is reverse of the removal procedure.
SERVICE SCHEDULE PROCEDURES
C
ONTROL SYSTEM ROD END LUBRICATION
Expendable
Spray lubricant
Replaceable
None
Service Rating
Line
Minimum Certification
LSA-RM, or A&P
Additional References
KAI Section 32
1. Remove the seat ramp covers, aft center console, and aft baggage floor cover.
(3-4)
Summary of Contents for RV 12iS
Page 1: ...Rev 2 Date 11 15 18 i MAINTENANCE MANUAL Aircraft Serial Number ___________________________...
Page 2: ...Rev 2 Date 11 15 18 ii THIS PAGE INTENTIONALLY LEFT BLANK...
Page 52: ...Rev 2 Date 11 15 18 3 18 THIS PAGE INTENTIONALLY LEFT BLANK...
Page 84: ...Rev 2 Date 11 15 18 5 30 THIS PAGE INTENTIONALLY LEFT BLANK...
Page 94: ...Rev 2 Date 11 15 18 6 10 THIS PAGE INTENTIONALLY LEFT BLANK...
Page 125: ...Rev 2 Date 11 15 18 10 5 SERVICE SCHEDULE PROCEDURES NONE...
Page 126: ...Rev 2 Date 11 15 18 10 6 THIS PAGE INTENTIONALLY LEFT BLANK...
Page 145: ...Rev 2 Date 11 15 18 13 1 Chapter 13 FUEL SYSTEM ULS SYSTEM iS SYSTEM...
Page 148: ...Rev 2 Date 11 15 18 13 4...
Page 149: ...Rev 2 Date 11 15 18 13 5...
Page 170: ...Rev 2 Date 11 15 18 15 6 THIS PAGE INTENTIONALLY LEFT BLANK...
Page 174: ...Rev 2 Date 11 15 18 16 4 THIS PAGE INTENTIONALLY LEFT BLANK...
Page 178: ...Rev 2 Date 11 15 18 17 4 THIS PAGE INTENTIONALLY LEFT BLANK...
Page 180: ...Rev 2 Date 11 15 18 18 2 THIS PAGE INTENTIONALLY LEFT BLANK...
Page 182: ...Rev 2 Date 11 15 18 18 4 THIS PAGE INTENTIONALLY LEFT BLANK...
Page 184: ...Rev 2 Date 11 15 18 18 6 THIS PAGE INTENTIONALLY LEFT BLANK...
Page 186: ...Rev 2 Date 11 15 18 18 8 THIS PAGE INTENTIONALLY LEFT BLANK...
Page 188: ...Rev 2 Date 11 15 18 18 10 THIS PAGE INTENTIONALLY LEFT BLANK...
Page 190: ...Rev 2 Date 11 15 18 18 12 THIS PAGE INTENTIONALLY LEFT BLANK...
Page 192: ...Rev 2 Date 11 15 18 18 14 THIS PAGE INTENTIONALLY LEFT BLANK...
Page 194: ...Rev 2 Date 11 15 18 18 16 THIS PAGE INTENTIONALLY LEFT BLANK...
Page 196: ...Rev 2 Date 11 15 18 18 18 THIS PAGE INTENTIONALLY LEFT BLANK...
Page 198: ...Rev 2 Date 11 15 18 18 20 THIS PAGE INTENTIONALLY LEFT BLANK...
Page 200: ...Rev 2 Date 11 15 18 18 22 THIS PAGE INTENTIONALLY LEFT BLANK...
Page 202: ...Rev 2 Date 11 15 18 18 24 THIS PAGE INTENTIONALLY LEFT BLANK...
Page 204: ...Rev 2 Date 11 15 18 18 26 THIS PAGE INTENTIONALLY LEFT BLANK...
Page 206: ...Rev 2 Date 11 15 18 18 28 THIS PAGE INTENTIONALLY LEFT BLANK...
Page 208: ...Rev 2 Date 11 15 18 18 30 THIS PAGE INTENTIONALLY LEFT BLANK...
Page 209: ...Rev 2 Date 11 15 18 18 31 3 VIEW...
Page 210: ...Rev 2 Date 11 15 18 18 32 THIS PAGE INTENTIONALLY LEFT BLANK...
Page 212: ...Rev 2 Date 11 15 18 18 34 THIS PAGE INTENTIONALLY LEFT BLANK...
Page 216: ...Rev 2 Date 11 15 18 19 4 THIS PAGE INTENTIONALLY LEFT BLANK...