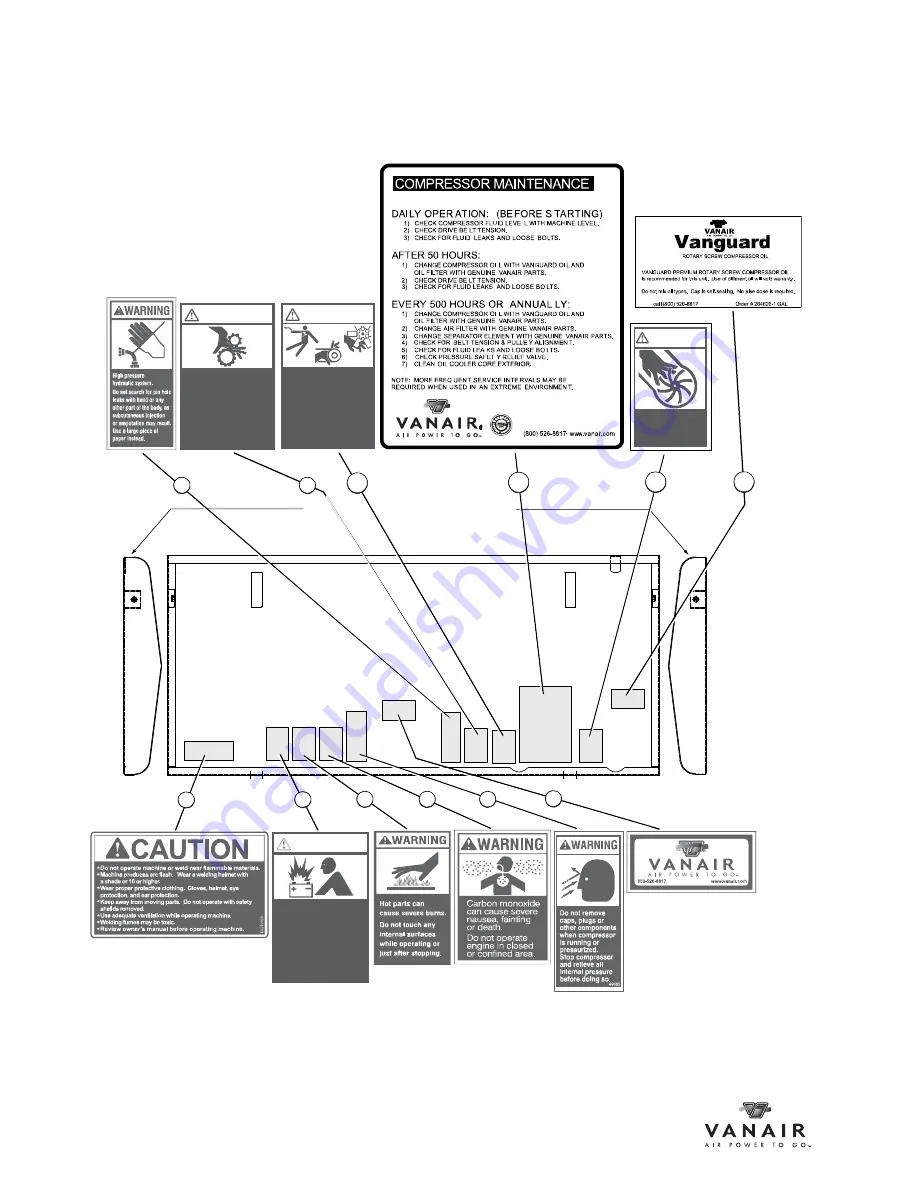
SECTION 9: ILLUSTRATED PARTS LIST
AIR N ARC
®
300 SERIES ALL-IN-ONE POWER SYSTEM
®
PAGE - 142
090034-OP_r0
9.12 DECAL LOCATIONS (1 OF 3)
Inside view of hood panel ends
Inside view of hood panel
WARNING
Sulphuric acid in
batteries can cause
severe injury or death.
Change only in
well-ventilated area.
Keep sources of
ignition awa y.
Rotating parts
can cause
severe injury.
Stay away while
engine and
compressor are
in operation.
WARNING
Accidental starts
can cause severe
injury or death.
Disconnect battery
and ground
spark plug lead
before servicing.
WARNING
Do not operate
without fan guard
in place.
WARNING
1
2
3
4
5
9
10
11
6
7
8
12