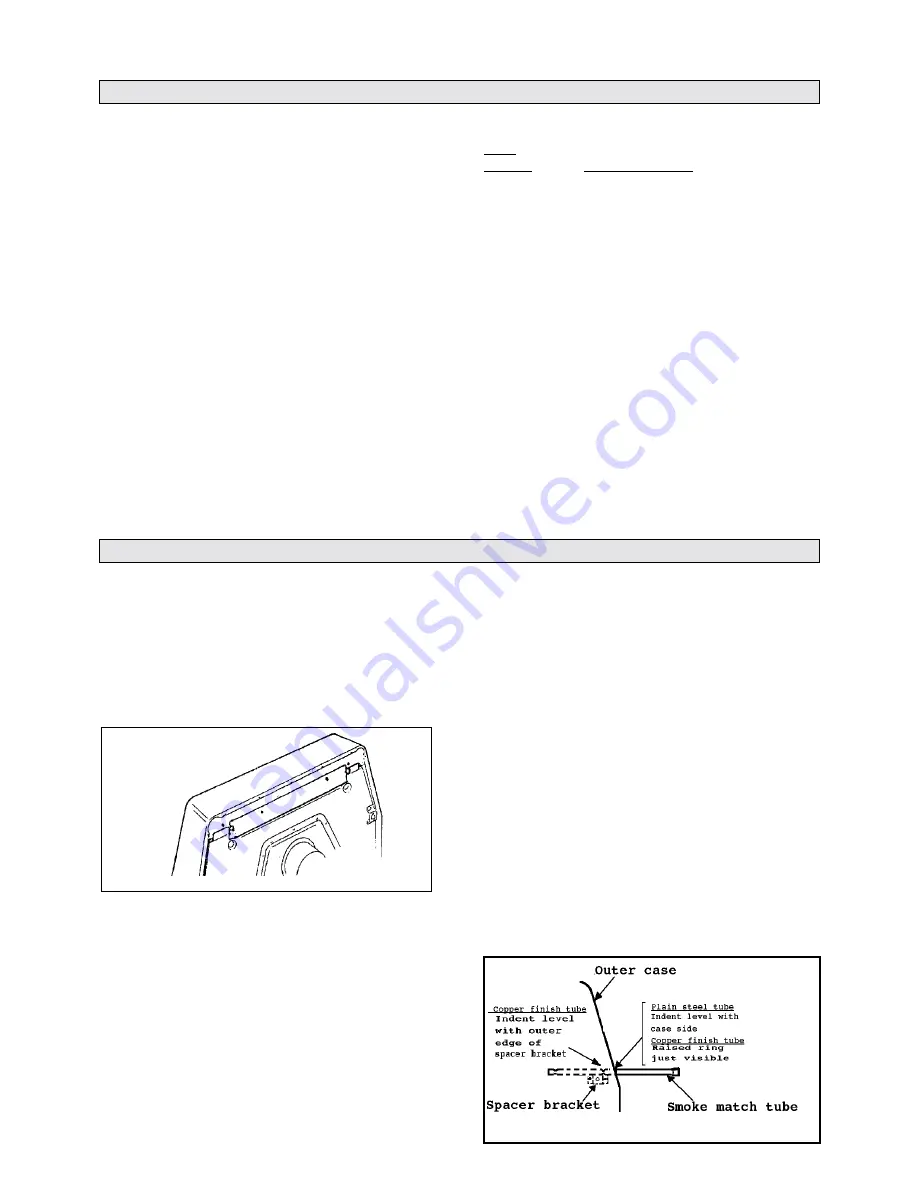
10
5.
FULL OPERATING CHECKS
5.1
Check Control Settings
5.1.1.
To help in checking the control positions while
the outer case is detached, place the control bezel over
the gas tap spindle and against the tap bracket.
Temporarily secure to the tap bracket with one of the
screws.
5.1.2.
Fit the control knob over the gas tap spindle.
5.1.3.
Depress the control knob and turn
anticlockwise partially towards the 1/IGN position until
some resistance is felt. Keep depressed at this position
to purge air from the system then, while keeping it
depressed, turn fully to the 1/IGN position. A spark
should be generated at the pilot while turning. The spark
should ignite the pilot.
5.1.4.
When pilot ignition has been achieved, keep the
control knob depressed for approximately ten seconds to
allow the thermocouple probe to warm up and then
release it. If the pilot does not remain alight, ensure that
the air has been purged, that the pilot orifice is clear and
that the thermocouple connections are sound. Replace
the pilot unit if necessary (see servicing section of this
manual).
5.1.5.
Check all the control settings. These are:-
Knob
Position
Burner appearance
1/IGN
Centre section on low. Outer
sections off.
2
Centre section fully on. Outer
sections off.
3
Centre section fully on. Outer
sections on low.
4
Centre and outer sections fully on.
5.2.
Check Reference Pressure
The appliance is pre-set to give the correct heat input at
the inlet pressure shown in section 1 of this manual. No
adjustment is necessary. Check the burner pressure by
fitting a pressure gauge at the test point. The test point is
on the pipe connecting the gas tap to the lower injector.
Check the pressure with the appliance alight and set at
maximum output (Control position 4).
After checking, turn off the appliance. Remove the
pressure gauge and replace the test point sealing screw.
Relight the appliance. Turn to the maximum output
position and test around the sealing screw for gas
soundness with a suitable leak detection fluid.
6.
FINAL ASSEMBLY & CHECKS
6.1
Fit The Outer Case
6.1.1.
Detach the control knob and control bezel.
6.1.2.
Refit the outer case. Make sure that the centre
strip at the top back of the case is located behind the
vertical face of the back panel.
The rearward angled ears near the top corners of the
back panel should be behind the outer case top plate,
(see fig.16).
6.1.3.
Secure the case at the bottom sides with the two
screws previously removed.
6.1.4.
Place the control bezel back in position and
secure it to the gas tap bracket with two screws.
6.1.5.
Fit the control knob over the gas tap spindle.
6.1.6.
Make sure that the coal is not dislodged when
refitting the case.
6.1.7.
Refit the window surround using the two
knurled screws previously removed (The reverse
method to that described in section 3.3.2).
Make sure that
the outer edges of the surround sides are inside the outer case.
6.2.
Test For Spillage
A spillage test must be made before the installed appliance
is left with the customer
.
6.2.1.
Close all doors and windows in the room
containing the fire.
6.2.2.
Light the appliance and set the control knob to
the maximum position (Position 4).
6.2.3.
Leave the appliance on for five minutes.
6.2.4.
There are two types of smoke match holders. One
has a copper finish, the other is plain steel. Please apply
the relevant parts of the spillage test instructions
Place the smoke match tube (with lighted match) on top
of the wall spacer bracket at the rear right side of the
appliance.
Copper finish tubes:
Slide the tube in until the second
indent is level with the outer edge of the spacer bracket.
A raised ring round the tube (approx. 25mm from the
indent) should be visible along the casing side (see
fig.17).
Plain steel tubes:
Slide the tube until the indent is level
with the edge of the casing side (see fig.17).
Fig.16 Outer case top location
Fig.17 Smoke match tube position