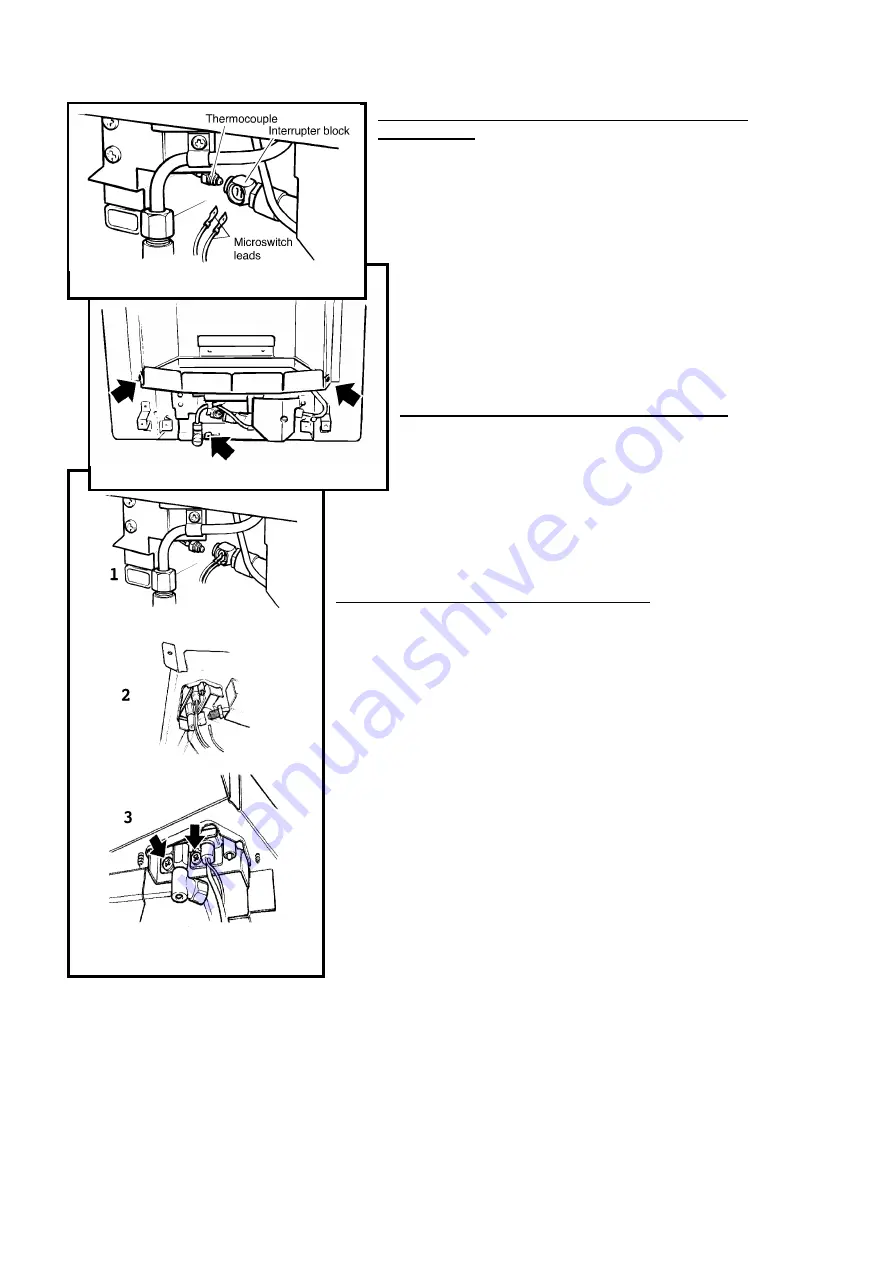
26
13.7
To remove the thermocouple interrupter block
(see figure 44)
13.7.1
Remove the bottom front cover
13.7.2
Detach the thermocouple from the interrupter block by
unscrewing the thermocouple nut.
13.7.3
Detach the two microswitch leads from the interrupter block.
13.7.4
Remove the interrupter block by unscrewing from the gas shut-
off tap.
13.7.5
Refit in the reverse order. If the microswitch leads cannot be
easily attached to the interrupter block when it is fully tightened to
the gas shut-off tap, slacken it and rotate to allow the leads to be
fitted. Retighten making sure that the leads remain in place in the
interrupter block. Fit and tighten the thermocouple nut making sure
that the leads are secured in the interrupter block to give a good
electrical contact.
13.8
To remove the burner unit (see figure 45)
13.8.1
Remove the front surround unit- See section 13.3.
13.8.2
Remove the 7 loose coals, the front coal halves, the base coal,
ceramic side walls and rear wall.
13.8.3
Support the inlet isolating elbow to avoid straining the
pipework and disconnect the appliance from the elbow.
13.8.4
Detach the burner unit from the convection box by removing 3 screws.
13.8.5
Replace in the reverse order. See section 13. 3. 6 for refitting the
surround.
13.9
To remove the pilot unit (see figure 46)
13.9.1
Remove the burner unit - See section 13.8.
13.9.2
To give clear access for disconnecting the pilot pipe, detach the ignition
generator & bracket unit from the burner as described in section 13.6. and lift it
clear.
13.9.3
Detach the thermocouple from the interrupter block by unscrewing the
thermocouple nut.
13.9.4
Detach the electrode lead from the underside of the electrode tab.
13.9.5
Disconnect the pilot pipe from the pilot unit elbow.
13.9.6
Remove the first screw
s
ecuring the dust cage to the
pilot unit / burner.
Carefully remove the dust cage and place aside.
13.9.7
Remove the second screw securing the
pilot unit to the burner.
Remove the pilot unit and place it aside.
13.9.8
Refit in the reverse order. See section 13. 3. 6 for refitting the surround.
Note 1 The pilot unit must be replaced as a whole assembly. Its individual components
are not separately replaceable.
2. Once removed, ensure that the dust cage is cleaned before refitting. Make sure
that it locates squarely onto the pilot unit without any gaps between the cage edges and the
pilot unit.
3. When the thermocouple is removed from the interrupter block, the microswitch
lead terminals in the interrupter block will be loose. Make sure that they are properly
secured to give a good electrical contact when retightening the thermocouple nut.
Fig. 46 Pilot unit removal (Dust cage
not shown for clarity)
Fig. 45 Burner removal points
Fig. 44 Thermocouple interrupter block