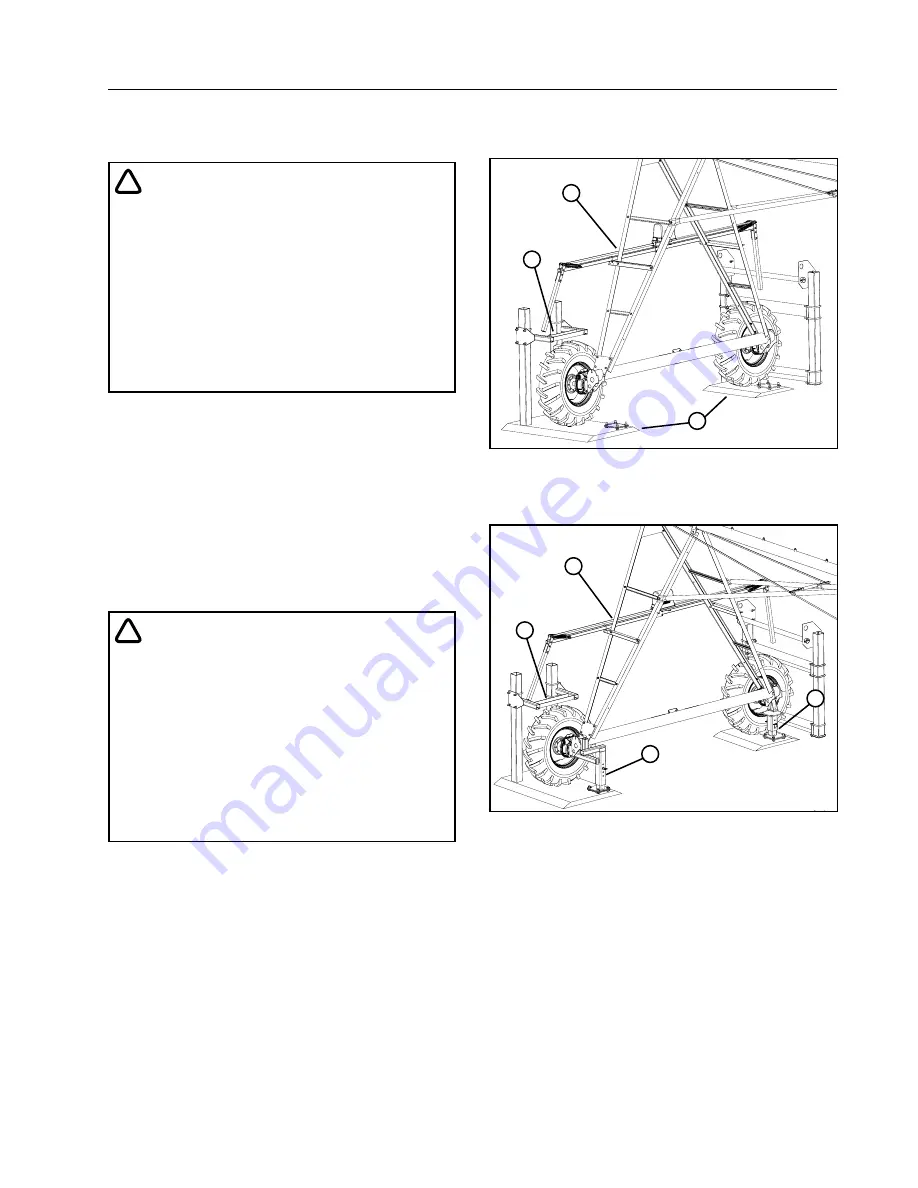
21
Overview
Bender160 Components
Bender Drive Unit Anchor
!
WARNING
• BENDER BARRICADE MUST BE INSTALLED
PRIOR TO ENTERING INTO BEND MODE.
FAILURE TO INSTALL THE BARRICADE PRI-
OR TO BENDING THE SYSTEM CAN RESULT
IN DAMAGE TO BOTH THE SYSTEM AND ANY
FIELD OBSTRUCTIONS IT MAY BE BENDING
AROUND.
• OPERATOR MUST BE PRESENT DURING
THE FIRST BEND WITH THE BENDER DRIVE
UNIT ANCHORS.
The Bender drive unit anchor is located at the
bending tower in conjunction with two concrete pads.
The bender drive unit anchor consists of a rear tire
hold down. See Figure 21-1.
When the bender end of field stop arm contacts the
bending barricade, the bending tower stops, and
the machine enters the bending mode. The bender
drive unit anchor holds down the rear tire during the
bending procedure to prevent the rear tire from lifting
off of the ground, allowing for stability and consistent
bending procedure.
!
CAUTION
• NEVER USE THE SAFETY OVERRIDE BUT-
TON TO WALK THE MACHINE OFF OF THE
BARRICADE. STRUCTURAL DAMAGE MAY
RESULT.
• SOIL MAY BUILD UP IN THE WHEEL TRACK
RESULTING IN A RAMP EFFECT ALLOW-
ING THE ACTUATOR ARM TO GO OVER THE
BARRICADES. REGULARLY MAINTAIN THE
WHEEL TRACK TO INSURE THE ACTUATOR
ARM ALWAYS CONTACTS THE BARRICADE.
Optional Hold Down Components
The optional hold down components are used in
situations where more hold down strength is required.
This may be necessary for long bender machines, or
on steep terrain, which could result in pulling forces
great enough to severely compress the trailing tire
against the hold down frame, or the leading tire
against the concrete. See Figure 21-2.
When being used properly the rear hold down hook
is to allow additional anchor strength to the rear tire
hold down. Additionally the front tire support is used
to transfer the load off the tire to the concrete pad.
2
1
3
Figure 21-1 Bender Drive Unit Anchor
1. Bender Drive Unit
2. Rear Tire Hold Down
3. Concrete Pad
1
2
3
4
Figure 21-2 Optional Hold Down Components
1. Bender Drive Unit
2. Rear Tire Hold Down
3. Rear Hold Down Hook
4. Front Tire Support
Summary of Contents for Bender160
Page 2: ...2...
Page 17: ...17 Safety Safety Decals Continued...
Page 18: ...18 Safety...
Page 22: ...22 Overview...