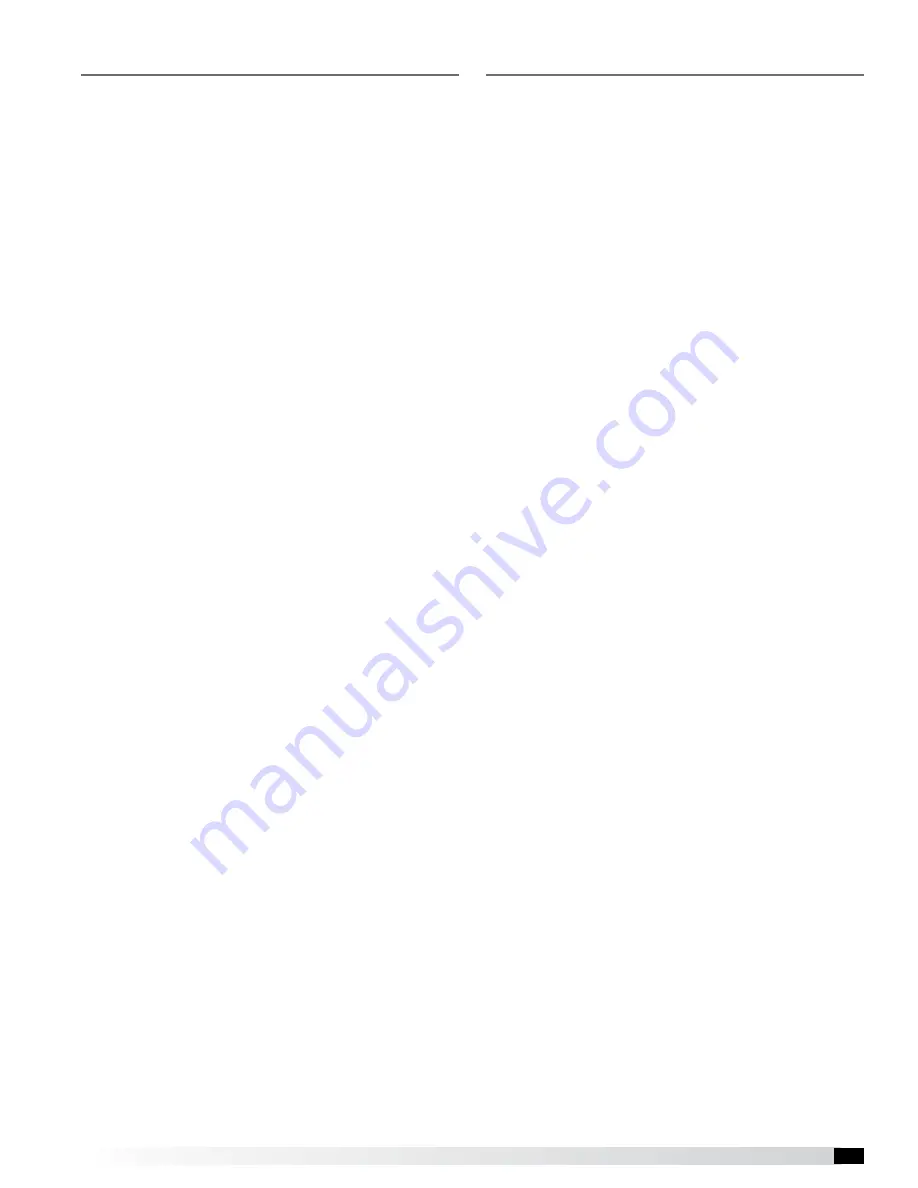
Dedicated Outdoor Air Unit
15
Phase Monitor
The unit control circuitry includes a phase monitor that
constantly checks for phase reversal, phase imbalance,
loss of phase or a power brownout. When it detects a
fault, it cuts off the 24 VAC that goes to the low voltage
terminal strip, thereby shutting off all motors.
Variable Frequency Drive (VFD)
If a VFD was provided and installed at the factory, it has
been pre-set to control the speed of the blower motor
for optimum performance. The motor speed needs to be
verified during test and balance of the unit.
If the system was configured for Constant Air Volume
(CAV), the VFD will operate in an ON/OFF fashion
and the speed of the motor will not change. If the
system was configured for Variable Air Volume (VAV),
the microprocessor will constantly monitor operating
conditions and provide a signal to the VFD, changing
the VFD output as needed.
The VFD may alternatively be connected to an external
signal such as provided by a BMS and be operated by a
2-10 VDC or a 4-20 mA input.
Supply Fan VFD Sequence
Optional Room CO2 Sensor:
The microprocessor will
modulate the supply fan based on a comparison of the
CO2 set point to the actual CO2 levels reported from
the sensor. Mechanical high static protection cutoffs
must be installed by others to protect the system and
equipment from over-pressurization.
Optional Duct Static Pressure Sensor:
The
microprocessor will modulate the supply fan based
on a comparison of the duct static pressure set point
to the actual duct static pressure level reported from
the sensor. Mechanical high static protection cutoffs
must be installed by others to protect the system and
equipment from over-pressurization. The manufacturer
does not assume responsibility for this.
Optional Building Static Pressure Sensor:
The
supply fan is modulated based upon the signal from a
building static pressure sensor. The microprocessor will
modulate the supply fan based on a comparison of the
building static pressure set point to the actual building
static pressure level reported from the sensor.
Optional Single Zone VAV:
The microprocessor will
use a space mounted temp sensor to vary heating and
cooling capacity and the airflow delivered by the fan to
maintain room-air temp at a desired set point.
Optional 0-10 VDC by others to VFD:
Supply fan is
modulated by a 0-10 VDC, field-provided by others.
Component Operation
Exhaust Fan VFD Sequence
Optional Building Static Pressure Sensor:
The
exhaust fan is modulated based upon the signal from
a building static pressure sensor. The microprocessor
will modulate the exhaust fan based upon a comparison
of the building static pressure level reported from the
sensor.
Optional Outdoor Air Damper Tracking:
The
microprocessor will proportionally modulate the exhaust
fan based upon the outdoor air damper position.
Optional Supply Tracking:
The microprocessor will
proportionally modulate the exhaust fan based upon the
supply fan.
Optional 0-10 VDC by Others to VFD:
The supply fan
is modulated by a 0-10 VDC provided by others in the
field.
Outdoor Air and Recirculated (Recirc) Air
Damper Sequence
Optional Room CO2 Sensor:
The microprocessor
will proportionally modulate the OA/RA dampers based
upon a comparison of the CO2 set point to the actual
CO2 level reported from the sensor. As the CO2 level
rises, the controller will proportionally modulate the
outdoor air damper open, between the minimum and
maximum OA position.
Optional Building Pressure:
The OA/RA dampers
will modulate based upon the signal from a building
static pressure sensor. The controller will modulate
the dampers, between the minimum and maximum OA
positions, based upon a comparison of the building
static pressure set point to the actual building static
pressure level reported from the sensor.
Exhaust Fan Only Power
The exhaust fan will have a dedicated power circuit
where in the case of a power outage, the exhaust fan
will still run. A phase monitor will detect an outage or
power loss and open the contact, disconnecting all
power to the unit and controller. An external signal will
need to be sent to a relay to power the exhaust fan,
enabling the fan to run at a maximum speed. This
sequence is NOT to be used for high temperature
exhaust applications.
Vapor Tight Lights
Vapor tight lights provide light to each of the
compartments in the energy recovery unit. The lights
are wired to a junction box mounted on the outside of
the unit. The switch to turn the lights on is located in
the unit control center. The switch requires a separate
power source to allow for power to the lights when the
unit main disconnect is off for servicing.
Optional Component Operation
Summary of Contents for VX Series
Page 51: ......
Page 52: ......
Page 53: ......
Page 54: ......
Page 55: ......
Page 56: ......
Page 57: ......
Page 58: ......
Page 59: ......
Page 60: ......
Page 61: ......
Page 62: ......
Page 63: ......
Page 64: ......
Page 65: ......
Page 66: ......
Page 67: ......
Page 68: ......
Page 69: ......
Page 70: ......
Page 71: ......
Page 72: ......