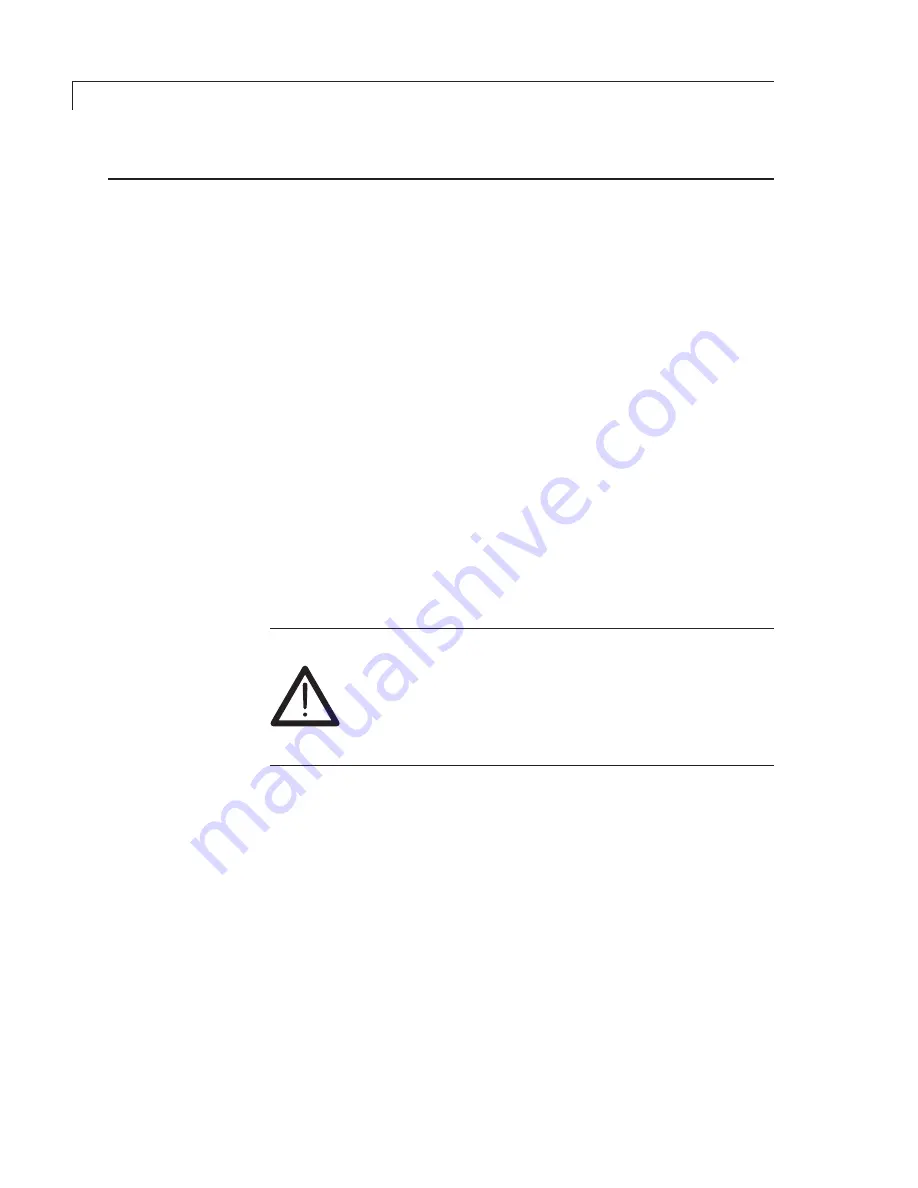
14
Initial Power-Up
Connections
1. Plug the supplied power cord into the rear mounted power supply. Ensure
that the power supply output cable is plugged into the interface board power
connector.
2. Connect the carrier gas source (25 psi maximum pressure) to the carrier inlet
on the rear panel.
If this is a dual inlet system:
Connect appropriate source gases to the carrier inlet and dilution gas inlet.
The source must be of sufficient capacity to flow the maximum LPM of the
sum of dilution and carrier combined on a single inlet system. The carrier inlet
source must be able to provide at least 500 SCCM, and the dilution inlet must
be able to source the maximum dilution flow, which may be as high as 20
SLPM.
3. Turn on the calibrator with the main power switch on the front panel.
This supplies the fans, the control valves, and the pump, if so equipped.
4. Turn on the heater switch on the front panel. The display on the permeation
chamber cover will display a boot sequence, followed by a display of the
actual temperature.
5. Connect the span outlet to your instrument.
Always leak check the entire instrument and all flow connec-
tions, particularly if toxic, corrosive, or flammable gas mixes
will be generated.
Use clean/dry air or N
2
to perform a pressure/decay test to
verify the leak integrity of the system before putting it into
service.
Chamber Temperature
• If the chamber temperature exceeds the value set by the mechanical
temperature limit switch, the heater will automatically shut down and
a warning screen will appear on the touch screen controller.
• When the front panel door is removed, the heater automatically shuts down.
• Always refer to the separate instructions accompanying the permeation
tube(s) to make sure that the selected temperature is compatible with the
permeation tube(s) being used.
The front panel displays the current chamber temperature and the control status
of the instrument, indicated by the PNL and TMP lights. (Refer to Figure 4 on page 11.)
The chamber temperature can be set manually through the controls on the front
panel or remotely through RS-232 communication. (Refer to the chapter entitled
“Serial Port Communications” on page 17). After a temperature set point is entered
by either method, it is written to memory so that after a power failure the unit
will return to the condition previously established.
Summary of Contents for 500
Page 9: ... Introduction Specifications ...
Page 36: ...32 Model Number Breakdown ...