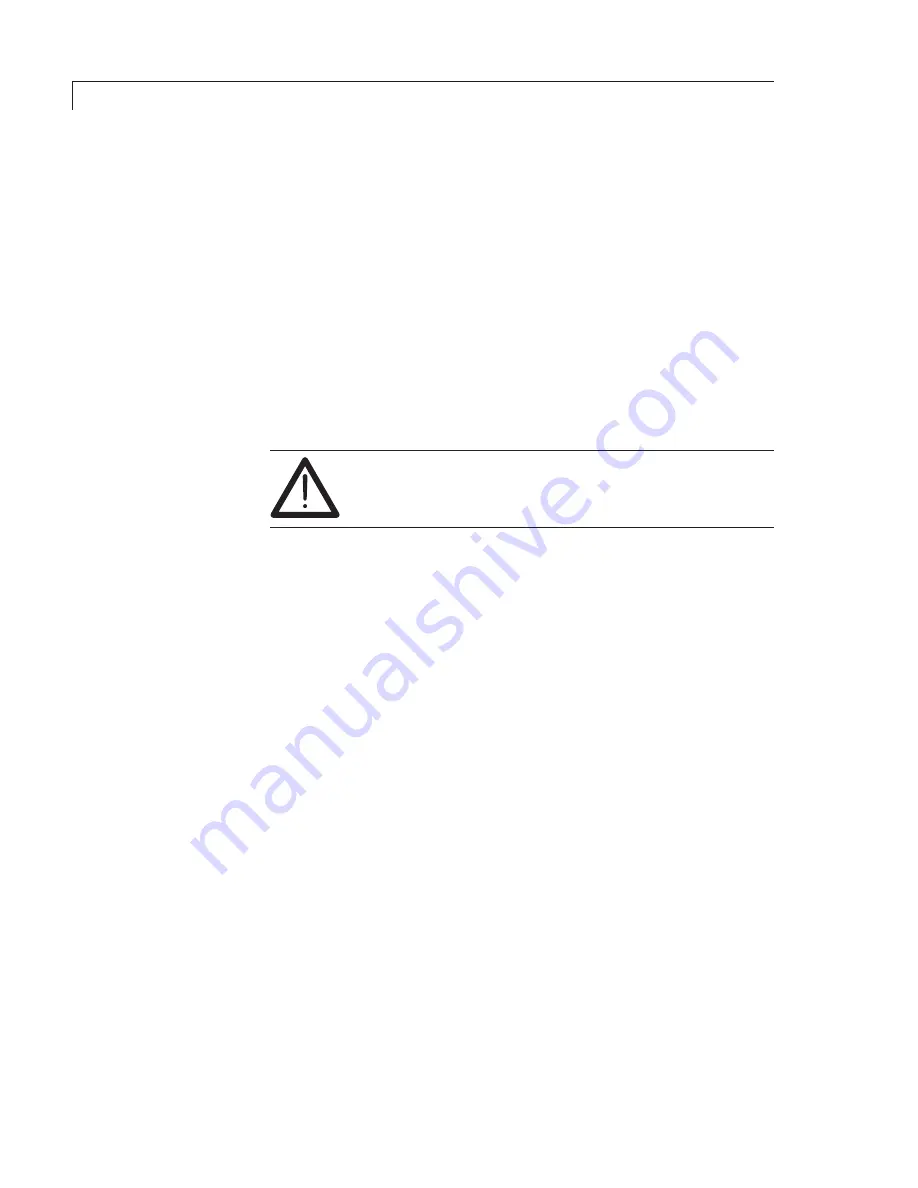
Unit Location
In general, the Dynacalibrator should be as close as possible to the analyzer to be
calibrated, as long as:
• the ambient temperature is at least 2°C below the selected operating
temperature of the permeation chamber.
• ambient temperature variations are minimal.
• exposure to precipitation and condensation is minimized.
• air flow around the unit’s cooling vents and rear panel fan intake is not
blocked or restricted, particularly for the rack-mounted units.
• it is on a level surface, to prevent errors in flow determination caused by a
non-vertical flowmeter
When the Dynacalibrator is installed in an instrument rack,
the user must make certain that the overall rack ventilation/
cooling is adequate.
A bench-mounted Dynacalibrator should be placed on a firm horizontal
surface – preferably the same surface as the analyzer to be calibrated. A rack-
mounted enclosure in a mobile installation (van, aircraft, etc.) requires additional
mechanical support between the rack and the rear of the enclosure. This addi-
tional support is not needed for slide-mounted enclosures.
Once the Dynacalibrator has been unpacked and a location selected, check
the packing slip included with the shipment to verify that all the ancillary parts
(forceps, etc.) are available. In the event of a discrepancy, please notify VICI
immediately.
Permeation Device Conditioning
Dynacal permeation devices must be conditioned prior to their use in the
Dynacalibrator. Proper conditioning ensures that the device performs at its
specified mass permeation rate and accuracy.
Conditioning is accomplished primarily by heating the device for a specified
time period in a temperature-controlled environment (at the intended operating
temperature ±1°C) through which there is a steady purge of dry gas at a
minimum of 80 cc/min.
Since conditioning for each specific device is a function of a variety of factors,
inflexible rules or recommendations cannot be included here. Contact VICI
Metronics for conditioning information for your permeation devices.
Getting Started
Summary of Contents for 500
Page 9: ... Introduction Specifications ...
Page 36: ...32 Model Number Breakdown ...