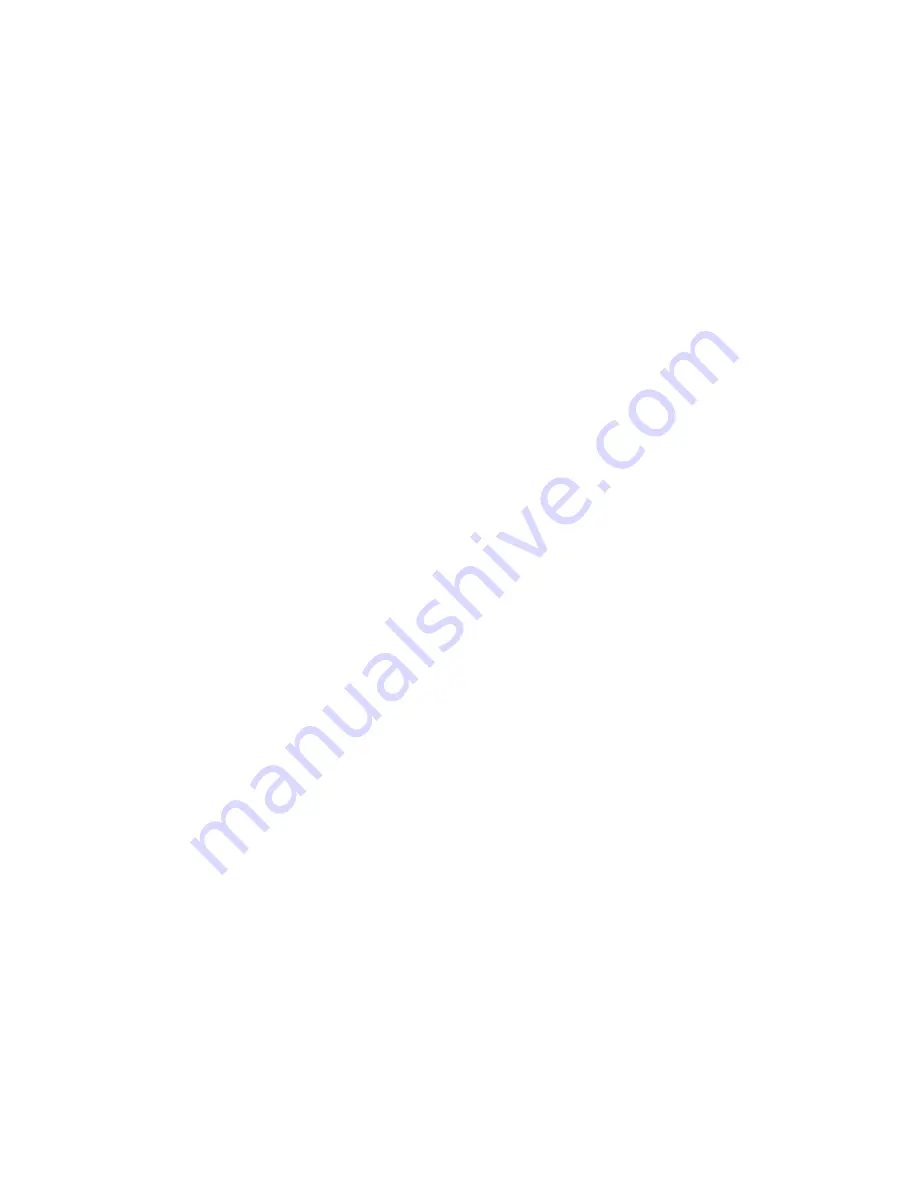
AIR FILTER REPLACEMENT
If the air motor does not perform as normal, check for a clogged air filter.
1. Shut off air pressure to the pump and release pressure in the line to the pump.
WARNING
NEVER remove swivel air connector while air line is pressurized.
2. Note the position of the retaining clip. It can only be secured by the smallest tang of
the metal retainer. Grasp air line with one hand and pull the retaining clip with pliers.
3. Pull the swivel air connector out.
4. Carefully remove air filter.
5. Clean air filter with an air hose or replace with a new air filter.
6. Re-insert the air filter.
7. Put a thin film of grease on the o-ring of the swivel air connector.
8. Reassemble the swivel air connector and retaining clip. Be sure that clip is secured
on the smallest tang of the metal retainer.
9. Check to make sure the swivel air connector is securely attached before turning the
air pressure back on.
MAINTENANCE
1. Periodically check all hydraulic and air connections to be sure they are tight. Loose
or leaking connections may cause erratic and/or total loss of operation. Replace or
repair all defective parts promptly.
2. Periodically check the hydraulic oil level in your system. See filling instructions on
page 2.
3. Change hydraulic oil after every 100 hours of operation. In dusty or dirty areas, it
may be necessary to change the oil more frequently. To change the oil, drain used oil
through the fill opening and fill reservoir to
1
/
2
" [1 cm] below the fill opening with
clean Enerpac hydraulic oil. Dispose of used oil in accordance with local regulations.
WARNING
The pump is equipped with an overload valve, preset for maximum operating
pressure. DO NOT attempt to adjust the overload valve. If adjustment is required,
contact an Enerpac Service Center. Adjustment by other than qualified personnel
may cause malfunction, damage to the system, and/or personal injury.
Storage
When the unit will be stored for 30 days or more:
1. Wipe the entire unit clean.
2. Disconnect all air pressure and hydraulic lines to prevent accidental operation.
3. Cover the unit.
4. Store in a clean, dry environment. DO NOT expose equipment to extreme
temperatures.
5
Summary of Contents for QS-2000A
Page 1: ......