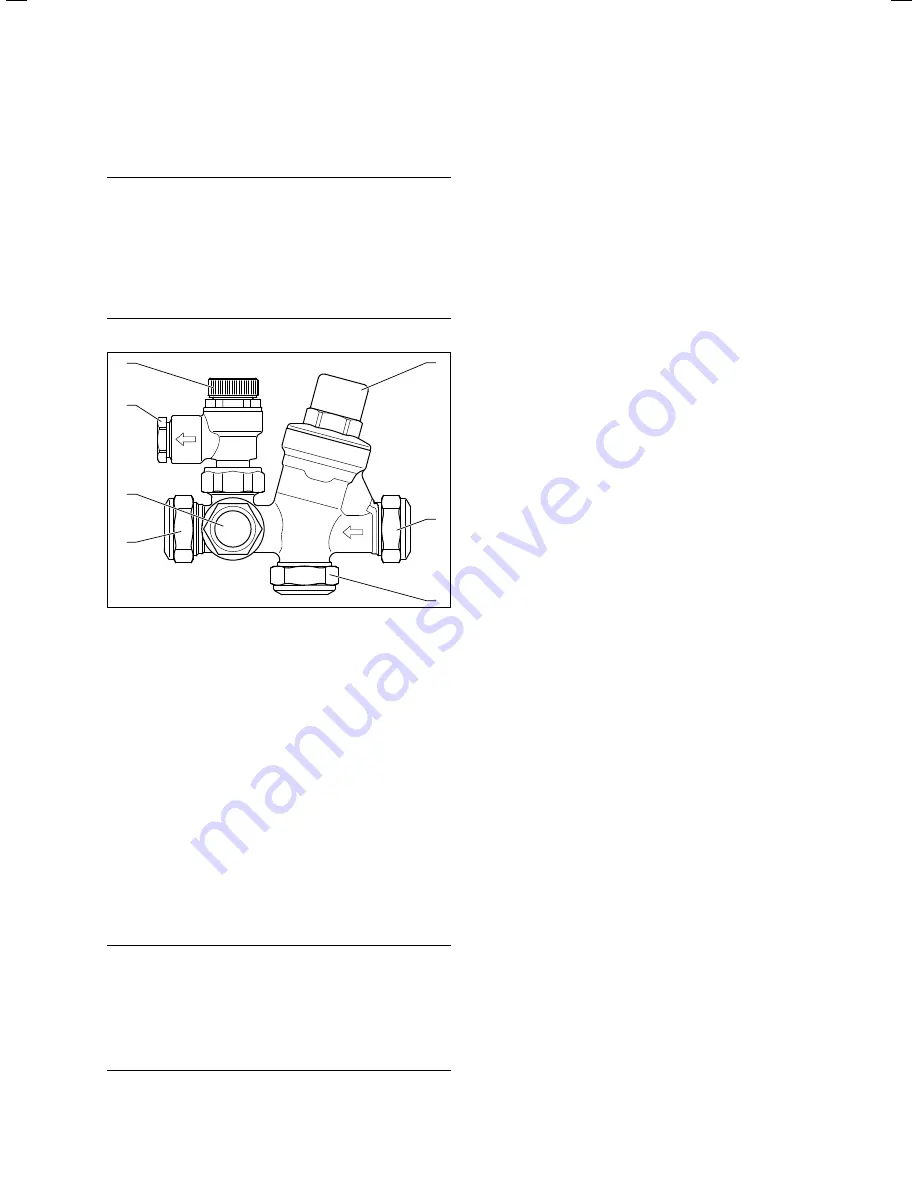
Installation and maintenance instructions for uniSTOR 0020111105_00
17
5.3.2 Mounting the safety assembly
b
Caution!
Risk of damage to the cylinder as a
result of excess pressure!
Excess pressure can cause the cylinder to
burst.
>
Make sure that there is no stop valve ins-
talled between the safety assembly
and the cylinder.
1
2
3
4
5
7
6
Fig. 5.4 Safety assembly
Key
1 Pressure reducing valve with line strainer
2 Cold water inlet
3 Pressure-controlled cold water inlet
4 Cylinder
connection
5 Hot water expansion vessel connection
6 15 mm expansion relief valve connection
7 Expansion relief valve
>
During the installation process, position the valves so
that you are able to connect the 15 mm connection (
6
) of
the expansion relief valve (
7
) with the tundish. Note the
direction of flow, which is marked on the safety assembly
with arrows.
i
The safety assembly must be installed horizon-
tally with the expansion relief valve facing
upwards (
¬ fig. 5.4
) in order to prevent the
build-up of dirt.
b
Caution!
Risk of damage to the cylinder as a
result of excess pressure!
Excess pressure can cause the cylinder to
burst.
>
Make sure that the expansion relief valve
outlet is not covered or closed.
>
Mount the discharge pipe of the expansion relief valve
with a constant slope to the outside. The discharge pipe
must finish at a safe and visible point where there is no
danger of it freezing up and where it poses no risk of
injury to persons.
>
Actuate the expansion relief valve regularly to prevent
calcification.
>
Connect the cylinder to the cylinder connection (
4
).
>
For the pipe from the main stop valve of the building to
the cylinder, use copper piping with a diameter of at
least 22 mm to ensure that the cylinder is as efficient as
possible. This is particularly important for installations
with a balanced cold water inlet (
3
).
>
Mount the safety assembly in the cold mains inlet on the
cylinder.
>
If necessary, establish the connection to the cold water
inlet (
3
) with pressure compensation of the safety
assembly.
>
Depending on the fittings used and the type of the draw-
off points, it may be necessary to install a backflow pre-
venter in the pressure-controlled cold water inlet.
i
If you mount the safety assembly above the cyl-
inder, you do not need to drain the cylinder in
order to maintain the safety assembly. Make
sure there is sufficient space for maintenance
and connection of the discharge pipe of the
expansion relief valve.
When the discharge pipes are connected, the expansion
relief valve may not be more than 600 mm away from
the temperature and pressure relief valve (
¬ fig. 5.5
).
5.3.3 Mounting the expansion vessel
The Vaillant domestic hot water cylinder is delivered
with an external expansion vessel.
Connect this expansion vessel to the installed safety
assembly as follows:
>
Screw the expansion vessel directly to the safety assem-
bly via the provided connection (
5
) or
>
Connect the expansion vessel with the safety assembly
via a copper pipe or suitable hose line. Make sure the
expansion vessel is supported sufficiently.
>
Use the supplied wall bracket if you want to mount the
expansion vessel to a wall.
i
In regions with high water pressure (4 bar or
more), you can also connect the mixer tap for a
bath or shower to the cold water inlet with pres-
sure compensation (3) of the safety assembly.
This ensures that the hot and cold water supply
to the mixer tap have the same pressure. You
should install the cold water supply for all other
connections using a T-piece before the safety
assembly in the cold mains inlet to the cylinder.
Installation 5