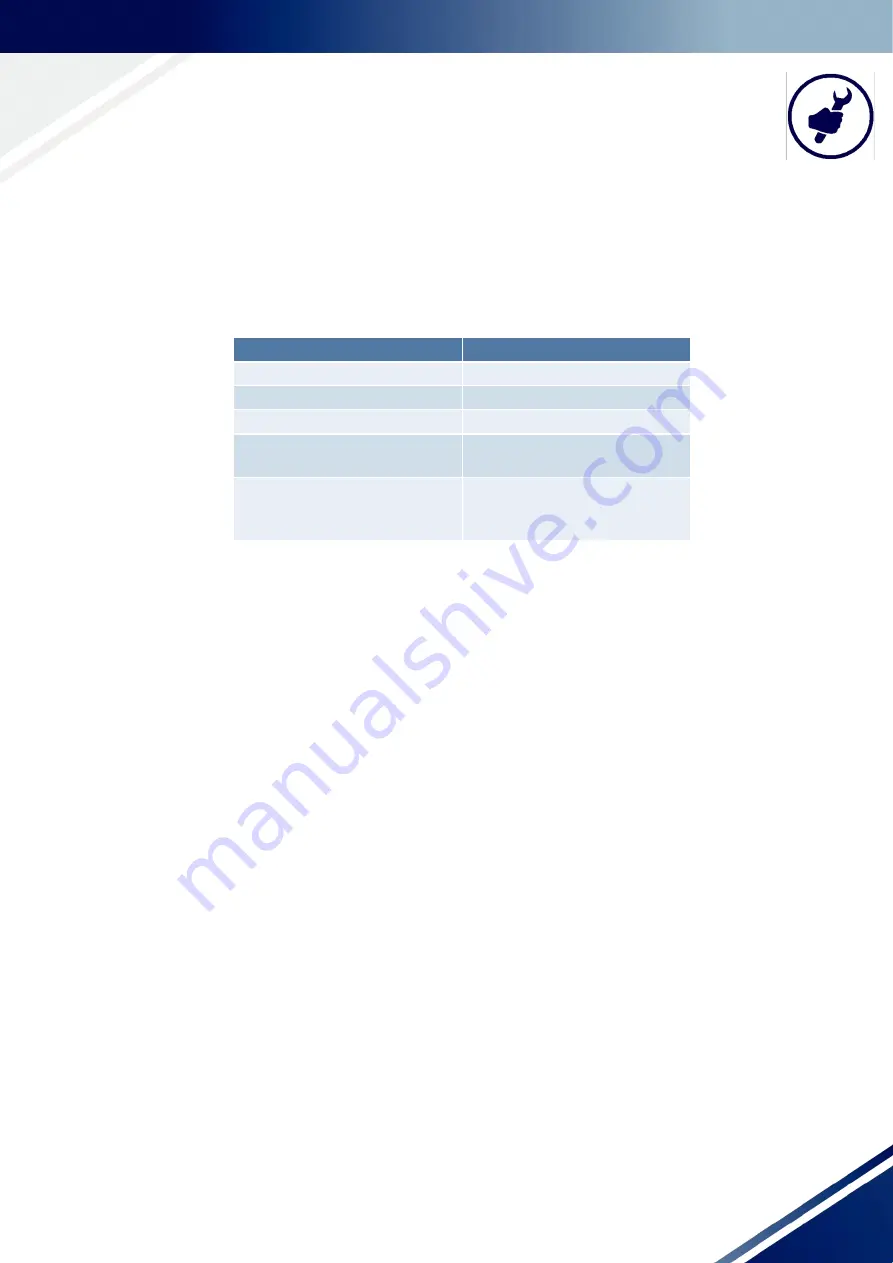
MAINTENANCE
35
7.4
Carbon brush
Carbon brush
The carbon brush must not fall below the defined wear limit. The current collector must be replaced once the
wear limit has been reached. The dimension can be found in the customer-specific drawing.
Carbon brush springs
The contact pressure of the carbon brush springs must not fall below the values in the following table. Measure
the force required to push in the carbon brushes. If the contact pressure is no longer sufficient, the entire cur-
rent collector unit must be replaced.
Carbon brush
Minimum force, approx. [N]
BLS200
32
BLS200Q
35
BLS100
20 (10 each per carbon brush)
ONST50
(SA-BLS50)
5
ONST10/20 (0166546/01)
ONST10/20 (0590603/00)
(SA-BLS20)
3
8