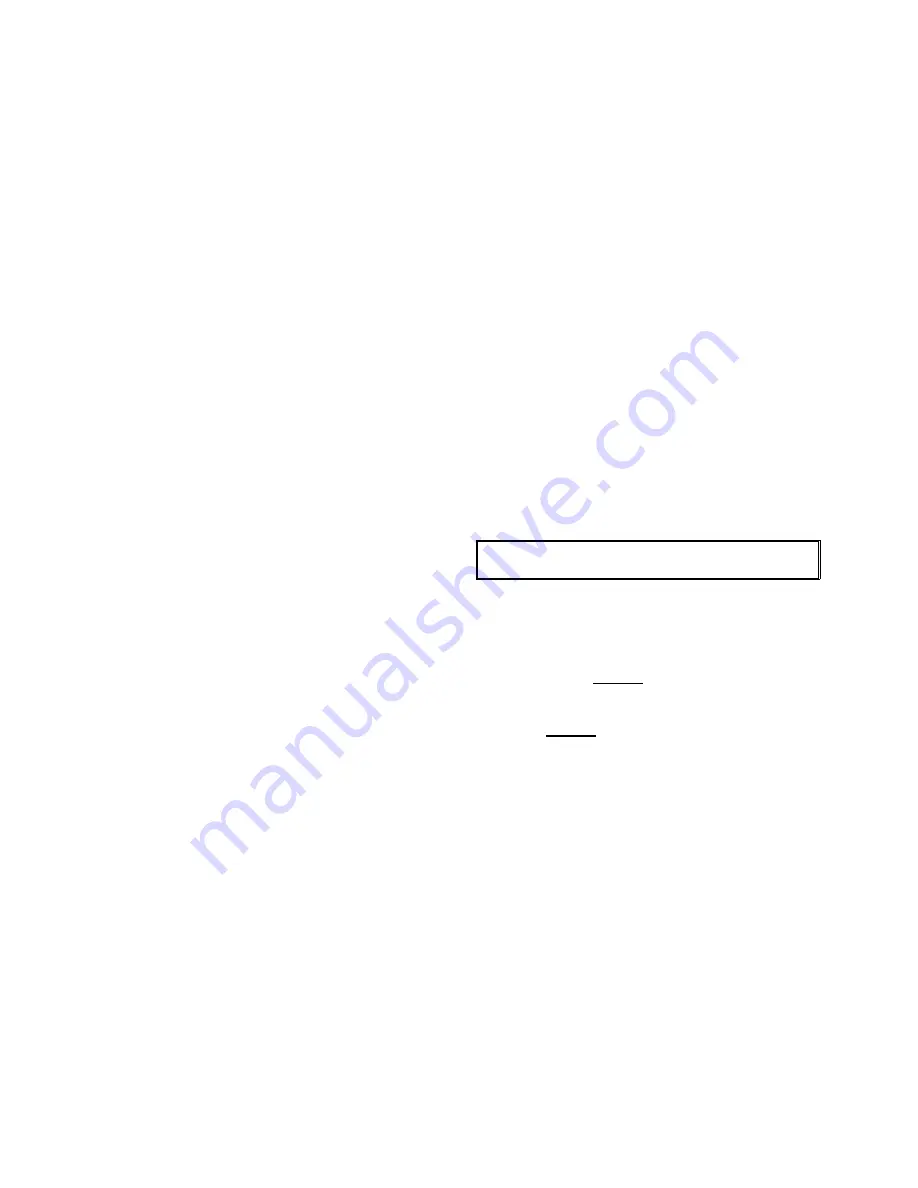
4
Disassemble the valve only as far as needed to
replace damaged or worn parts.
First ensure there is no pressure within the
valve. Refer to Page 5 for parts location and
identification.
Remove the cover bolts (13) and lift off cover (2)
with float and linkage attached. It may be
necessary to pry the cover off. Be careful not to
damage or lose the cover O-ring (14) unless
being replaced.
Remove the spring pin (21) connecting the lever
arm to the cage (3). Remove the seat (4) from
the cage and remove the plug (5). Remove the
cage O-ring (16) and renewable seat (15) from
the seat.
The float ball (12) is secured to the float rod (10)
by Loctite 263 and the hex nut (20). Loosen the
hex nut (20) and apply heat (approx. 550F) to
the connection while unscrewing the float ball by
hand. (If replacing the float ball, it may be more
practical to replace both the float ball and the
float rod.) Be careful not to lose the lock washer
(24).
The float hood (11) is attached to the float ball
(12) by a nylon cap screw (25) and lock washer
(24). The cap screw is secured by Loctite 380.
Inspect all parts for wear and damage. Minor
scratches and dents in the float are normal.
Replace the float if water is detected inside of it.
Replace damaged parts.
REASSEMBLY
Clean all parts especially seating and sealing
surfaces before reassembling valve. Worn parts
should be replaced during re-assembly.
Install plug (5) in seat (4), lubricate and install
cage O-ring (16) and renewable seat (15) in seat
(4). Thread cage (3) with plug and seat into
cover (2) and tighten.
Thread orifice button (8) all the way into lever
arm (7) and install hex nut (22) and lock washer
(23) but do not tighten. Connect the lever arm
(7) to the cage (3) using spring pin (21).
Adjust the orifice button (8) so that the lever arm
(7) is parallel to the cover (2) when it is gently
resting on the plug (5) in the closed position.
Secure by tightening hex nut (8).
Install hex nut (20) and lock washer (24) onto
end of float rod (10). Apply Loctite 263 to the
threads on the float rod (10) and screw float ball
(12) onto float rod (10). Tighten hex nut (20).
Install lock washer (24) onto cap screw (25).
Apply Loctite 380 to cap screw (25) insert
through center hole in float hood, screw onto
float ball (12) and tighten.
Verify free movement of linkage mechanism and
that the orifice button (8) presses against the
plug (5) when it is closed and pulls away from
the plug when it in the fully open position.
Lubricate and place O-ring (14) in cover (2) and
carefully place cover (2) on body (1) ensuring O-
ring is retained. Install the cover bolts (13) and
tighten in an alternating pattern.
Carefully introduce pressure and check for
leaks.
BACKFLUSHING INSTRUCTIONS
Follow all local cross-connection and safety
codes and regulations!
To determine if a GA Industries sewage air valve
needs cleaning or backflushing:
•
Close the inlet isolating valve then slowly
open the ½” flushing ball valve (if installed)
or slowly remove the pipe plug at the top
of air valve to relieve internal pressure.
•
Open t
he 1” blow off ball valve (if installed)
or remove the pipe plug near the bottom.
Liquid should freely drain from the valve
body. If it does not, then the valve is likely
in need of cleaning or backflushing.
To clean a GA Industries sewage air release
valve equipped with backflushing attachments:
•
Close the inlet isolating valve and then
slowly open the ½” flushing valve to
relieve internal pressure.
•
Open the
1” blow off valve
•
Conne
ct the ½” flushing valve to a
pressurized source of clean water using
the rubber hose provided with the
backflushing attachments.
•
Introduce flushing water until liquid runs
freely from the blow off valve.
•
Shut off and disconnect the supply of
clean water and close the blow off and
flushing valves.