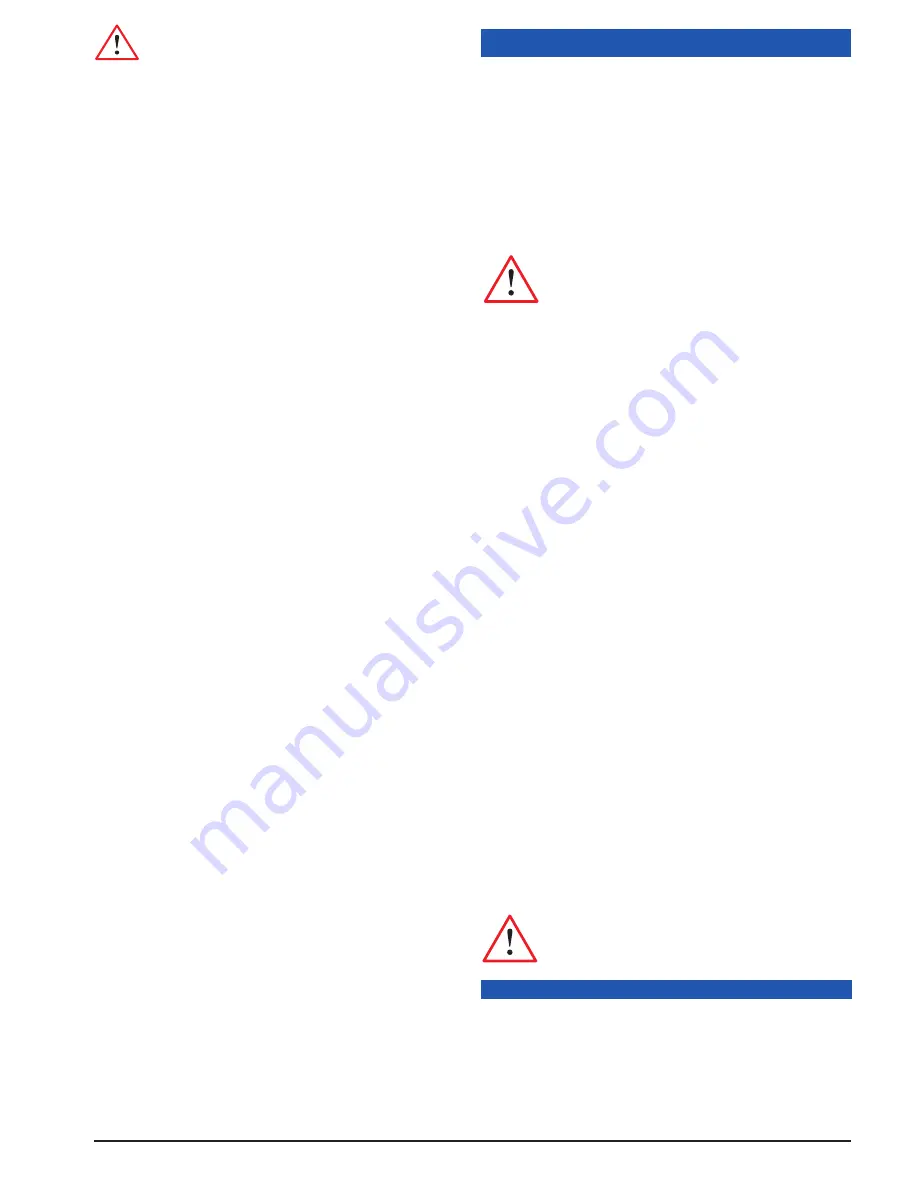
VAG Operation and Maintenance Instructions • 11
4.4 Assembly instructions and fittings
Check the valve for possible damage that it may have suffered du-
ring transport and storage. Protect the valve against dirt caused
on the construction site by adequate covering until installation.
Prior to installation all components essential for proper function,
such as the seat and the sealing ring of the disk must be tho-
roughly cleaned to remove all dirt particles. VAG does not assume
any liability for consequential damage caused by dirt, shot-blas-
ting gravel residues etc.
The sealing and operational parts should be checked for proper
operation prior to installation.
Should the valve be repainted later on, you should ensure that no
paint is applied to the sealing and operational parts . The identifi-
cation plates must not be painted over either. If the equipment is
sand-blasted for cleaning prior to installation, these parts must be
adequately covered. If solvents are used for cleaning, You should
ensure that the solvents do not destroy the seals of the pipeline
or the valve.
For the assembly of the VAG EKN
®
Butterfly Valve it must be en-
sured that proper load suspension devices as well as means of
transport and lifting devices are available.
In open position, the disk of the VAG EKN
®
Butterfly Valve pro-
trudes beyond the overall length. It needs to be made sure that
there is sufficient space between the disk and other installations
in the pipeline.
Suspending the valve by its disk may lead to damage to or de-
struction of the disk or valve.
When installing valves with a defined flow direction (e.g. flow di-
rection is indicated by arrows on the body) please observe the
flow direction during installation.
When connecting the valve with the pipeline flanges, hexagon
bolts and nuts with washers from flange to flange must be used
in the through holes. Fasten the bolts evenly and crosswise to
prevent unnecessary tension and the resulting cracks or breaks.
The pipeline must not be pulled towards the valve. Should the gap
between valve and flange be too wide, this should be compen-
sated by thicker seals.
The material of the seal needs to be selected according to the
operation conditions.
We recommend using steel-reinforced rubber seals to DIN EN
1514-1 Shape IBC. If you use raised face flanges, these seals are
mandatory.
For bolted flanges, the European standard EN 1591 applies. The
operator needs to select bolts and nuts suitable for the respective
operation pressure, temperature, the flange material, the operati-
onal loads and the seal. As depending on the seal materials used
and whether they are used in main friction connections or secon-
dary friction connections, very different tightening torques of the
flange bolts result, the operator must choose the tightening torque
of the flange bolts according to the above parameters.
Do not over-tighten the bolts of the flanges as this may result in
damage to the valve or the flanges faces cracking.
While the valve is being installed, it must be ensured that the
flanges of the pipeline it is connected to are aligned and level with
each other. Welding works on the pipeline must be performed be-
fore the valves are installed to prevent damage to the seals and
the corrosion protection. Welding residue must be removed befo-
re the equipment is put into operation.
The pipeline must be laid in a way that prevents harmful pipeline
forces from being transmitted to the valve body. Should construc-
tion works near or above the valve not be completed yet, the valve
must be covered to protect it from dirt.
5 Set-up and operation of the valve
5.1 Visual inspection and preparation
Before putting the valve and the equipment into operation, per-
form a visual inspection of all functional parts. Check whether all
bolted connections have been properly fastened.
5.2 Function check and pressure test
Prior to installation, the function parts of the valve have to be ope-
ned and closed completely at least once and should be checked
for trouble-free operation.
Warning:
The pressure exerted on the closed valve
must not exceed its nominal pressure (see technical
data sheet KAT 1310-A). When a pressure test is per-
formed in the pipeline with a test pressure exceeding
the admissible nominal pressure in closing direction,
the pressure must be compensated by way of a by-
pass.
If the VAG EKN
®
Butterfly Valve is operated in dry state, higher
actuation torques may be expected.
Newly installed pipeline systems should first be thoroughly purged
to remove all foreign particles. Residue or dirt par-ticles present
in the pipeline may impair the function of the valve .or prevent its
free movement.
In particular after repair work or upon the commissioning of new
equipment, the pipeline system should be purged again with the
valve being fully open position. If detergents or disinfectants are
used it must be ensured they do not attack the valve materials. As
a standard, the valve is closed by turning clockwise at the gear.
The dimensions of the stems and actuators allow operation of the
valve by one person via the handwheel. Extensions for operation
are not permissible as they may damage the valve due to exces-
sive force. The 90° turn is limited by a limit stop located at the
gear. If it is turned further using excessive force, this may cause
damage. Proper function is to be checked by opening and closing
the valve several times.
5.3 Putting electric actuators into operation
Turn the valve into medium intermediate position by hand. Check
the rotary motion at the gear and thus the direction of rotation of
the motor by shortly starting the actuator electrically. If the direc-
tion of rotation is wrong, reverse the polarity of the motor con-
nection.
By short electrical start-up, check the direction of rotation again
by checking the direction of motion.
Check the switch-off function of the torque and limit switches in
both directions by manually operating the switches in intermedia-
te position. Reverse the polarity, if necessary. The valve must not
be operated over its entire travel until the direction of rotation and
the switch-off function are correct.
If the direction of rotation is wrong, the limit and torque
switches have no effect at all!
6 Actuators
6.1 General
Actuators (gears, pneumatic, hydraulic and electric actuators) are
designed for flow velocities according to Table 2 in EN 1074-1
(valves used for water supply; requirements relating to fitness for
use). Any deviating operating conditions need to be specified.
The adjustment of the limit stops (OPEN, CLOSE) must not be