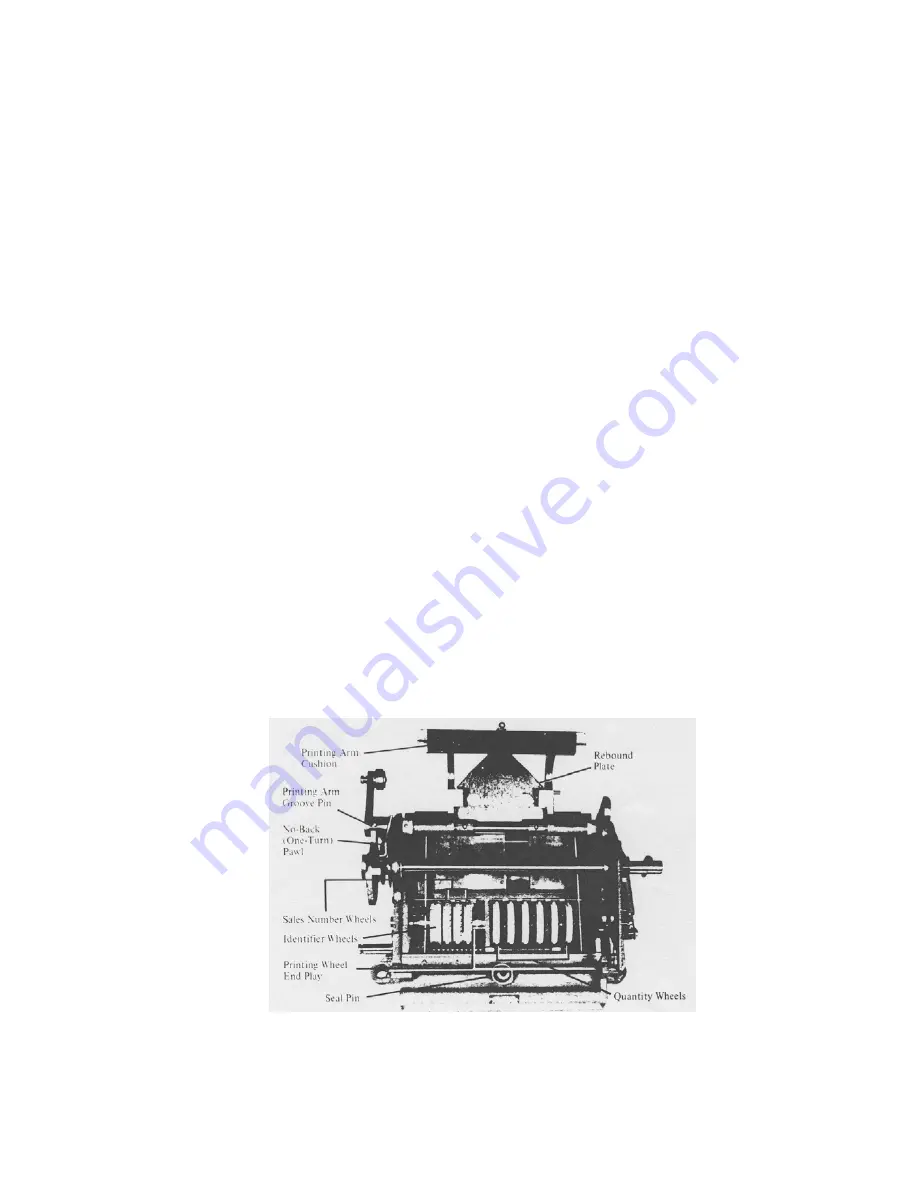
9
5. TROUBLE SHOOTING
5.1 GENERAL CHECKS (FIGURES 6 THRU 10).
If the reason for the trouble is unknown, it is necessary to examine the printer to be sure it functions
properly.
Observe function of the no back pawl by turning the crank in a counter clockwise direction. The no
back pawl should limit the rotation to 20 degrees.
Turn the crank in a clockwise direction. The one-turn stop pawl should stop the crank after one
complete turn.
Turn crank until tray is in rear position and seal pin is up.
While turning the crank, observe the following during the print-in cycle:
a. tray moves forward to print-in position, seal pin pierces ticket and wheels reset to zero.
b. print action occurs before stop.
c. simulate delivery by turning drive gear While delivery is being made sales number wheel
advances one digit.
Observe the following during the print-out cycle.
a. tray moves to rear printer.
b. print-out occurs showing the quantity delivered.
c. seal pin releases ticket before stop is reached.
Check print wheel end play for 0,5 mm to 0,65 mm.
Turn the printer so the printing arm faces you. Check the springs to see that they are properly
anchored.
Check roller on the printing arm for proper alignment on cam.
Examine stop pawl for proper assembly.
Turn the printer so the back faces you. Be sure the ticket stop screw is secure.
Check the tray support rods to be certain they are free and secured in place by four clips.
Turn the printer so the crank faces you. Be sure the springs are properly anchored.
Examine the E-ring retaining and pins to be certain that they are properly seated and thight.
Examine the three reset gears for damage or wear. Replace as required.
Fig. 6: Parts Identification
Summary of Contents for 247
Page 9: ...8 Fig 4 Lubrication points Fig 5 Lubrication points...
Page 18: ...17...