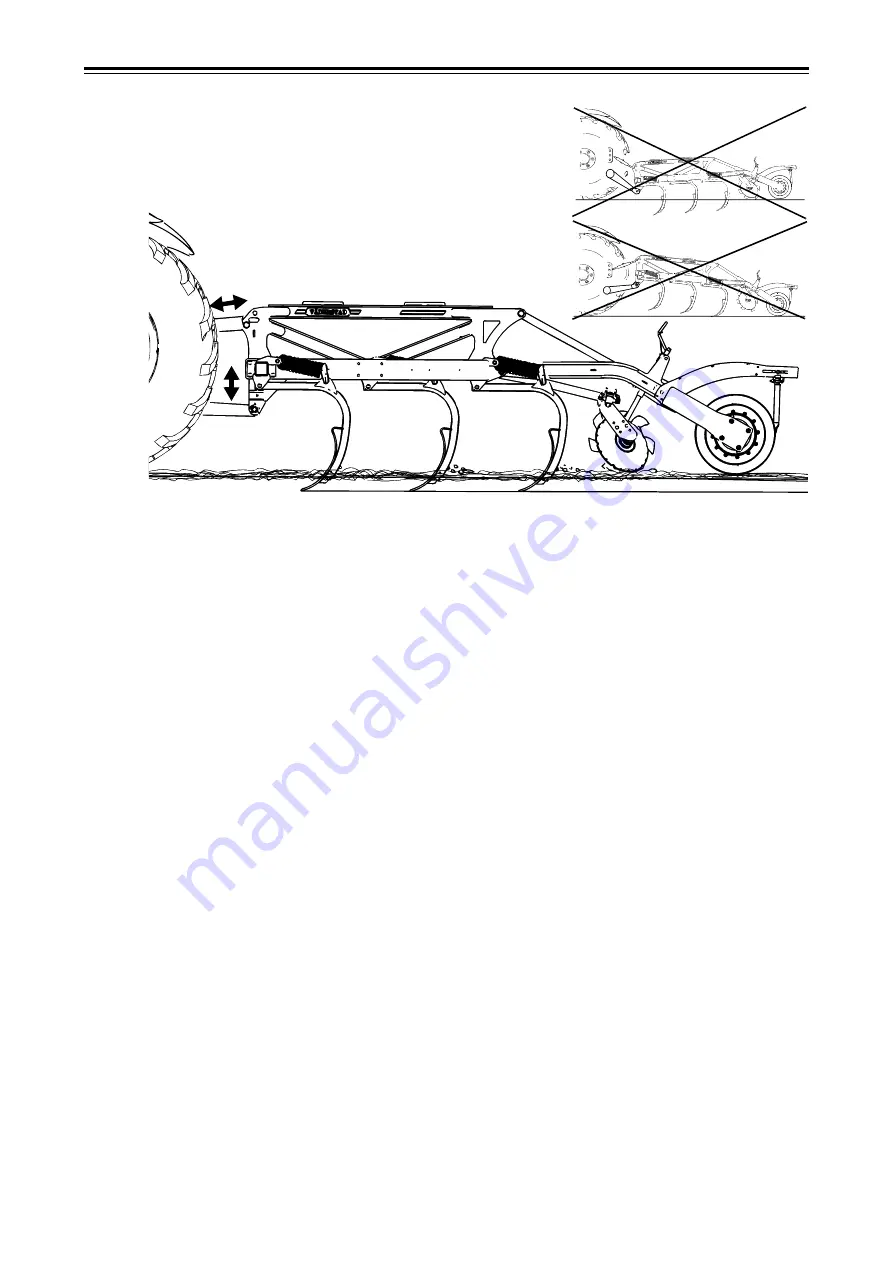
Instructions and settings
22
11.07.2011
ver. 3
2.6
Adjusting parallel alignment, hydraulically mounted
Figure 2.12
The height of the front part of the implement is adjusted with the length of the top rod or the height
of the hydraulic lifting arms, depending on which coupling point has been selected in the imple-
ment’s tower, see
“2.2.3 Choice of coupling points” see page 17
When driving in the field, adjustment takes place when checking that the implement is being
pulled parallel with the ground.
NOTE!
The height of the front part of the implement must be adjusted when changing the position
of the compaction roller, to ensure that the machine is parallel with the ground and to prevent an
uneven working depth.
NOTE!
Poor parallel alignment can result in the implement being unstable when in motion.
Summary of Contents for Cultus Series
Page 2: ...2 11 07 2011 ver 3...
Page 4: ...4 11 07 2011 ver 3...
Page 37: ...CS 300 400 11 07 2011 ver 3 37 5 Hydraulic diagram 5 1 CS 300 400 Figure 5 1...
Page 41: ......