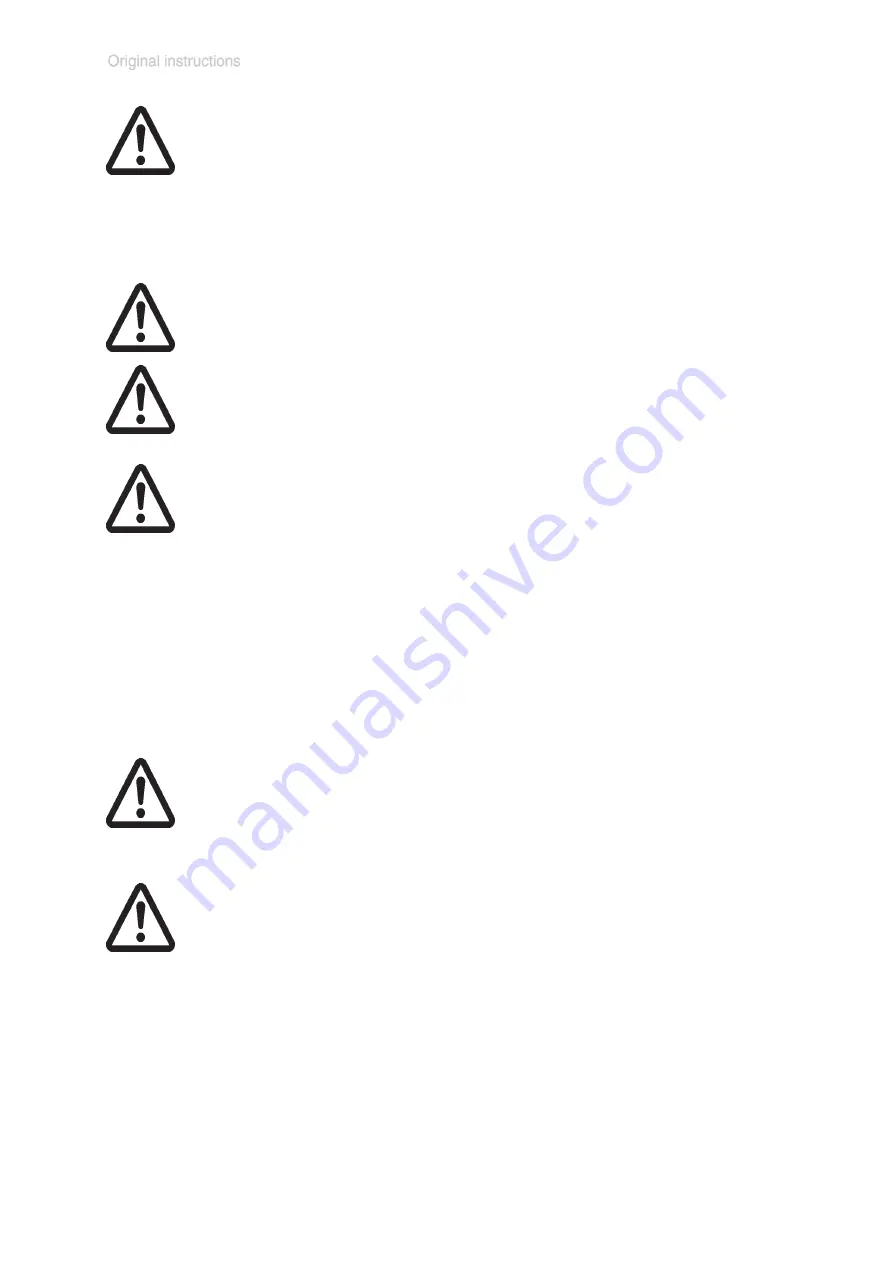
Documents are only to be used and distributed completely and unchanged. It is strictly the users´ responsibility to check
carefully the validity of this document with respect to his product. Manual-no.: 999084 / 05/10/2009
page 6 of 46
In case of overload the motor is shut down by a
thermal cutout
in the winding.
☞
Attention: Manual reset is necessary. Switch off the pump or isolate the equipment
from mains. Wait approx. five minutes before restarting the pump
☞
Attention
: In case of
supply voltage below 100V
, the lock of the cutout might be
restricted and the pump might restart on its own after sufficient cooling down. Take
suitable precautions, if an automatic restart of the pump may lead to a critical
dangerous situation.
☞
Avoid high heat supply (e. g. due to hot process gases).
☞
Ensure sufficient air admittance if pump is installed in a housing.
Due to the residual
leak rate of the equipment
, there may be an exchange of gas,
albeit extremely slight, between the environment and the vacuum system.
☞
Adopt suitable measures to prevent contamination of the pumped substances or
the environment.
Pumping at
high inlet pressure
may lead to overpressure at the gas ballast valve.
☞
Pumped gases or condensate might be pushed out in case the valve is open.
☞
If an inert gas supply is connected, ensure that the inlet pipeline is not contaminated.
The controller is equipped with a
short circuit proof wide-range power supply
with
integrated overload protection and with a fuse 8A(T).
Check the level of condensate in the round bottom collecting flask regularly. Do not
overfill the collecting flask.
Ensure that in case of failure the pump and the vacuum system always will turn into a
safe status.
☞
In case of diaphragm cracks or leaks in the manifold, pumped substances might be
released into the environment or into the pump housing. To reduce the risk of leaks,
ask for a diaphragm pump with additional safety diaphragm.
☞
Comply especially with notes on operation and use and maintenance.
☞
Failure of the pump (e. g. due to power failure) must not lead to a critical dangerous
situation under any circumstances.
Electronic equipment is never 100% fail-safe. This may lead to an indefinite status of
the equipment. Provide protective measures against malfunction and failure.
☞
Operating the pump, stand still of the pump or operating the venting valve must not
lead to a critical dangerous situation under any circumstances.
Attention
: If
Auto-Start
(
Auto-St.
) is preselected, the process starts immediately
after switching on the controller without pressing any further key. It is the user’s respon-
sibility to ensure that no dangerous status of the system due to the automatic startup
of the pump, e.g. after a power failure, can occur and to provide appropriate safety
measures. If necessary, the user has to check
prior to using the equipment
if the
option ”Auto-Start” is enabled.
Use only
genuine spare parts and accessories.
☞
Otherwise safety and performance of the equipment as well as the electromagnetic
compatibility of the equipment might be reduced.
Possibly the CE mark or the C/US conformity becomes void if not using genuine
spare parts.
The A-weighed emission sound pressure level of the pump does not exceed 70 dB(A).
Measurement according to EN ISO 2151:2004 and EN ISO 3744:1995 with standard
silencer or exhaust tube at outlet.
Ensure that maintenance is done only by suitable trained and supervised techni-
cians.
Ensure that the maintenance technician is familiar with the safety procedures
which relate to the product processed by the vacuum system and that the equipment,
if necessary, is appropriately decontaminated before starting maintenance.
Comply with local and national safety regulations.