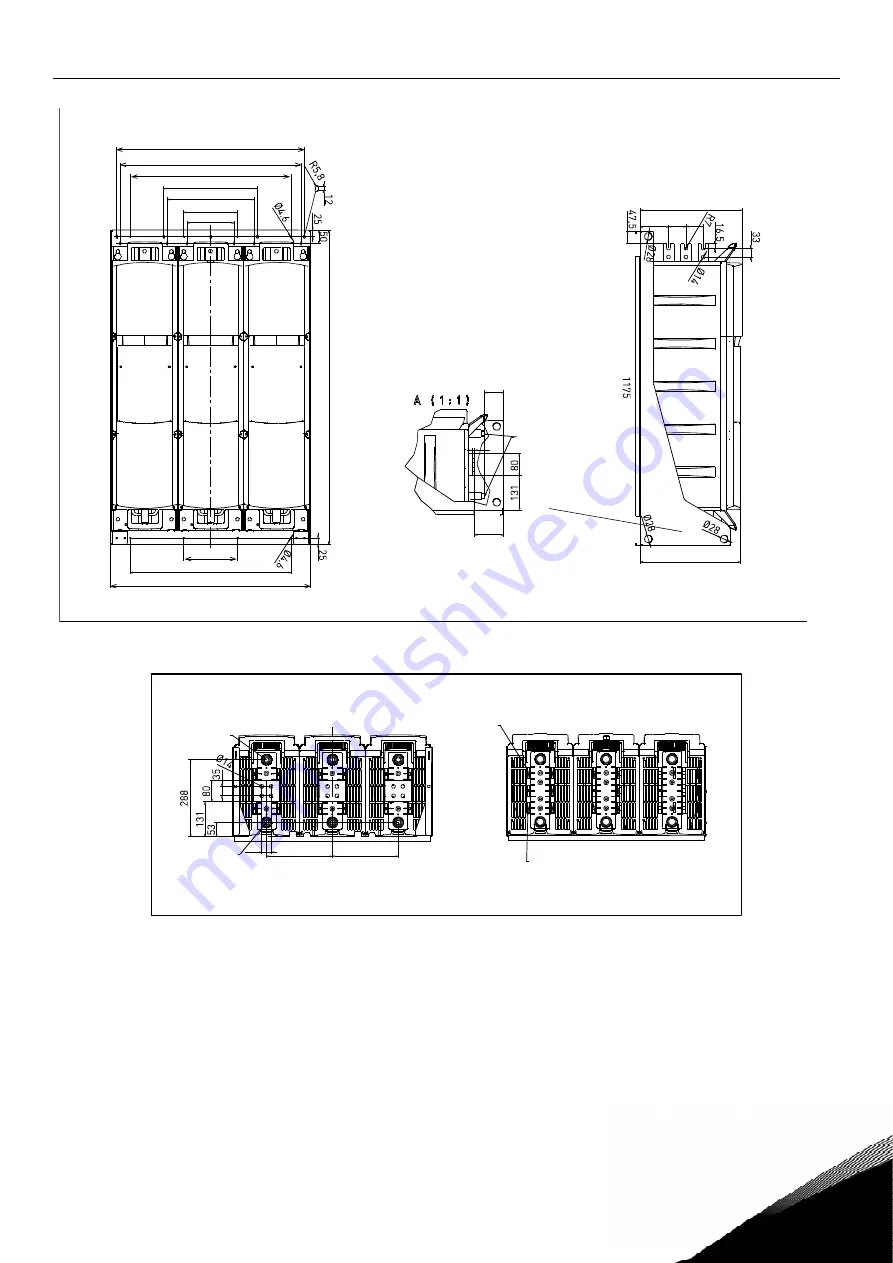
INSTALLATION
vacon • 37
24-hour s358 (0)40 837 1150 • Email: [email protected]
5
381
65
65
106
375
70
G1/2” +USITR-08
10
108
746
600
200
200
175
700
675
600
350
325
Figure 5-16. Vacon NX Liquid-Cooled frequency converter front and side dimensions, CH74, IP00
Coolant out
35
246
246
DC+ connector
DC- connector
Coolant in
Figure 5-17. Vacon NX Liquid-Cooled frequency converter top and bottom dimensions, CH74, IP00