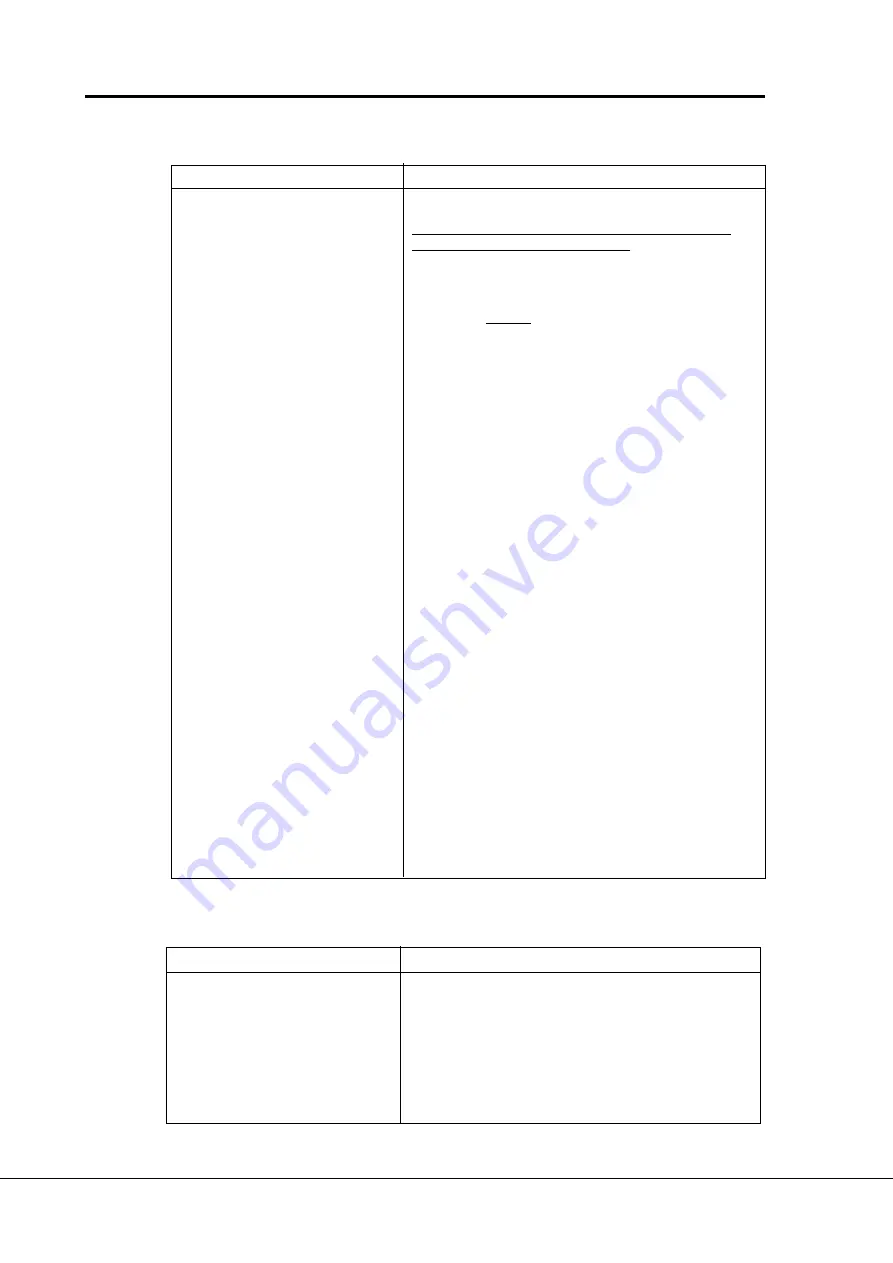
Vacon Plc
Phone: +358-201 2121
Fax:+358-201 212 205
Service: +358-40-8371 150
E-mail: [email protected]
Page 28
Vacon
Pump and fan control with autochange
scale.
3. 6
Digital output function
Setting value
Signal content
0 = Not used
Out of operation
Digital output DO1 sinks current and programmable
relay (RO1, RO2) is activated when:
1 = Ready
The frequency converter is ready to operate
2 = Run
The frequency converter operates (motor is running)
3 = Fault
A fault trip has occurred
4 = Fault inverted
A fault trip has not occurred
5 = Vacon overheat warning
The heat-sink temperature e70°C
6 = External fault or warning
Fault or warning depending on parameter 7
.
2
7 = Reference fault or warning
Fault or warning depending on parameter 7
.
1
- if analogue reference is 4—20 mA and signal is <4mA
8 = Warning
Always if a warning exists
9 = Reversed
The reverse command has been selected
10 = Multi-step or jogging speed
Multi-step or jog. speed has been selected with digital
input
11 = At speed
The output frequency has reached the set reference
12 = Motor regulator activated
Overvoltage or overcurrent regulator was activated
13 = Output frequency supervision 1
The output frequency goes beyond the set supervision
Low limit/ High limit (par. 3
.
9 and par. 3
.
10)
14= Output frequency supervision 2
The output frequency goes beyond the set supervision
Low limit/ High limit (par. 3
.
11 and par. 3
.
12)
15= Torque limit supervision
The motor torque goes beyond the set supervision
Low limit/ High limit (par. 3
.
13 and par. 3
.
14)
16= Active reference
Active reference goes beyond the set supervision
limit supervision
Low limit/ High limit (par. 3
.
15 and par. 3
.
16)
17 = External brake control
External brake ON/OFF control with programmable de
lay (par 3
.
17 and 3
.
18)
18 = Control from I/O terminals
External control mode selected with pr. push-button #2
19 = Frequency converter
Temperature on frequency converter goes beyond
temperature limit supervision
set supervision limits (par. 3
.
19 and 3
.
20)
20 = Unrequested rotation direction
Rotation direction of the motor shaft is different from the
requested one
21 = External brake control inverted
External brake ON/OFF control (par. 3.17 and 3.18),
output active when brake control is ON
22= Analog input limit supervision
The level of selected analog input goes beyond the
set supervision low / high limit (par. 3
.
29 and par. 3
.
30)
23—26 = Not in use
27 = Autochange 3 control
Control signal for drive 3 in autochange system
28 = Auxiliary drive 1 start
Starts and stops auxiliary drive 1
29 = Auxiliary drive 2 start
Starts and stops auxiliary drive 2
30 = Auxiliary drive 3 start
Starts and stops auxiliary drive 3
Table 6-3a Output signals via DO1
3. 7
Relay output 1 content
Setting value
Signal content
0-22 = Same as parameter 3.6
23—25 = Not in use
26 = Autochange 1 control
Control signal for drive 1 in autochange system
27 = Autochange 4 control
Control signal for drive 1 in autochange system with
I/O-expander option
28 = Auxiliary drive 1 start
Starts and stops auxiliary drive 1
29 = Auxiliary drive 2 start
Starts and stops auxiliary drive 2
30 = Auxiliary drive 3 start
Starts and stops auxiliary drive 3
Table 6-3b Output signals via RO1