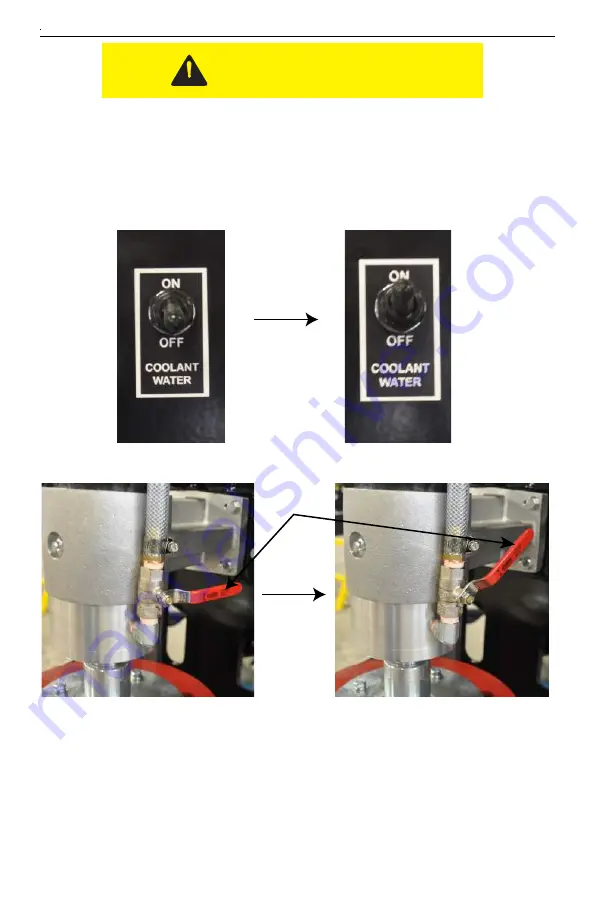
Core Cutting
MTC Coring Unit. Operator’s Manual
© 2016 Utilicor Technologies Inc.
11
ATTENTION
Step 3.
1. Turn on Coolant Water
2. Open Water Petcock (1/8 turn)
3. Verify that water is flowing out through the Pilot Bit.
The coring process requires water to cool the core drum and the pilot bit. Make
sure the water tank is full before you begin the coring operation. The process uses
approximately 1 gallon of water per inch depth cut.
Petcock