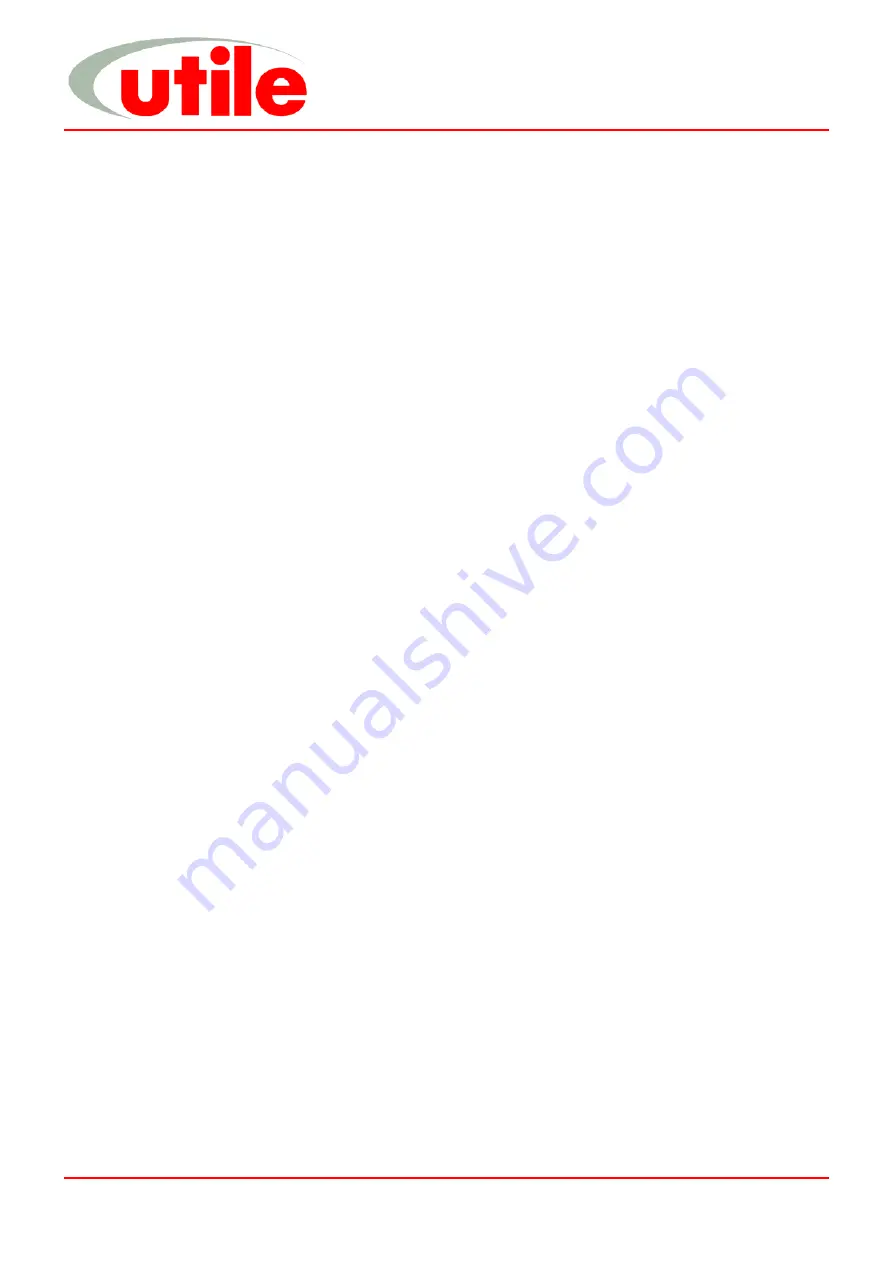
The Utile Engineering Co. Ltd.
15/08/06
Irthlingborough, Northamptonshire. England
Tel: +44 (0) 1933 650216
Fax: +44 (0) 1933 652738
10 IC183
1.
Blade Inspection
When carrying out any maintenance and inspections always follow the health and safety guidelines on page 4.
Ensure all electric circuits are isolated and cannot be switched on, and that the pipeline system has been cleared
and is pressurised to atmospheric pressure. Fully trained and competent service personnel must carry out any
maintenance work.
Inspection commences with the dismantling of the rear end, use parts list drawing on page 12.
1.1
Remove 4-socket head screws (12) the coverplate (3) can be withdrawn leaving the ball bearing (7) on the
shaft.
1.2
Take care not to loose the o-ring (10) fitted between the cylinder (1) and coverplate (3).
1.3
The blades (6) can now be removed form their slots for inspection.
Check the blades for lamination, chipping or charring on their rubbing edges and for concave wear. For any
other wear other than polished surfaces or if the blades depth has reduced to 24mm or below then replace
the blades.
When replacing blades a complete set must be replaced. When fitting new blades, make sure they slide
freely in their slots and if necessary, remove high spots with fine emery cloth.
1.4
Inspect the visible part of the cylinder bore and rotor for any signs of excessive wear or scuffing and for
excessive slot wear. If there is any sign of cylinder rubbing completely dismantle the machine. Factory
reconditioning is recommended, but if work has to be carried out on site, we advise you most strongly to
contact Utile Engineering Service Department for advice.
2.
Reassembly after Blade Inspection
Reassemble in the reverse order taking note of the following points: -
2.1
Ensure the blades (6) are orientated correctly in their slots.
2.2
Fit o-ring (10) into groove in cylinder (1) end face.
2.3
Replace coverplate and screws.
3. Cylinder
Renewal
With the rear end coverplate (3) already removed as described in 1 for blade inspection, the next stage is to
withdraw the rotor complete with the drive end coverplate (2).
3.1
Undo 4 screws (12) and slide off the coverplate (2) complete with the rotor.
3.2
Take care not to loose the o-ring (10) fitted between the cylinder (1) and coverplate (2).
The cylinder can now be replaced.
4.
Removal of Bearings and Seals
With the rear end coverplate (3) already removed as described in 1 for blade inspection.
4.1
Using a two-leg pulley drawer the rear end ball bearing (7) can be removed from the shaft.
4.2
The PTFE ring (14) can be inspected for wear, renew if worn.
With the drive end coverplate (2) already removed complete with rotor as described in 3 for cylinder renewal.
4.3
Using a two-leg pulley drawer the remove the drive end coverplate (2) complete with the shaft seal (8)
leaving the ball bearing on the shaft. Note the position of the thrust washer (9) in the coverplate.
4.4
Using a two-leg pulley drawer the drive end ball bearing (7) can be removed from the shaft.
4.5
The PTFE ring (14) can be inspected for wear, renew if worn
4.6
The shaft seal (8) can be pressed out of the coverplate for inspection.
4.7
Inspect the bearings; renew if they show any signs of wear or pitting.
4.8
Examine the shaft seal (8) and renew if the wiping lip is worn or damaged.
Blade Inspection, Reassembly after
Blade Inspection, Cylinder Renewal,
Change Bearings and Seals