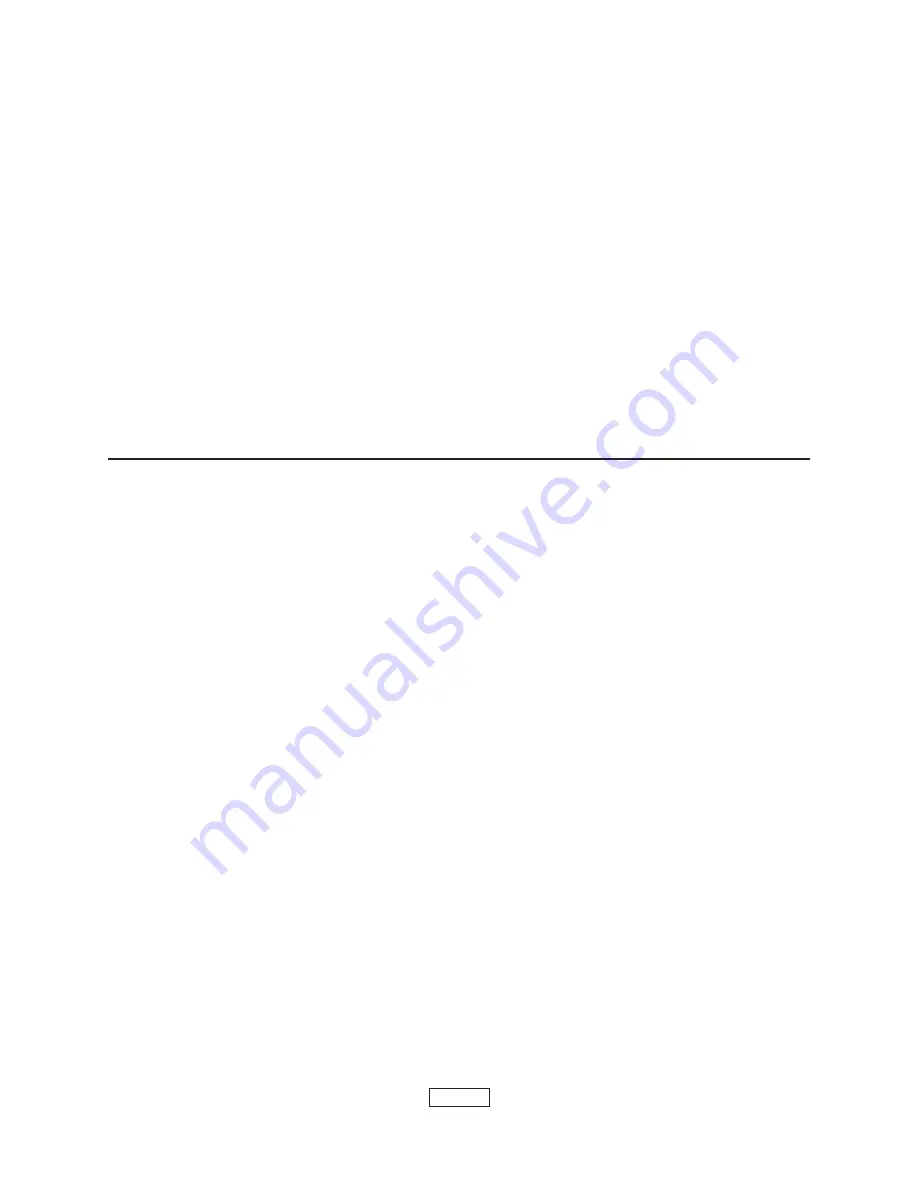
PAGE 15
NORMAL SEQ
NORMAL SEQ
NORMAL SEQ
NORMAL SEQ
NORMAL SEQUENCE OF OPERA
UENCE OF OPERA
UENCE OF OPERA
UENCE OF OPERA
UENCE OF OPERATION
TION
TION
TION
TION
On a call for heat, the thermostat will actuate, completing the circuit to the aquastat. In
turn, the circulator and ignition systems are activated and ignition will begin.
In the event the boiler water temperature exceeds the high limit setting on the boiler mounted
aquastat, power will be interrupted between the aquastat and the ignition system. The power
will remain off until the boiler water temperature drops below the high limit setting. The
circulator will continue to operate under this condition until the thermostat is satisfied.
THERMOST
THERMOST
THERMOST
THERMOST
THERMOSTA
A
A
A
AT INST
T INST
T INST
T INST
T INSTALLA
ALLA
ALLA
ALLA
ALLATION
TION
TION
TION
TION
1. Thermostat should be installed on an inside wall about four feet above the floor.
2. NEVER install a thermostat on an outside wall.
3. Do not install a thermostat where it will be affected by:
A. Drafts
B. Hot or cold pipes
C. Sun light
D. Lighting fixtures
E. Television sets
F. A fireplace or chimney
4. Check thermostat operation by raising and lowering thermostat as required to start and
stop the burner.
5. Instructions for the final adjustment of the thermostat are packaged with the thermostat
( adjusting heating anticipator, calibration, ect.).