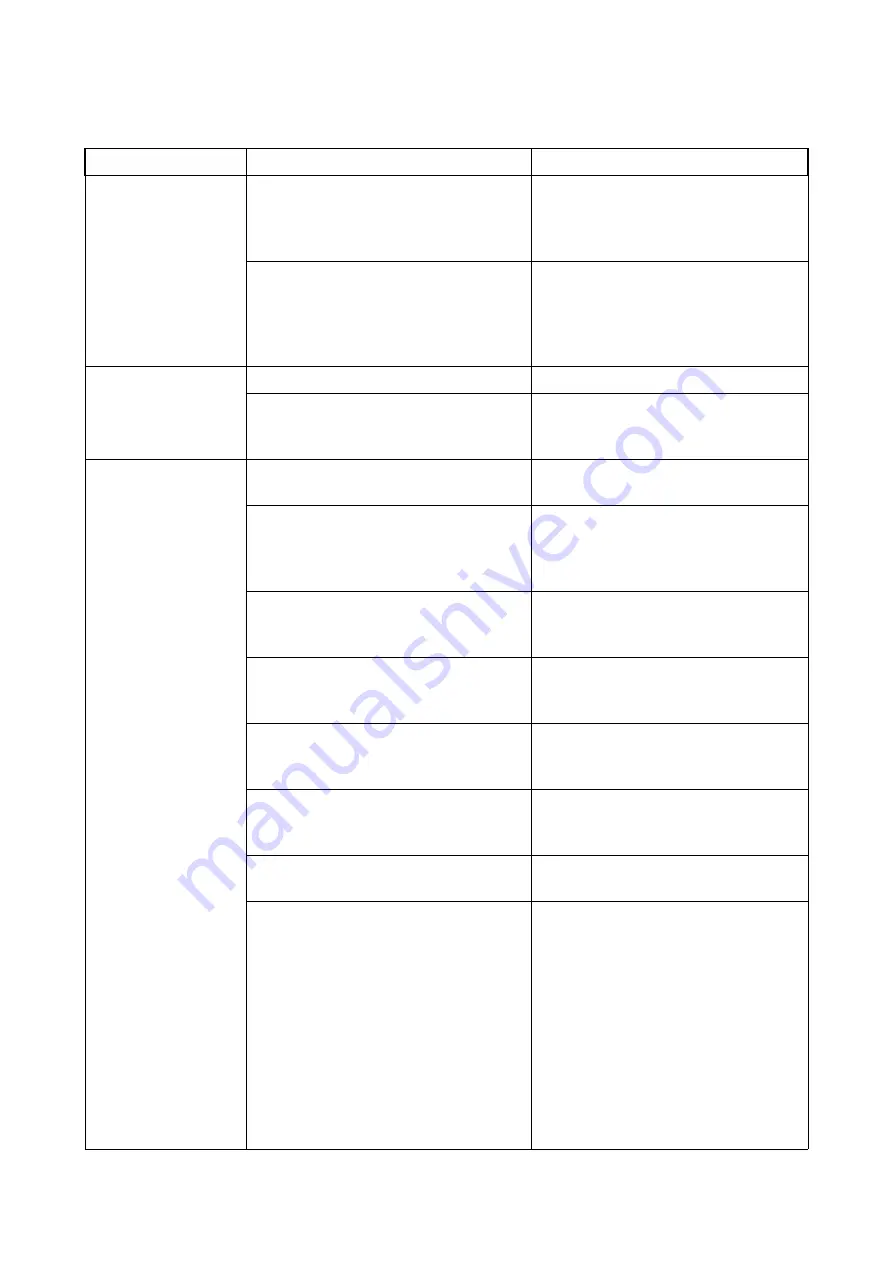
3NV
1-4-8
1-4-4 Mechanical problems
Problem
Causes / check procedures
Corrective measures
(1)
No primary original
feed.
Check if the surfaces of the following pul-
leys are dirty with paper powder.
DP forwarding pulley
DP feed belt
Clean with isopropyl alcohol.
Check if the following pulleys is
deformed.
DP forwarding pulley
DP feed belt
Check visually and replace any
deformed (see page 1-5-2).
(2)
Multiple sheets of orig-
inal are fed.
Original is not correctly set.
Set the original correctly.
Check if the DP separation pulley is
worn.
Replace the DP separation pulley if it is
worn (see page 1-5-5).
(3)
Originals jam.
Originals being used do not conform with
the specifications.
Use only originals conforming to the
specifications.
Check if the surfaces of the following pul-
leys are dirty with paper powder.
DP forwarding pulley
DP feed belt
Clean with isopropyl alcohol.
Check if the contact between the DP reg-
istration roller and DP registration pulley
is correct.
Check visually and remedy if necessary.
Check if the contact between the DP
upper conveying roller and DP conveying
pulley is correct.
Check visually and remedy if necessary.
Check if the contact between the DP left
conveying roller and DP conveying pulley
is correct.
Check visually and remedy if necessary.
Check if the contact between the DP right
conveying roller and DP conveying pulley
is correct.
Check visually and remedy if necessary.
Check if the contact between the DP
eject roller and DP eject pulley is correct.
Check visually and remedy if necessary.
Check if the contact between the DP
switchback roller and DP switchback pul-
ley is correct.
Check visually and remedy if necessary.
Summary of Contents for DP 770
Page 1: ...Service Manual Document Processor D3 Rev 0 Date 0 201 3NVSM06 ...
Page 2: ...Service Manual Document Processor D3 Rev 0 Date 0 201 3NVSM06 ...
Page 5: ...This page is intentionally left blank ...
Page 11: ...This page is intentionally left blank ...
Page 17: ...3NV 1 1 4 This page is intentionally left blank ...
Page 21: ...3NV 1 2 4 This page is intentionally left blank ...
Page 67: ...3NV 1 3 46 This page is intentionally left blank ...
Page 85: ...3NV 1 5 10 This page is intentionally left blank ...
Page 87: ...3NV 1 6 2 This page is intentionally left blank ...
Page 95: ...3NV 2 1 8 This page is intentionally left blank ...