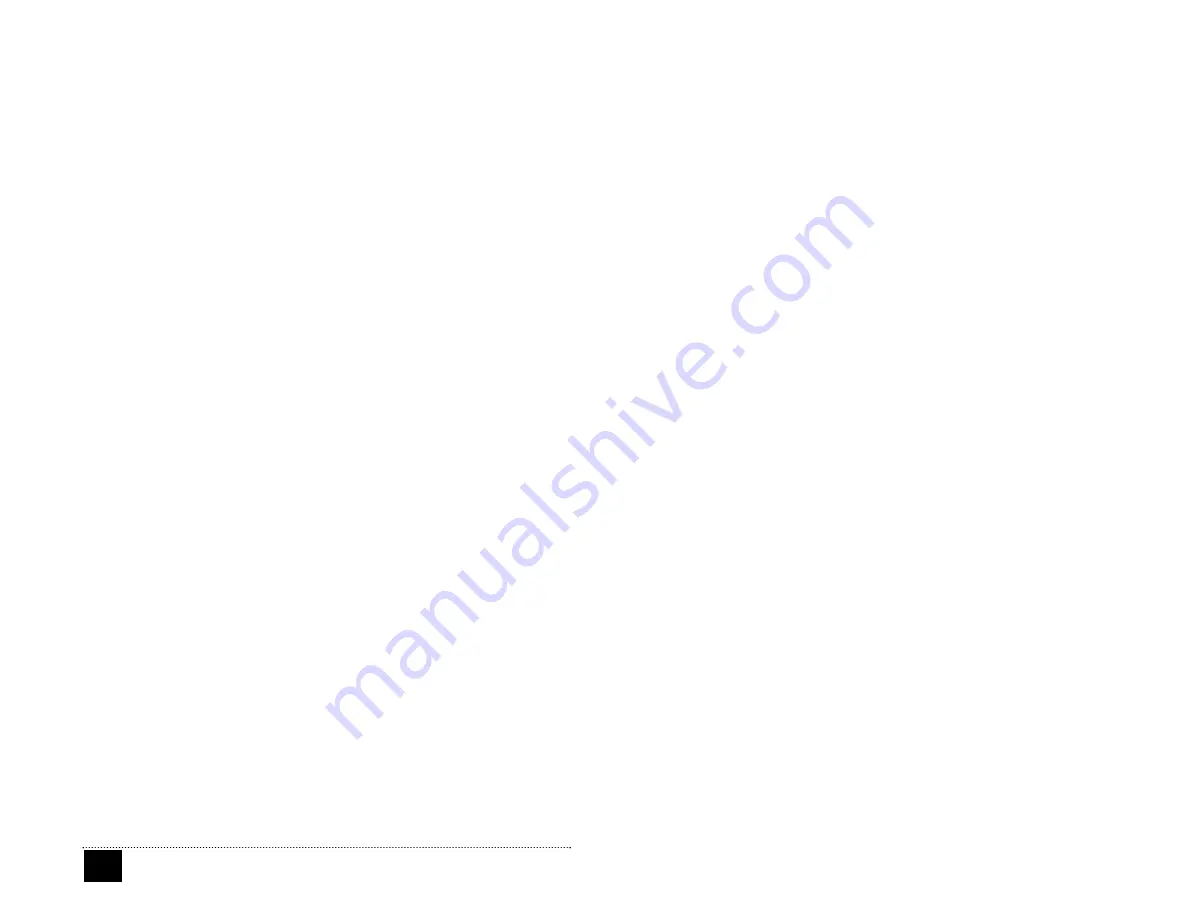
from the high frequency waveform generator. This converter is trans-
former coupled to the base of the output preamplifier which, in turn,
drives the final output stage.
Waveform Generation
Each of the cut, blend, and coag modes are distinguished from each
other by the voltage waveforms delivered to the output terminals.
All of these waveforms are originally derived from a 450 kHz square
wave oscillator on the logic board. In the pure cut mode, the
unmodified 450 kHz square wave is applied to the gate of the chop-
per FET in the DC-AC converter. In the blend modes and in the
coag mode, the continuous square wave is interrupted for various
durations. Blend 1 removes 6 cycles of every 16 for a duty cycle of
62.5 percent. Blend 2 removes 8 cycles of 16 for a duty cycle of 50
percent. Blend 3 removes 10 of 16 for a duty cycle of 37.5 percent,
and the coag mode removes 15 of 16 for a duty cycle of 6.25 per-
cent.
Cycle removal for these functions is accomplished using a ripple
counter, an array of gates, and a D-type flip flop. The 450 kHz oscil-
lator is disabled unless either the cut/blend switching circuit or the
coag switching circuit is active.
RF Power Amplification
After the variable-amplitude, output-control voltage is converted to
AC by the DC-AC converter, the resultant RF signal is transformer
coupled to the input of the preamplifier and amplified in two stages
to the level necessary for performing electrosurgery. The preamplifier
consists of a bipolar power transistor with collector-to-base local
feedback and a transformer coupled to the final output stage. With
the exception of the power transistor itself, which is mounted on the
back panel heat sink, all components of the preamplifier are mount-
ed on the RF power board.
The final output stage uses four parallel power transistors mounted
on a fan-cooled internal heat sink. Other components of this circuit,
which consist of biasing resistors, output transformer, and output
coupling capacitors are mounted on the RF power board.
The RF output is coupled to the active and dispersive output termi-
nals through an output transformer with series capacitors in both
leads. This results in an output which is RF isolated from ground and
which is incapable of conducting low frequency currents which may
cause serious neuromuscular stimulation in the patient.
Feedback Circuit
Feedback control of the output is provided to 1) limit the maximum
open circuit output voltage, 2) regulate the output to optimum levels
under various cutting conditions, and 3) diminish the sensitivity of
the cutting output to line voltage variations. The output voltage is
detected by a high frequency bridge rectifier connected across the
secondary of the output transformer. This rectifier produces a DC
output which is proportional to the peak RF voltage across the output
terminals. This proportional voltage is applied to the LED input of a
opto-isolator device, and the emitter voltage from the isolator is fed
back to the cut/blend gain and offset control amplifier on the digital
display board.
With this circuit in place, an increase in the output, caused by a
decrease in load current or any other cause, will be detected and
subtracted from the output control signal, which will, in turn, result
in less drive to the preamplifier and, therefore, less change in the
output. Conversely, any attempted decrease in the output voltage
will be suppressed by the opposite action.
The degree of feedback control is adjustable using R333 on the
power board. This resistor is adjusted as part of the factory calibra-
tion procedure. It is interactive with the power gain adjustments.
Changing it without corresponding adjustment of the gain will result
in miscalibration of the generator.
Function Switching Circuits
The commonly available hand switches for electrosurgery have three
wire connections to the generator with two single pole switches for
cut/blend and coag. The active lead to the electrosurgical imple-
ment is the common wire for both switching functions. To maintain
RF isolation of the generator output, it is necessary that the hand
Finesse Service Manual
12
Summary of Contents for Finesse ESU-110
Page 4: ......
Page 10: ...Finesse Service Manual 6 ...
Page 27: ...Mains Power Wiring Diagram Finesse Service Manual 23 ...
Page 28: ...Assembly Diagram Finesse Internal View Finesse Service Manual 24 ...
Page 29: ...RF Power Board Assembly Drawing Finesse Service Manual 25 ...
Page 30: ...Logic Board Assembly Drawing Finesse Service Manual 26 ...
Page 31: ...Display Board Assembly Drawing Power Supply Board Assembly Drawing Finesse Service Manual 27 ...
Page 32: ...System Functional Diagram Finesse Service Manual 28 ...