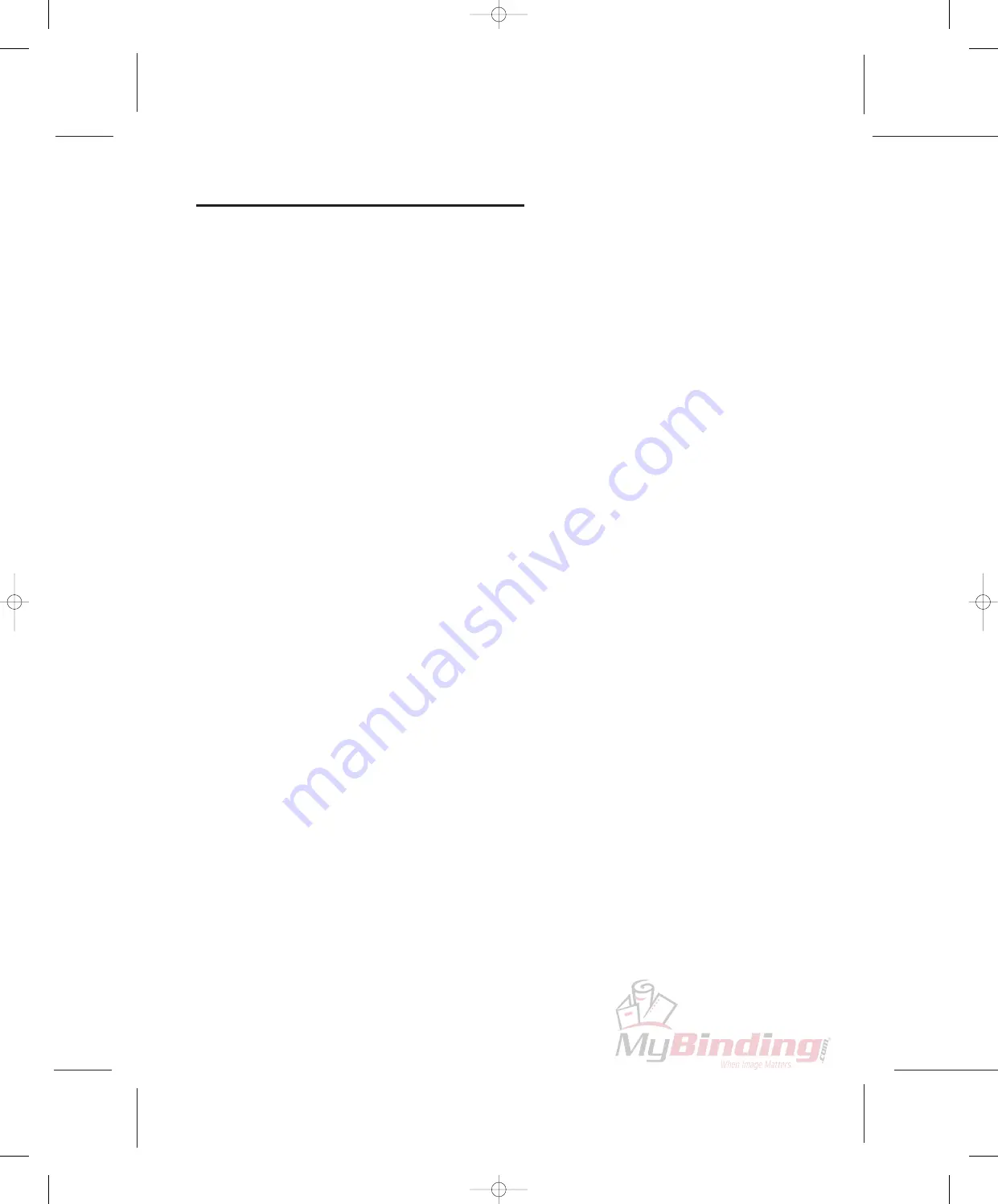
22
USI • YOUR SOURCE FOR LAMINATION
TROUBLE SHOOTING
COMMON EXAMPLES OF PROBLEM LAMINATING . . . and their causes.
A. FILM NOT BONDING TO SUBSTRATE OR TO ITSELF AT SEALED EDGES
Causes:
1. The heat (on either or both heat shoes) is set too low.
2. Film tension is too tight.
3. Film is threaded incorrectly.
4. The pressure setting is not correct.
B. WRINKLES OR IRREGULAR WAVES RUNNING ACROSS THE LAMINATED WEB
(PERPENDICULAR TO THE EDGE)
Causes:
1. The heat set is too high.
2. Not enough tension on the supply mandrels. (Large, irregular waves).
3. Too much tension on the supply mandrels. (Small, fine wrinkles known as the “orange peel” effect).
4. The rubber laminating rollers are not clean.
5. The pressure adjustment for the laminating and pull rollers is out of adjustment.
C. STRETCH LINES RUNNING WITH WEB (PARALLEL TO THE EDGE)
Causes:
1. Too much tension on the supply mandrels.
2. The heat is set too high on either or both heat shoes.
3. The heat shoes or rollers are not clean.
D. BLISTERS ON SURFACE OF SUBJECT OR ALONG EDGE OF SUBJECT
Causes:
1. The heat is set too high on either or both heat shoes.
2. Excessive moisture in the paper being laminated. (If inks are not dry, this may also cause blisters).
For high moisture content substrates, use USI’s low temperature films with a
bonding temperature of 185°—190°. For best results, allow the prints to dry fully.
3. The rubber laminating rollers are not clean, or are damaged.
4. The rollers are not in full press position (rotated fully clockwise.)
E. CURLING OF THE FINISHED LAMINATION
Causes:
1. Unbalanced tension on the supply rolls. Too much tension on the top supply roll will cause
the web to curl up. Too much tension on the bottom roll will cause a downward curl in the web.
2. Film has been threaded incorrectly.
3. Heat is unbalanced in the top or bottom heat shoes. If the subject curls up, there is too
much heat in the top shoe. If it curls down, there is too much heat on the bottom shoe.
F.
WRINKLING AROUND EDGE OF LAMINATED ITEM
Causes:
1. Item to be laminated is too thick.
Possible Solutions:
a. Loosen tension
b. Use thicker film
c. Flush cut item
G. BOTTOM RUBBER ROLLERS TURN BUT TOP RUBBER ROLLERS DO NOT
1. The tension is too tight.
2. Film has not been threaded correctly.
3. Film was loaded backwards. (Adhesive against heaters)
4. Not enough roller pressure.