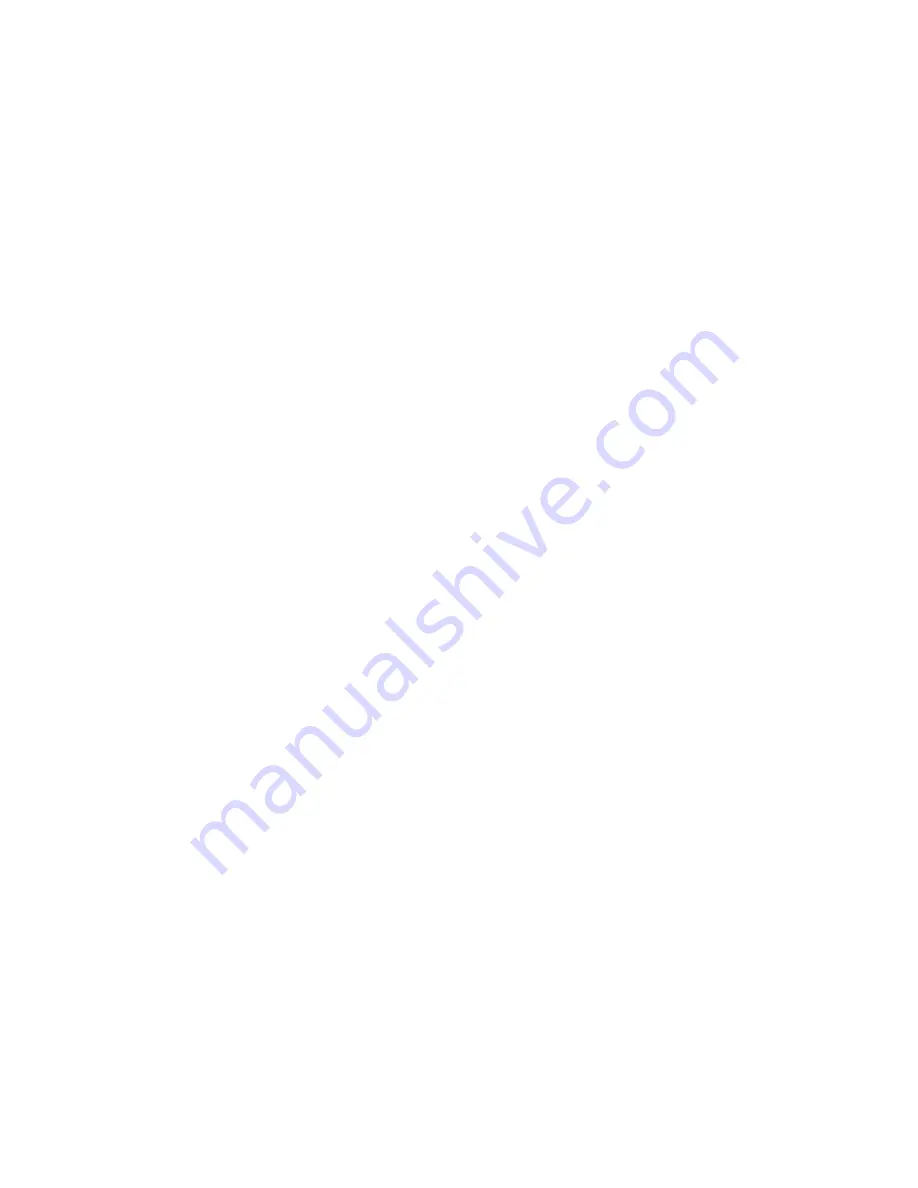
25
SETUP MENU
TPS Setup
= Clicking this will take you to the TPS Setup menu, which shows
the idle and WOT settings as well as the current voltage of the TPS. Clicking
once will open the menu. Clicking AutoSet TPS will take you through the steps
to calibrate your throttle position sensor settings. You can also manually adjust
these settings by clicking Adjust Idle or Adjust WOT. Reset TPS will erase the
saved TPS data from the controller, reverting back to the TPS voltages saved in
the loaded tune file. See page 8 for more details.
Speedo Out
= Provides configuration options for the speedometer output. See
page 14 for more details.
Speed Sensor
=
This menu allows you to choose your speed sensor type and
configure its details such as speedometer drive gear teeth, driven gear teeth,
and pulses per revolution. Rotating the knob in this screen changes the speed
sensor type. Available speed sensor types will vary depending on the current
transmission type. If other options, such as speedometer gear teeth, pulses per
revolution etc. are available for a specific sensor type, pushing the knob will
bring up a menu that allows you to change the adjustment mode or to exit. If no
options are available for the selected sensor type, pressing the knob will exit this
screen and save the settings. After scrolling through all the speed sensor types,
the last option is to reset the speed sensor settings. This will revert all of the
settings for the speed sensor, axle ratio, and tire diameter back to the defaults
from the currently loaded tune.
Axle Ratio
=
Allows you to input your axle ratio, which improves speed display
accuracy in the home screen and will also will affect speed sensor calibration for
certain types of speed sensors.
Tire Diam
= Allows you to input your tire diameter, which improves speed
display accuracy in the home screen and will also will affect speed sensor
calibration for certain types of speed sensors.
Engine RPM In
=
Allows the adjustment of the engine RPM input configuration.
This includes pulses per revolution and type of RPM sensor or signal. Turning
the knob allows adjustment of pulse rate, while pressing the knob will bring up a
menu of options including preset pulse rates, signal types, and the exit option
(which also saves these settings).
Summary of Contents for 4L60E
Page 1: ...Installation and Operation Manual for 4L60E 4L65E and 4L70E Transmissions...
Page 6: ...6...
Page 12: ...12 TRANSMISSION DIAGRAMS...
Page 17: ...17...
Page 23: ...23 Home Screen Normal Mode Home Screen Enlarged Mode...
Page 38: ...38...
Page 39: ...39...