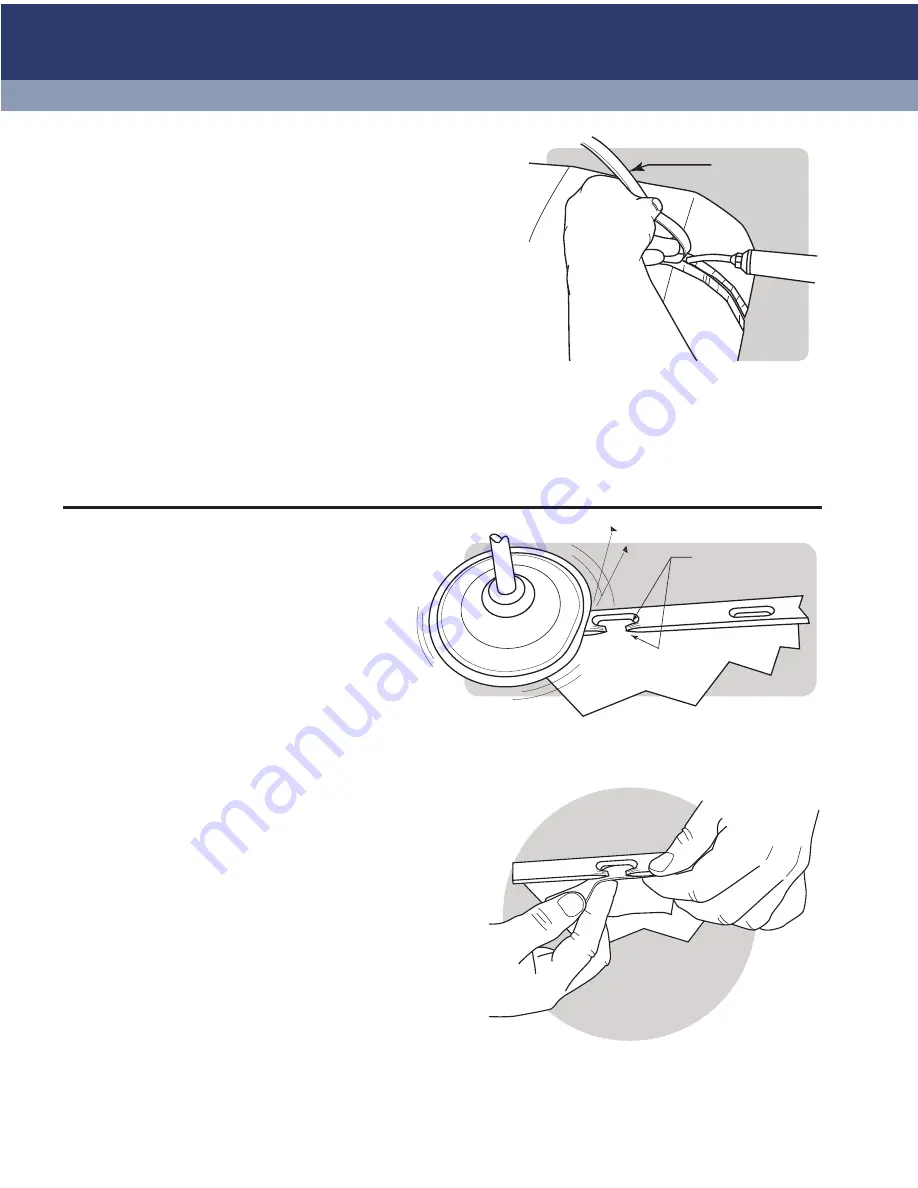
Page 6
www.urethanesupply.com
f.
Weld the front side of the crack
. On the front, it’s usually best
to use the narrow, thin R13 rod. This will tuck down into the
v-groove and retain most of its strength even after it’s been
sanded flush. Use the same process as on the backside to weld
it. However, the R13 will melt and bend much more easily since
it’s thinner. It’s best to focus the heat from the welder a little
farther in front of the point where the rod meets the bumper to
keep the rod from becoming too weak. You need to apply about
a pound of downward pressure on the rod as you do your weld
to make sure the rod fuses properly with the bumper.
g.
Finishing the weld
. Once the weld is completely cool, sand
with 50-80 grit paper in a grinder or DA. Be careful not to sand
too fast; this will just melt and smear the plastic. It’s best to use
a sharp, new piece of paper and slow the sander down a bit to
keep the plastic from melting. Sometimes the repair may be
finished out and feathered with the welding rod, but most often
you’re going to need some filler to fill in the low spots. Please
see our “Book of Plastic Repair” for more information on how
to apply filler on plastic parts.
Welding a broken bumper slot
Because of the strength provided by the nitrogen weld-
ing system, you can make strong repairs even when you
don’t have a lot of surface area to weld to. A perfect ex-
ample is the slots on the edge of the bumper where the
bumper snaps into the quarter panel, like on a Honda
bumper. These often seem to break out when the bump-
er is removed. There’s not enough surface area to make
a good repair with either a two-part system or with the
FiberFlex. Here’s how you fix a torn-out bumper slot.
a.
Clean the plastic
f
irst
. Do this every time
BEFORE you touch it with sandpaper. Clean the
plastic with soap and water first, then with 1000
Super Clean plastic cleaner.
b.
Taper the edges with sandpaper
. Using 50 to 80 grit sand-
paper, remove paint from the area to be welded and taper
the ends down to a point on both sides. This will give you
enough surface area to stick to when you finish the repair.
c.
Apply tape to support rod during weld
. Use the 6481-1 or
6485 aluminum body tape underneath the hole to support
the melted plastic welding rod. You can also clamp a strip
of sheet metal or wood along the edge if that works bet-
ter. Make sure the edge of the support is at the edge of the
plastic so it doesn’t interfere with the clamp and leave room
between the clamps to use the hand seamer as described in
Step F.
Taper both
sides
R13
PP Ribbon
Step F - Welding the front side of the crack with R13 PP
ribbon
Step B - Tapering the edges of the slot to be repaired with sandpaper. Taper
both sides down so the rod has surface area to stick to once sanded.
Step C - Applying aluminum tape to support the melted welding
rod. You can also clamp a wooden stick underneath to provide
extra support.