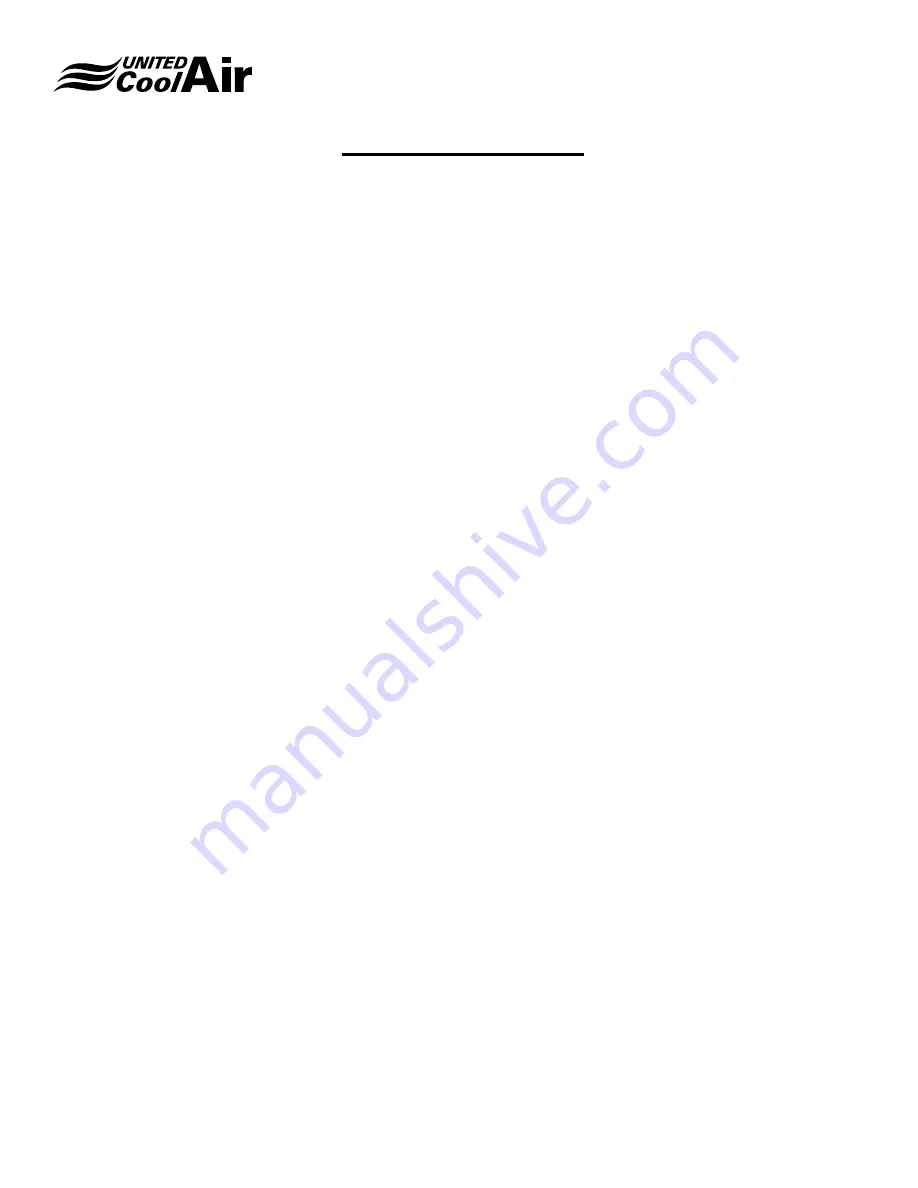
Installation, Operation and Maintenance Manual
VertiCool Classic
35
Subject to change without notice.
20.10-IM (0617)
Water-Cooled Unit
Start-Up Procedures
(R-410a Systems)
1.
Start up must be performed by a qualified HVAC
Technician�
2.
Make certain that all power is disconnected at the main
power circuit breaker or service disconnect before
starting any of this procedure�
3.
Check all electrical screw terminals and wiring lugs
for tightness internal to the equipment� Components
may have loosened due to vibration during transit
or handling� Verify that the main power block lug
connections made in the field are tight and secure.
4.
Confirm that the voltage rating of the equipment data
tag coincides with the power that will be delivered to
the unit�
5.
Verify that the circuit protection for the unit satisfies
Local and National Codes according to the unit data
tag Minimum Circuit Ampacity (MCA) and Maximum
Fuse Size (MFS)�
6.
Locate the unit thermostat and check all electrical
terminations against the unit electrical diagram and for
the unit thermostat�
Note: If using a digital thermostat with a “C” (Common)
terminal, this terminal MUST be terminated to the “C”
terminal in the unit. Failure to do so will result in the
thermostat shorting out and being destroyed.
7.
Leak check the refrigerant system� While the unit was
leak checked at the factory, leaks can develop during
transit and / or handling�
8.
Confirm that the unit condensate has been adequately
trapped and taken to a suitable point for disposal�
9.
Verify that the filters are in place, clean and usable.
10.
Switch the unit thermostat to the “OFF” position�
11.
Apply power to the unit� Switch the circuit breaker or
field supplied electrical service disconnect switch to the
on position�
Note: If the unit has crankcase heaters and the surrounding
ambient is 70˚ F or lower, let the compressors sit for
approximately 24 hours before proceeding.
12.
Record the voltage at the unit terminals�
13.
If possible with the thermostat provided, switch the
evaporator blower to the RUN or ON position� Verify
that the evaporator blower is activated�
14.
Verify that the evaporator blower is rotating in the
correct direction (three phase units only)�
Note: If the evaporator blower motor runs backwards,
shut off all power to the unit. Switch any two of the
incoming power leads at the unit main power terminal
block. The unit has been wired and phased properly
at the factory. DO NOT change any factory wiring to
correct for a phase problem.
Note: Before conducting the following start up sections
connect a suitable refrigerant gauge set to the unit
Schrader connections. Install temperature sensors to
record the appropriate refrigerant line temperatures.
15.
Set the thermostat switch to a temperature set point
approximately 5˚ lower than the space temperature.
Set the thermostat fan switch to the AUTO position� Set
the thermostat operating mode to the COOL position�
This should energize the compressor(s) and evaporator
blower�
Note: Dependent upon the options and/or the thermostat,
there may be a delay for the compressor(s) operation.
16.
While waiting for the compressor(s) to stabilize, record
the External Static Pressure (ESP) for the evaporator
blower�
Note: Make sure all the unit access panels are in place when
taking these readings.
17.
Verify that the incoming water / fluid pressure does not
exceed the rating for the water / fluid control valves.
18.
Verify that the unit piping and heat exchangers will not
be subjected to freezing conditions�
19.
Confirm that no joints are leaking in the cooling fluid
circuit(s)�
20.
Document the type of fluid being used as the cooling
medium� If glycol is being used, make sure the mixture
is adequate for any low ambient conditions that may be
possible�
21.
If possible, record the fluid flow rate (GPM).
a.
Make sure the flow rate is within the proper limits:
i.
Minimum 2�5 GPM / Ton
ii.
Maximum 3�5 GPM / Ton
Continued on next page
Summary of Contents for VertiCool CLASSIC
Page 2: ......