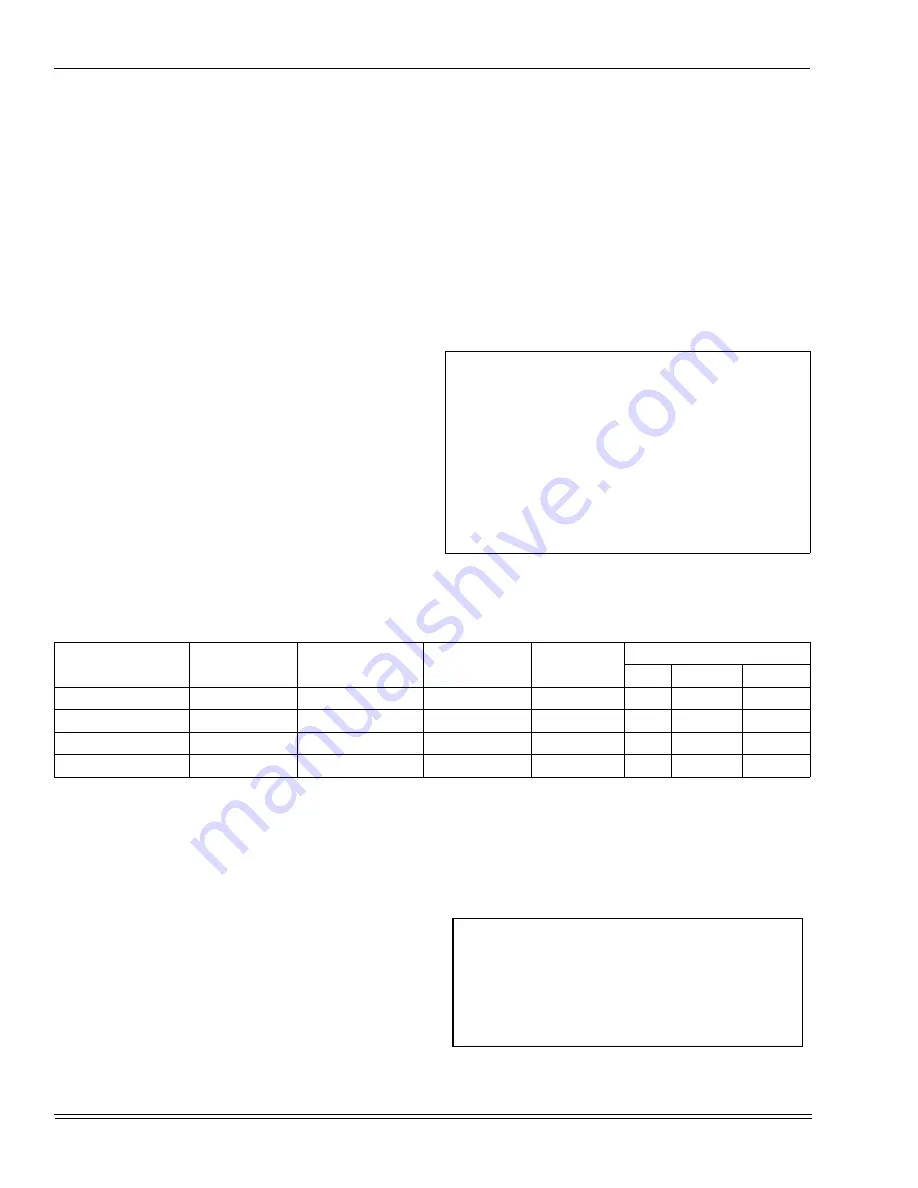
035-17438-001 Rev. A (901)
24
Unitary Products Group
REPLACEMENT OF THE VARIABLE SPEED
MOTOR WITH A MULTI-SPEED PSC DIRECT
DRIVE MOTOR
NOTE:
A failed variable speed motor should always be
replaced with a variable speed motor suitable for the furnace
model being serviced. However, if one is not available, a
multi-speed direct drive motor may be used in the interim.
REMOVAL OF THE VARIABLE SPEED BLOWER
ASSEMBLY AND MOTOR
Follow the Blower Removal Instructions in the Maintenance
section of this instruction under, “BLOWER CARE” on
page 21.
1.
Loosen the blower wheel set screw and the motor mount
bolt, and slide the variable speed motor out of the blower
housing.
INSTALLATION OF PSC MOTOR
1.
Install the PSC multi-speed direct drive motor into motor
mount. See table for proper motor and capacitor part
numbers. See Table 7.
2.
Slide motor in motor mount insuring there is no interfer-
ence between moving and stationary parts. Position wire
leads downward. Tighten motor mount screw to 30 in.
lbs.
3.
Center the blower wheel in the blower housing and align
the shaft flat with the blower wheel set screw. Tighten set
screw to 15 ft. lbs.
4.
Replace blower assembly and fasten with 3 screws
5.
Strap motor capacitor to electric panel. See Table 7.
6.
Fasten electric panel to blower housing.
7.
Remove red wire from Circ. input terminal. Plug jumper
wire (attached to motor power harness) on 120 volt line
terminal on ignition control and jumper to CIRC. INPUT
Connect brown door switch wire to jumper.
8.
Connect white main harness lead to Line neutral.
9.
Connect motor leads to cool, heat lo and heat high per
Table 6.
10. Connect brown capacitor leads from motor to capacitor
and cover terminals with boot supplied.
FURNACE CONTROL DIAGNOSTICS
The furnace has built-in, self diagnostic capability. If a system
problem occurs, a fault code is shown by a blinking LED. It is
located behind a clear view port in the blower compartment
door. DO NOT remove the furnace blower compartment
panel OR turn off furnace power as either action will clear the
control's memory of the fault.
The control continuously monitors its own operation and the
operation of the system. If a failure occurs, the LED will indi-
cate the failure code. If the failure is internal to the control, the
light will stay on continuously. In this case, the entire control
should be replaced as the control is not field repairable.
If the sensed failure is in the system (external to the control),
the LED will flash in the following flash-pause sequences to
indicate failure status.
Flash sequence codes 2 thru 8 are as follows. LED will turn
on for 1/4 second and off for 1/4 second. This pattern will be
repeated the number of times equal to the code. For exam-
ple, six on flashes equals a number 6 fault code.
All flash code sequences are broken by a 2 second off period.
POWER SUPPLY POLARITY - Ignition Control
If the power supply polarity is reversed, the following unit
operation will occur. On a call for heat, the inducer will
run, the HSI will glow and the gas valve will energize and
the burners will ignite. The burners will immediately
extinguish and the unit will recycle. This will occur 3
times and then the unit will lockout. A “7” flash code will
be displayed. This code means the flame could not be
established. This occurs because the control cannot
sense flame with the power supply polarity reversed.
Table 7:
PSC MOTOR SELECTION
Model Number
Motor Part Num-
ber
Motor Horsepower
Capacitor Part
Number
Capacitor
Rating MF
Motor Speed Chart
Cool
Heat LO
Heat HI
80 / 64 / 1200 / “A”
024-31969-000
1/3
024-20045-000
7.5
BLK
BLU
BLK
100 / 80 / 1600 / “B”
024-27540-000
1/2
024-20046-000
10.0
BLK
RED
BLU
100 / 80 / 2000 / “C”
024-23238-001
1
024-20446-000
15.0
BLK
RED
BLU
120 / 96 / 2000 / “C”
024-23238-001
1
024-20446-000
15.0
BLK
BLU
BLK
IGNITION CONTROL (P/N 031-01909-000) Normal
flame sense current is approximately
2.4 microamps DC (
µ
a)
Low flame signal control lockout point is
0.15 microamps (DC (
µ
a)