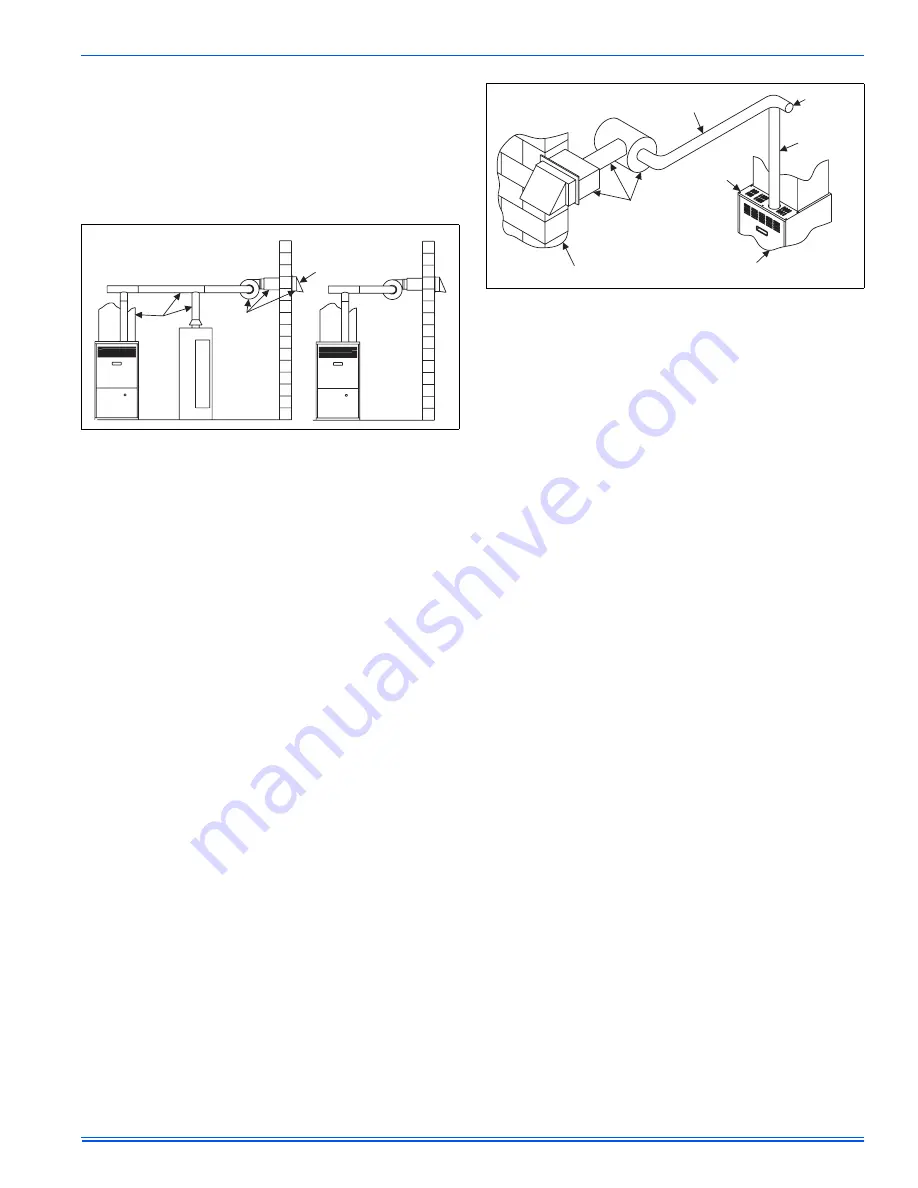
166753-UIM-C-0706
Unitary Products Group
15
HORIZONTAL SIDEWALL VENTING
HORIZONTAL SIDEWALL VENTING
HORIZONTAL SIDEWALL VENTING
HORIZONTAL SIDEWALL VENTING
For applications where vertical venting is not possible, the only
approved method of horizontal venting is the use of an auxiliary power
vent. Approved power venters are Fields Controls Model SWG-4Y or
Tjernlund Model GPAK-JT. Follow all application and installation details
provided by the manufacturer of the power vent. This unit may be hori-
zontally vented using 4” (10.2 cm) diameter pipe with a minimum length
of 4.5 feet (1.37 m) and a maximum length of 34.5 feet (10.82 m) with
up to 4 elbows.
VENT PIPING ASSEMBLY
VENT PIPING ASSEMBLY
VENT PIPING ASSEMBLY
VENT PIPING ASSEMBLY
The final assembly procedure for the vent piping is as follows:
1.
Cut piping to the proper length beginning at the furnace.
2.
Deburr the piping inside and outside.
3.
Dry-fit the vent piping assembly from the furnace to the termination
checking for proper fit support and slope. Piping should be sup-
ported with pipe hangers to prevent sagging. The maximum spac-
ing between hangers is 5 feet (1.5 m).
4.
Assemble the vent piping from the furnace to the termination
securing the pipe connections with screws.
VENT CLEARANCES
VENT CLEARANCES
VENT CLEARANCES
VENT CLEARANCES
IMPORTANT:
The vent must be installed with the following minimum
clearances as shown in Figure 20, must comply with local codes and
requirements.
FIGURE 17:
Typical Sidewall Vent Application
FAN ASSISTED FURNACE
& WATER HEATER
FAN ASSISTED
FURNACES
VENT
PIPE
HOT
WATER
TANK
FURNACE
OPTIONAL
SIDEWALL
VENT SYSTEM
(field supplied)
EXTERIOR
VENT HOOD
FIGURE 18:
Typical Sidewall Vent and Termination Configuration
VENT PIPE
FLUE
PIPE
BURNER
ACCESS
PANEL
CELLAR
WALL
OPTIONAL
SIDEWALL
VENT SYSTEM
(field supplied)
TOP
COVER
VENT
DAMPER