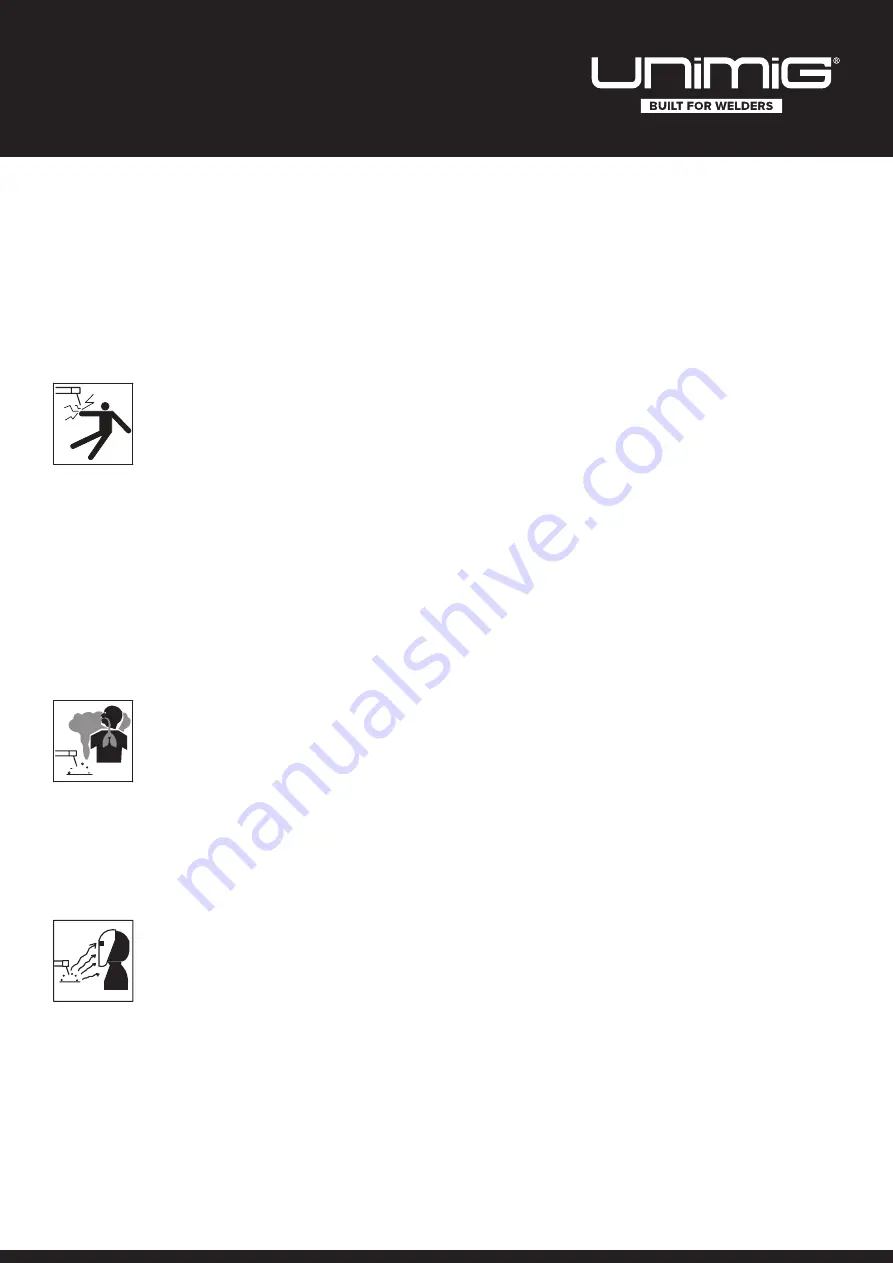
Welding and cutting equipment can be dangerous to both the operator and people in or near the surrounding working area, if the equipment is not
correctly operated. Equipment must only be used under the strict and comprehensive observance of all relevant safety regulations.
Read and understand this instruction manual carefully before the installation and operation of this equipment.
Machine Operating Safety
• Do not switch the function modes while the machine is operating. Switching of the function modes during welding can damage the
machine. Damage caused in this manner will not be covered under warranty.
• Disconnect the electrode-holder cable from the machine before switching on the machine, to avoid arcing should the electrode be in
contact with the work piece.
•
Operators should be trained and or qualified.
Electric shock: It can kill.
Touching live electrical parts can cause fatal shocks or severe burns. The electrode and work circuit is
electrically live whenever the output is on. The input power circuit and internal machine circuits are also live when power is on. In MIG/
MAG welding, the wire, drive rollers, wire feed housing, and all metal parts touching the welding wire are electrically live. Incorrectly
installed or improperly grounded equipment is dangerous.
•
Connect the primary input cable according to Australian and New Zealand standards and regulations.
• Avoid all contact with live electrical parts of the welding/cutting circuit, electrodes and wires with bare hands.
• The operator must wear dry welding gloves while he/she performs the welding/cutting task.
• The operator should keep the work piece insulated from himself/herself.
• Keep cords dry, free of oil and grease, and protected from hot metal and sparks.
• Frequently inspect input power cable for wear and tear, replace the cable immediately if damaged, bare wiring is dangerous and can
kill.
• Do not use damaged, under sized, or badly joined cables.
• Do not drape cables over your body.
•
We recommend (RCD) safety switch is used with this equipment to detect any leakage of current to earth.
Fumes and gases are dangerous.
Smoke and gas generated whilst welding or cutting can be harmful to people’s health. Welding
produces fumes and gases. Breathing these fumes and gases can be hazardous to your health.
Do not breathe the smoke and gas generated whilst welding or cutting, keep your head out of the fumes
• Keep the working area well ventilated, use fume extraction or ventilation to remove welding/cutting fumes and gases.
•
In confined or heavy fume environments always wear an approved air-supplied respirator.
•
Welding/cutting fumes and gases can displace air and lower the oxygen level causing injury or death. Be sure the breathing air is safe.
• Do not weld/cut in locations near de-greasing, cleaning, or spraying operations. The heat and rays of the arc can react with vapours to
form highly toxic and irritating gases.
• Materials such as galvanized, lead, or cadmium plated steel, containing elements that can give off toxic fumes when welded/cut. Do
not weld/cut these materials unless the area is very well ventilated, and or wearing an air supplied respirator.
Arc rays: harmful to people’s eyes and skin.
Arc rays from the welding/cutting process produce intense visible and invisible ultraviolet
and infrared rays that can burn eyes and skin.
Always wear a welding helmet with correct shade of filter lens and suitable protective clothing including welding gloves whilst the
welding/cutting operation is performed.
• Measures should be taken to protect people in or near the surrounding working area. Use protective screens or barriers to protect
others from flash,glare and sparks; warn others not to watch the arc.
4
| VIPER 120 SYNERGIC MIG Welder Manual
SAFETY