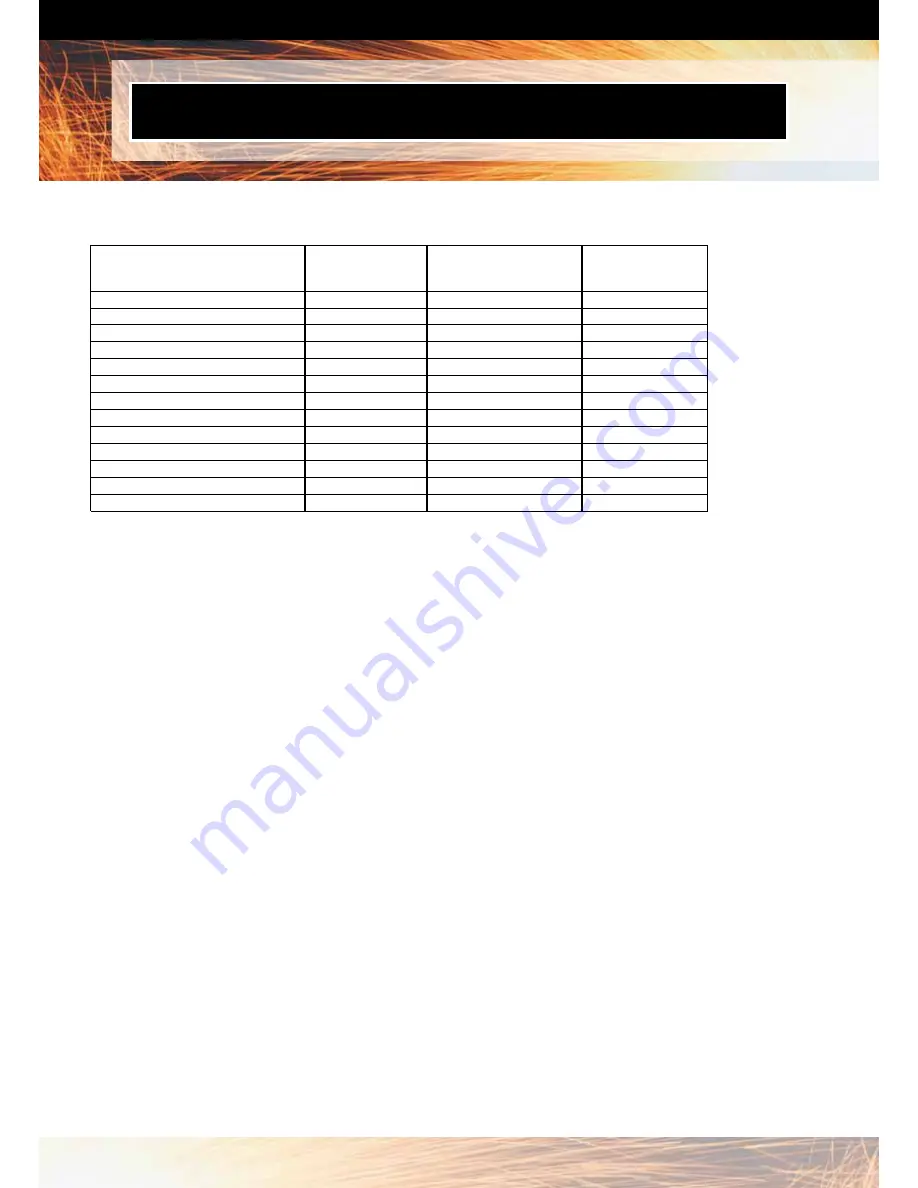
2
The properties of these and other commonly used gases are listed in the table below.
This table summarises the properties, characteristics and hazards of the more common gases used in gas welding, cutting and
allied processes.
PHYSICAL AND SAFETY PROPERTIES OF GASES
Notes
1
LP Gas consists primarily of Propane (C3H8) - other constituents include artificial odourisers for safety
2
Approximate calculated values only - there is some scatter in the literature.
3
N/S = Not specified in this Standard
Oxygen
Cylinder colour is black. Oxygen has no smell, and is generally considered non-toxic at atmospheric pressure.
Oxygen normally constitutes 21% of air and when the concentration of oxygen exceeds 21%, flammable materials become
increasingly easier to ignite and burn more rapidly and with a higher flame temperature. Oxygen itself does not burn, but
supports and accelerates combustion in other substances including those not normally considered combustible and which
may be readily ignited by sparks. Metals may also burn. Hence, great caution must be exercised in preventing oxygen
enrichment of the atmosphere, particularly in confined space situations. Oxygen should never be called "air".
Oxygen in contact with oil, grease, other hydrocarbons or oil based substances can cause spontaneous ignition and
consequential fire or explosion. Hence all oxygen systems (e.g. cylinders, pipework, regulators, blowpipes) must be kept
completely free of oil or grease.
Proper advice should be sought, e.g. from Gas Suppliers and Equipment manufacturers, before using any materials for oxygen
service, especially lubricants, seals and thread sealants, including
PTFE
tape, which have not been supplied for use with
oxygen and marked accordingly.
When the oxygen concentration in the atmosphere is less than 21%, gradual and sometimes undetectable changes occur in
operator's alertness and efficiency.
Each year many accidents ranging from minor to fatal types occur through either misuse of oxygen or failure to understand its
properties and their significance.
Some lessons which have been learnt through misuse or unsafe use of oxygen are:
a)
DO NOT use oxygen to refresh air: There is often a temptation to use oxygen to 'sweeten' air when welding or cutting
operations have been carried out in confined spaces. Large amounts of oxygen can be released locally in a short time
from gas cylinders under pressure. In one situation where this was done, hot work in the form of flame cutting was
INSTRUCTION MANUAL FOR UNI-FLAME
GAS WELDING, FLAME CUTTING AND GOUGING KIT
CHART 1
Property
Oxygen
Acetylene
LP Gas
(O2)
(C2H2)
(C3H8)
Note 1
Density relative to air
1.103
0.901
1.52 to 2
Ignition limits V% - in air
-
2.5 to 80
2.2 to 9.5
Ignition limits V% - in oxygen
-
2.5 to 80
2 to 57
Ignition temp
∞
C - in air
-
423
554
Ignition temp
∞
C - in oxygen
-
428
530
Flame temp in air (Note 4)
-
2325
1925
Flame temp in oxygen (Note 4)
-
3100
2800
Smell
Odourless
Pungent (Sweet)
Pungent
Colour
Colourless
Colourless
Colourless
Gas cylinder colour (AS 4484)
Black
Maroon
Silver/Grey
Regulator colour (AS 4267, AS 4480)
Black
Red
Orange
Welding Hose colour (AS 1335)
Blue
Red
Orange
Safety device colour (AS 4603)
Blue
Red
Red