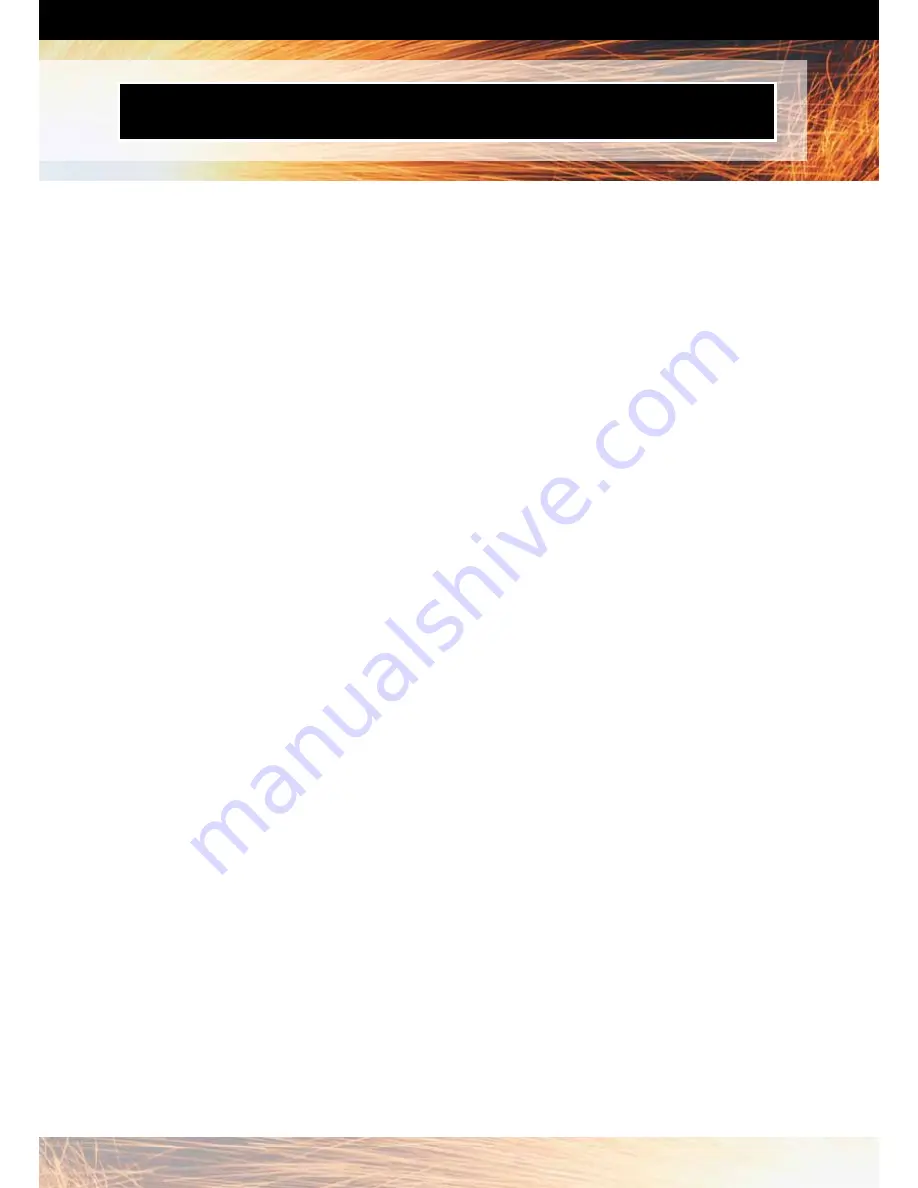
9
Gas Welding
- Low heat input
Shade 3
- Light fusion welds
Shade 4
- Heavy fusion welds
Shade 5
Cylinder trolleys
Cylinder trolleys should be designed and built with due regard to stability in operation.
The cylinders, maximum of one each oxygen and fuel, should rest fully and securely on the base of the trolley. Means of
restraint of the cylinders, e.g. a chain or strap, should be provided. The maximum size of cylinder stated on a permanent label
on the trolley should not be exceeded.
Consideration should be given to possible release of the cylinder safety devices, and unimpeded gas release from them
should be provided.
System Assembly
General compatibility
Your Uni-Flame gas welding and cutting kit comprises many components. It is important for safe operation that replacement
parts purchased in the future are genuine Uni-Flame parts or parts that are compatible and suitable for use with Uni-Flame gas
equipment.
Fuel gas
The choice of fuel gas uniquely determines several of the system operating parameters, especially equipment and operating
pressures. Only equipment specified by the manufacturer for use with that particular fuel gas shall be used.
Acetylene gas should not be used at flowing pressures exceeding 150 kPa downstream of the outlet of the pressure regulator
(see AS 4267). LPG equipment including especially regulators and hose, should never be used in Acetylene systems. It should
be noted that Gas Suppliers recommend that the maximum acetylene gas draw-off rate should not exceed 1/7 of the cylinder
contents per hour, which for the common large Acetylene cylinder of 7 m3 gas capacity limits the maximum flow to 0.14 m3/hr
or 17 l/min.
LPG systems should comprise only equipment especially designated for LPG except for multi-fuel gas components where the
manufacturer specifically nominates LPG amongst the recommended fuels. LPG systems are not subject to maximum outlet
pressure limitations except that at low temperatures the vapour pressure in the cylinders for some mixtures may prevent high
system pressures. 400 kPa is a commonly used upper limit.
Flow capacity
The tip or nozzle in use determines the required system pressures and flows and hence the pressure regulator outlet pressure
settings. Particular care must be taken in allowing for pressure drops, especially through long lengths of small diameter hose
and multiple safety devices. Manufacturer’s instructions should be carefully followed. A system which has excessive pressure
drops may become unstable resulting in possible retreat of the flame into the tip leading to overheating, backfire or flashback.
Pressure drop is particularly important in acetylene systems because of the limitation in maximum operating pressure to only
150 kPa maximum.
Setting Up Plant Safely
System operation
Before operation these important steps must be carried out:
a)
Leak testing
Prior to initial use of gas equipment, all breakable connections, glands and valves should be checked for leakages, e.g.
by a pressure drop method or by means of a leak detecting fluid. Smell should not be relied upon as many persons
have a poor sense of smell. NEVER test for leaks with a flame.
b)
Purging
It is strongly recommended to purge oxygen and fuel gas hoses prior to usage at the start of the day and after the
blowpipe has been shut down for a substantial period of time such as lunch periods or overnight. This must not be
done in confined spaces or in the presence of any ignition source. Always refer to operating instructions for the
correct purging procedures.
c)
Lighting
Flint lighters or stationary pilot flames should be used for ignition of flames. Blowpipes must not be lit or re-lit by hot
metal, matches, hot electrodes or welding arc. When lighting, ensure that the flame cannot touch either nearby
personnel or any combustible material. Always refer to operating instructions for the correct lighting procedures.
(See Chart 5)
INSTRUCTION MANUAL FOR UNI-FLAME
GAS WELDING, FLAME CUTTING AND GOUGING KIT