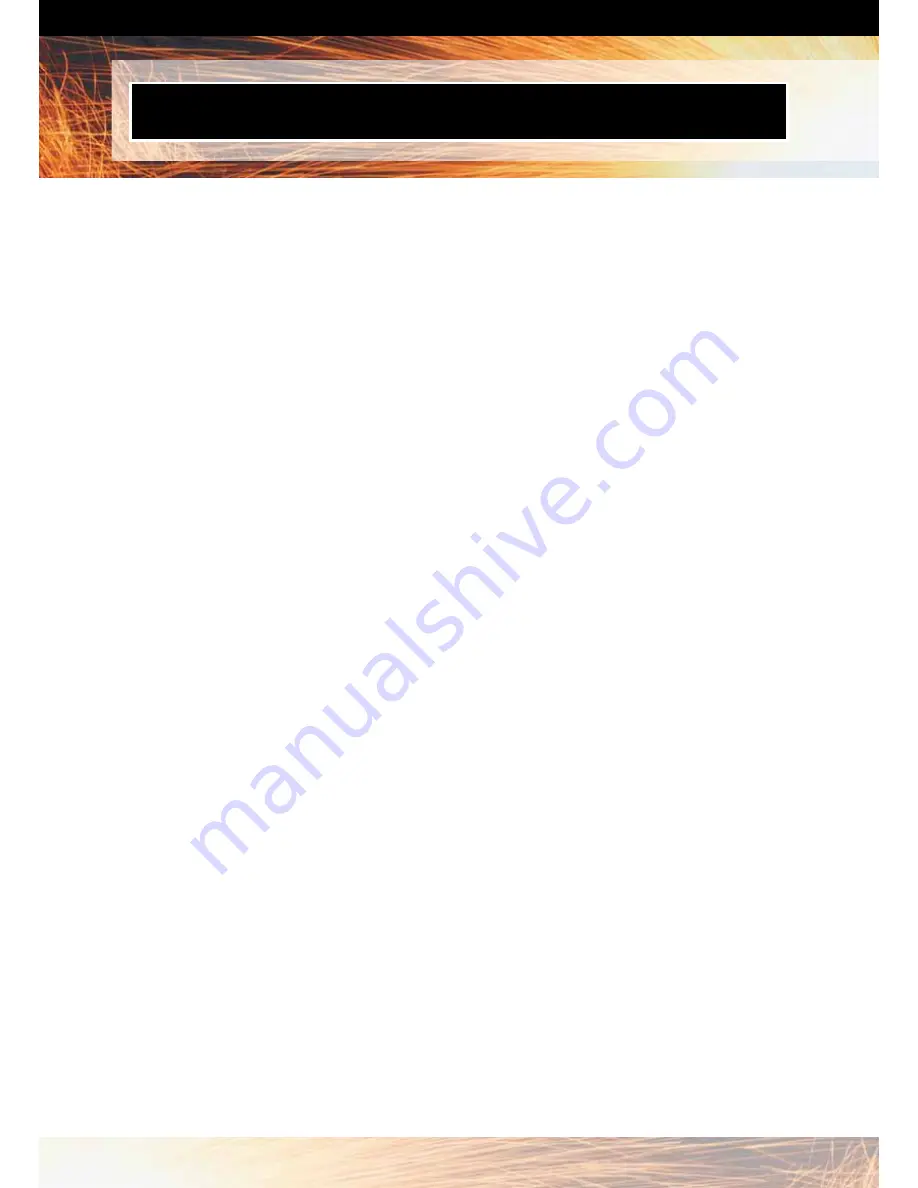
12
Acetylene Cylinder Overheating
Acetylene cylinders may become hot either through flashback or due to accidental heating (e.g. contact with hot objects,
fires). To prevent serious accidents, the following procedure should be carried out immediately overheating is noted:
a)
Shut cylinder valve quickly and have the supplier notified as soon as practicable. If the cylinder is on fire,
call the fire brigade.
b)
Clear all personnel from the area.
c)
Cool the cylinder with a plentiful supply of water, preferably from a fire hydrant and with the person behind a suitable
protective barrier.
d)
If the cylinder safety device functions and issuing gas ignites, cool as above, but do not extinguish the flames.
Where gas does not ignite, all sources of ignition must be removed from the area if this can be done safely.
e)
Continue cooling but with stops at intervals to check if the cooling water dries off the cylinder or if it remains wet.
f)
When the cylinder remains wet on removal of the water, the cylinder should be removed to an open space away from
any ignition source and placed under water e.g., in a 200 litre drum.
g)
Continue cooling for 24 hours or as advised by a competent authority.
Oxygen Cylinder Explosions
Accidents have been reported which involve explosion of an oxygen cylinder due to direct flame impingement from an
adjacent acetylene cylinder. Such accidents arise when the fusible plugs melt due to cylinder overheating, the escaping gas
ignites and the flame impinges on the oxygen cylinder. This causes softening, bulging and bursting of this cylinder without
appreciable increase in its internal pressure, i.e. without causing the bursting disc to rupture.
Where oxygen and acetylene cylinders in use are adjacent to each other, consideration should be given to protecting the
oxygen cylinder by placing a non-flammable shield, e.g. a 2-3 mm sheet of steel or refractory fibre between the cylinders. The
shield should extend at least from the shoulder of the acetylene cylinder to the top of the oxygen cylinder regulator .
REFURBISHMENT OR REPLACEMENT INTERVALS
1.
REGULATORS (including their integral protective devices)
Visual examination to determine suitability for service (eg gas, pressure rating, damage), condition of threads and
sealing surfaces, oil or grease contamination.
Leak test all joints at working pressure. Six monthly:
Functional tests to ensure the correct operation of internal components.
Manufacturer or supplier recommendation, but not exceeding 5 years.
2.
FLASHBACK ARRESTORS
and other external devices (including non-return valves)
Visual examination to determine suitability for service (e.g. gas, pressure rating, damage), condition of threads and
sealing surfaces, oil or grease contamination.
Leak test all joints at working pressure. Yearly as detailed in AS 4603 or following a flashback:
Proper functioning of the non-return valves and flashback arrestors.
For pressure-activated valves, check there is no flow in the normal direction with the valve tripped.
Manufacturer or supplier recommendation, but not exceeding 5 years4.
3.
HOSE ASSEMBLIES
Visual examination to determine suitability for service (e.g. gas, pressure rating, damage),
condition of cover, threads and sealing surfaces of the end fittings.
Leak test all joints at working pressure Six monthly:
Check for absence of cuts and excessive wear by bending the hose in a tight radius, to ensure reinforcement is not
visible.Determined by the hose assembly condition.
4.
BLOWPIPES, MIXERS AND ATTACHMENTS
Visual examination for damage of the threads and sealing surfaces of the
hose connections and the attachment connections.
Test control valve function.
Blank the attachment connection and leak test for internal malfunction. Manufacturer or supplier recommendation,
but not exceeding 5 years.
INSTRUCTION MANUAL FOR UNI-FLAME
GAS WELDING, FLAME CUTTING AND GOUGING KIT