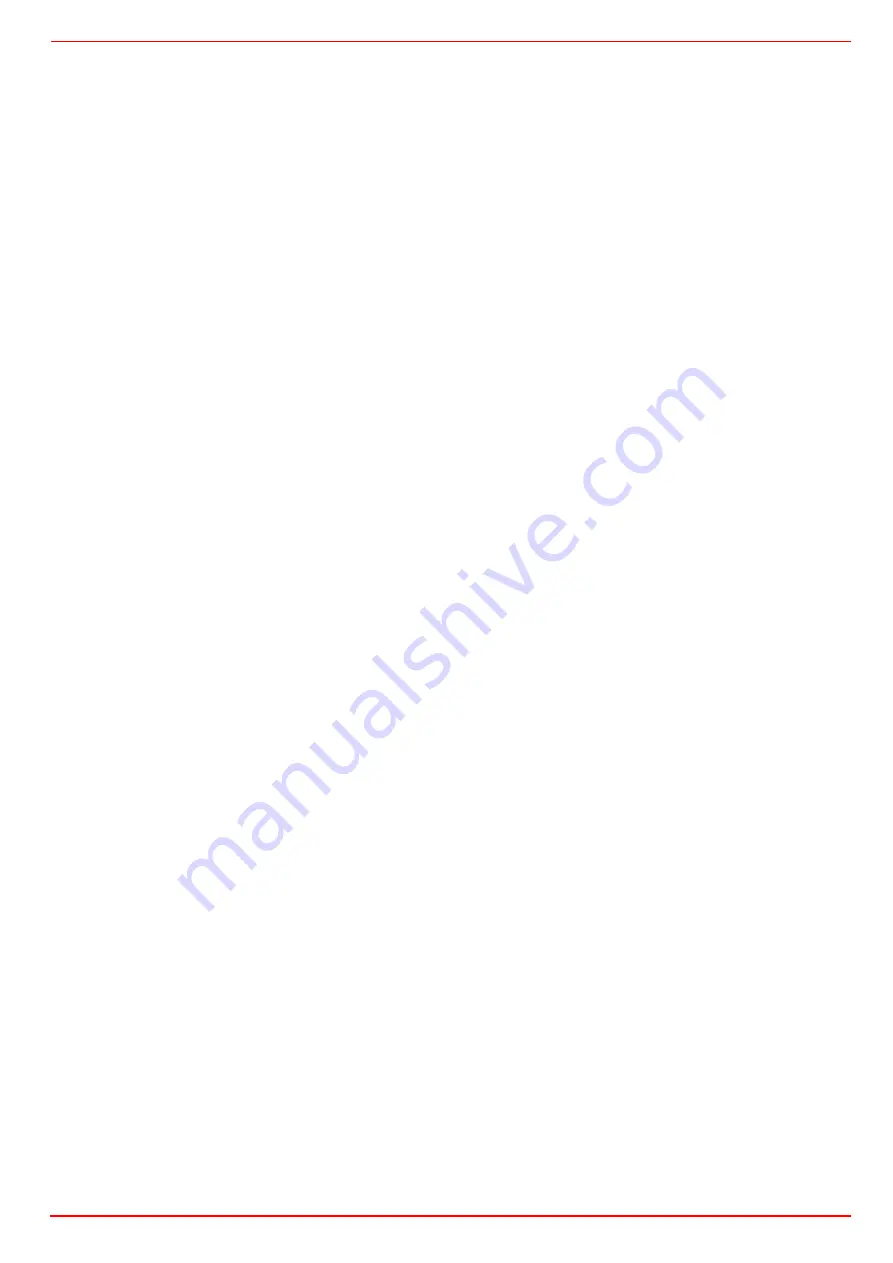
Twin-tube burners (**)
t3
Preignition time until the all clear to the pilot burner valve at
terminal 17.
t2
First safety time (pilot flame strenght); at the end of the safety time
a flame signal should appear at terminal 22 of the amplifier and it should
stay on, until a regulation stop; if it does not, the apparatus will block.
t4
Interval until the consent to the fuel valve at terminal 19, for the first
flame of the main burner.
t9
2nd safety time; at the end of the second safety time the main bur-
ner should be lit by means of the pilot. At the end of this period, terminal
17 is dead and therefore the pilot burner will be out.
t5
Interval; at the end of t5 terminal 20 is live. At the same time the
monitor outlets from 9 to 11 and the terminal 8at the input of the active
part of the apparatus are galvanically separated so as to protect the appa-
ratus itself from recovery voltage through the strenght regulator circuit.
When the strenght regulator LR at terminal 20 gives the consent,
the start-up programme for the apparatus comes to an end. Depending on
time variants, the programmer stops either immediately or at the end of a
set time, without effecting the position of the contacts.
B
Operational position of the burner
B-C Burner operation (production of heat)
While the burner is working the strnght regulator controls the damper,
according to the demand for heat, by means of the positioning at nominal
load of the auxiliary contact "V" of the damper servocontrol.
C
Regulation stop for operation of "R"
When there is a regulation stop the fuel valves immediately close. At the
same time the programmer starts to programme:
t6 Post-ventilation
time
(post-ventilation with the ventilator "G" at ter-
minal 7).Shortly after beginning of the post-ventilation time terminal 10
becomes live and moves the damper to the "MIN" position. The full clo-
sure of the damper only happens towards the end of the post-ventilation
time and is prompted by an automatic signal from terminal 11
t13
Admissible post-ignition time
During this time the flame monitor circuit may still receive a flame signal
without the apparatus blocking.
D-A End of automatic programme
At the end of t6, at the point where the programmer and the automatic
contacts have reverted to the starter position, the detection probe test
restarts.
During an operational stop even an unscheduled flame signal lasting a
few seconds can cause a block because during this period an NTC in the
circuit acts as retarder.This means that brief unscheduled influences can-
not cause a block.
(**) Times t3, t2 and t4 only apply only to safety devices in the series 01.
Specifications
Mains voltage
220V -15%...240V +10%
Frequency
50Hz -6%...60Hz +6%
Absorbed capacity
3.5 VA
Built-in fuse
T6.3/250E slow action DIN41571 No.
451915070
External fuse
max. 16A
Interference N-VDE0875
Flow permitted at terminal 1
5A (DIN 0660 AC3)
Flow permitted at control terminals
4A (DIN 0660 AC3)
Flow at monitor contacts:
input at terminals 4 & 5
1A, 250V
input at terminals 4 & 11
1A, 250V
input at terminals 4 & 14
function of the load at terminals 16 and
19, min.1A, 250V
Emplacement
Any
Protection IP40
Permitted ambient temp
-20...+60° C
Min.temperature (trans/storage) -50° C
Weight:
apparatus
approx. 1,000g.
base
approx. 165g.
Ionisation monitor
voltage in detector electrode
normal working
330V ±10%
test
380V ±10%
short circuit current
max. 0,5 mA
Ionisation current, min.request 6 µA
max. permitted length for connecting cables
normal cable (laid separately**) 80m
armoured cable(high frequency) protection at terminal 22
140m
UV monitor
Voltage in UV detector
normal working
330V ±10%
test
380V ±10%
Detector current, min. request* 70µA
Max. detector current
normal working
630 µA
test
1300 µA
Max.length of connecting cable
normal cable (laid separately**) 100m
armoured cable (high frequency) protected at terminal 22
200m
Weight
QRA2
60 g
QRA10
450 g.
*Connect up in parallel to the measuring device a condenser 100µF,
10...25V.
** The wire connecting up the detector electrode should not be in the
same sleeve as the other conductor wires.
Ignition spark monitor with QRE1 series 02 detector
Minimum detector current
30µA
Operating times
t7 initial delay for ventilator G2 2
t16 initial delay of air damper OPEN consent
4
t11 opening time for damper
any
t10 initial delay for air pressure monitor8
t1 pre-ventilation time with damper open36
t12 travel time for air damper to MIN positionany
t3 t3' pre-ignition time
t3
4
t3
'-
t2 t2' safety time (1st safety time for burners with intermittent pilot
lighter
t2
2
t2
'-
t4 t4' interval between start of t2 and response to valve at terminal 19
t4
10
t4
'-
t9 2nd safety time for burners with intermittent pilot lighter 2
t5 interval between end of t4 and response at terminal 20 10
t20 interval before programmer cuts out after start-up-
duration of start-up
60
t6 post-ventilation time (G2 only)
12
t13 permitted post-ignition time
12
t16 initial delay from opening consent of the air damper
t20 interval until the automatic shut-off of the programming mechanism
after the burner start