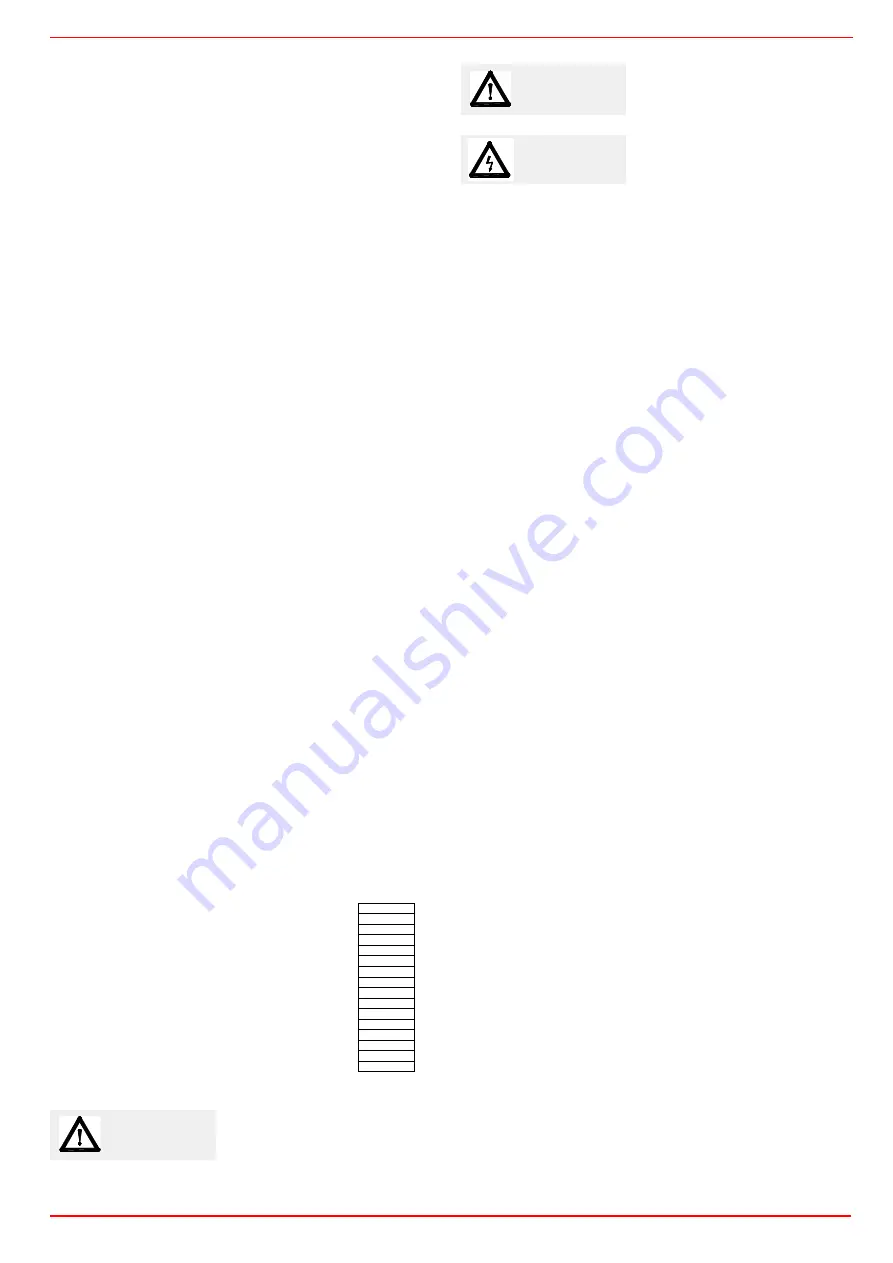
4
-EN 60204-1:2006 (Safety of machinery – Electrical equipment of machi-
nes.)
-CEI EN 60335-1 (Specification for safety of household and similar electri-
cal appliances);
-CEI EN 60335-2-102 (Household and similar electrical appliances.
Safety. Particular requirements for gas, oil and solid-fuel burning applian-
ces having electrical connections).
-UNI EN ISO 12100:2010 (Safety of machinery - General principles for
design - Risk assessment and risk reduction);
Norme nazionali / National Standard
-UNI 7824 (Atomizing burners of the monobloc type. Characteristics and
test methods.
Gas - Heavy oil burners
,
European directives:
-2009/142/EC (Gas Directive)
-2014/35/UE (Low Tension Directive)
-2014/30/UE (Electromagnetic compatibility Directive)
-2006/42/EC (Machinery Directive)
Harmonized standards
-UNI EN 676 (Automatic forced draught burners for gaseous fuels)
-EN 55014-1 (Electromagnetic compatibility- Requirements for house
hold appliances, electric tools and similar apparatus)
-EN 60204-1:2006 (Safety of machinery – Electrical equipment of machi-
nes.)
-CEI EN 60335-1 (Specification for safety of household and similar electri-
cal appliances);
-CEI EN 60335-2-102 (Household and similar electrical appliances.
Safety. Particular requirements for gas, oil and solid-fuel burning applian-
ces having electrical connections).
-UNI EN ISO 12100:2010 (Safety of machinery - General principles for
design - Risk assessment and risk reduction);
National Standard
- UNI 7824 (Atomizing burners of the monobloc type. Characteristics and
test methods.
Industrial burners
European directives
-2009/142/EC (Gas Directive)
-2014/35/UE (Low Tension Directive)
-2014/30/UE (Electromagnetic compatibility Directive)
-2006/42/EC (Machinery Directive)
Harmonized standards
-EN 55014-1 (Electromagnetic compatibility- Requirements for house
hold appliances, electric tools and similar apparatus)
-EN 746-2 (Industrial thermoprocessing equipment - Part 2: Safety requi-
rements for combustion and fuel handling systems)
-UNI EN ISO 12100:2010 (Safety of machinery - General principles for
design - Risk assessment and risk reduction);
-EN 60204-1:2006 (Safety of machinery – Electrical equipment of machi-
nes.)
-EN 60335-2 (Electrical equipment of non-electric appliances for house-
hold and similar purposes. Safety requirements)
Burner data plate
For the following information, please refer to
the data plate:
z
burner type and burner model: must be
reported in any communication with the
supplier
z
burner ID (serial number): must be repor-
ted in any communication with the supplier
z
date of production (year and month)
z
information about fuel type and network
pressure
SYMBOLS USED
Figures, illustrations and images used in this manual may differ in appearance from
the actual product.
WARNING!
Failure to observe the warning may
result in irreparable damage to the
unit or damage to the environment
Type --
Model
--
Year --
S.Number --
Output --
Oil Flow
--
Fuel
--
Category --
Gas Pressure
--
Viscosity --
El.Supply --
El.Consump. --
Fan Motor
--
Protection --
Drwaing n°
--
P.I.N.
--
DANGER!
Failure to observe the warning may
result in serious injuries or death.
WARNING!
Failure to observe the warning may
result in electric shock with lethal con-
sequences