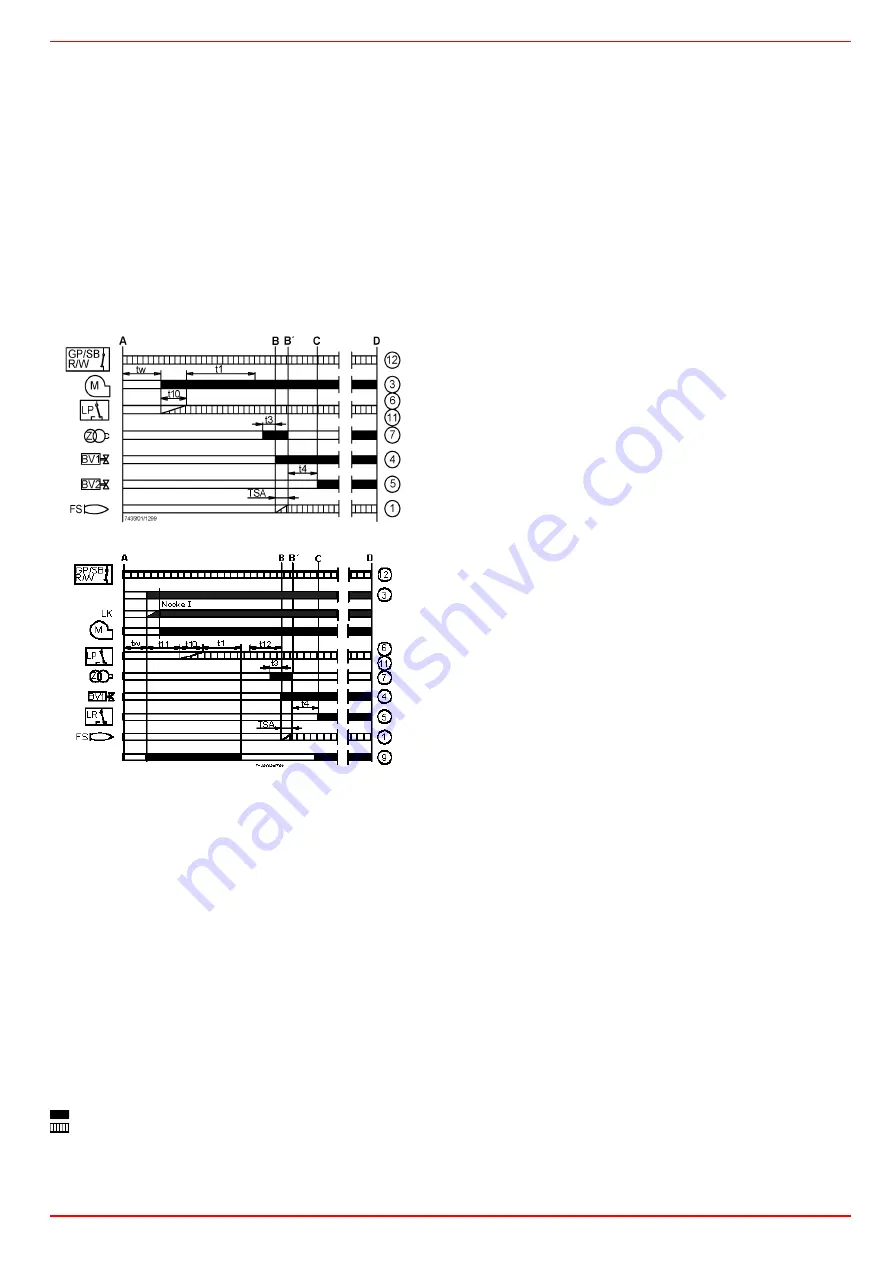
SIEMENS LGB 21/22.. CONTROL BOX
Function
The programme run is shown in the diagrams. The required and permissi-
ble input signals for the control part and flame supervision part are pictu-
red as a hatching correspondingly in the function diagrams. If these input
signals are missing, the controller interrupts the start-up programme and
initiates a lock-out at the place where the safety regulations demand it.
The LGB types are fitted with under voltage protection, i.e. the load relay
AR is de-energized when the supply voltage falls below 160 V. The burner
control automatically attempts a new start-up when the supply voltage
again exceeds 160 V
A
Start-up command from the temperature or pressure
controller “R”
A-C
Start-up programme
C-D
Burner operation (heat production corresponding to the control
commands)
D
Controlled shut-down by “R”
LGB21
LGB22
Key for operation diagram
A - C Startup sequence
tw
Waiting time, 8s for LGB21, 9s for LGB22
t1
Prepurge time 30s
TSA Ignition safety time 3s
t3
Preignition time, 2s for LGB21, 3s for LGB22
t4
Interval «BV1-BV2» or «BV1-LR», 8s
t10
Specified time for air pressure signal, 5s for LGB21, 3s for LGB22
t11
Programmed opening time for actuator «SA», max. 12s
t12
Programmed closing time for actuator «SA», max. 11s
BV
Fuel valves
FS
Flame presence signal
GP
Gas pressure switch
LP
Air pressure switch
LR
Load controller
M
Fan motor
R
Temperature or pressure controller
W
Safety thermostat or pressure switch
Z
Ignition transformer
1...12 Terminals of the burner flame controls on AGK11's socket
Command signal from flame control
Input signals
Conditions for starting up the burner:
z
The burner control must not be locked out.
z
The contacts of the gas pressure switch ”GP", the temperature or
pressure switch “W" and the controller “R", must be closed.
Start-up programme
A
Start command (switching on)
This command is triggered by control thermostat / pressure controller
«R». Terminal 12 receives voltage and the programming mechanism
starts running. On completion of waiting time «tw» with the LGB21..., or
after air damper «SA» has reached the nominal load position (on comple-
tion of «t11») with the LGB22..., fan motor «M» will be started.
tw
Waiting time
During the waiting time, air pressure monitor «LP» and flame relay «FR»
are tested for correct contact positions.
t11
Programmed opening time for actuator «SA»
(Only with LGB22...) The air damper opens until the nominal load position
is reached. Only then will fan motor «M» be switched on.
t10
Specified time for air pressure signal
On completion of this period of time, the set air pressure must have built
up, or else lockout will occur.
t1
Prepurge time
Purging the combustion chamber and the secondary heating surfaces:
required with low-fire air volumes when using the LGB21... and with nomi-
nal load air volumes when using the LGB22.... The diagrams show the so-
called prepurge time «t1» during which air pressure monitor «LP» must
indicate that the required air pressure is available. The effective prepurge
time «t1» comprises interval end «tw» through «t3».
t12 Programmed closing time for actuator «SA»
(Only with LGB22...)During «t12», the air damper travels to the low-fire
position.
t3 Preignition time
During «t3» and up to the end of «TSA», flame relay «FR» is forced to
close. On completion of «t3», the release of fuel is triggered at terminal 4.
TSA Ignition safety time
On completion of «TSA», a flame signal must be present at terminal 1.
That flame signal must be continuously available until shutdown occurs,
or else flame relay «FR» will be deenergized, resulting in lockout.
t4 Interval
LGB21...: time to the release of the second fuel valve «BV2»
LGB22...: on completion of «t4», the heat source is controlled depending
on the load (release of load controller «LR»)
B - B'
Interval for flame establishment
C
Burner operation position
C - D
Burner operation (heat production)
Operation of the burner at the maximum strenght or, with a flame control-
ler for the load.
D
Controlled by "R" shutdown
The burner stops, waiting for the next ignition.