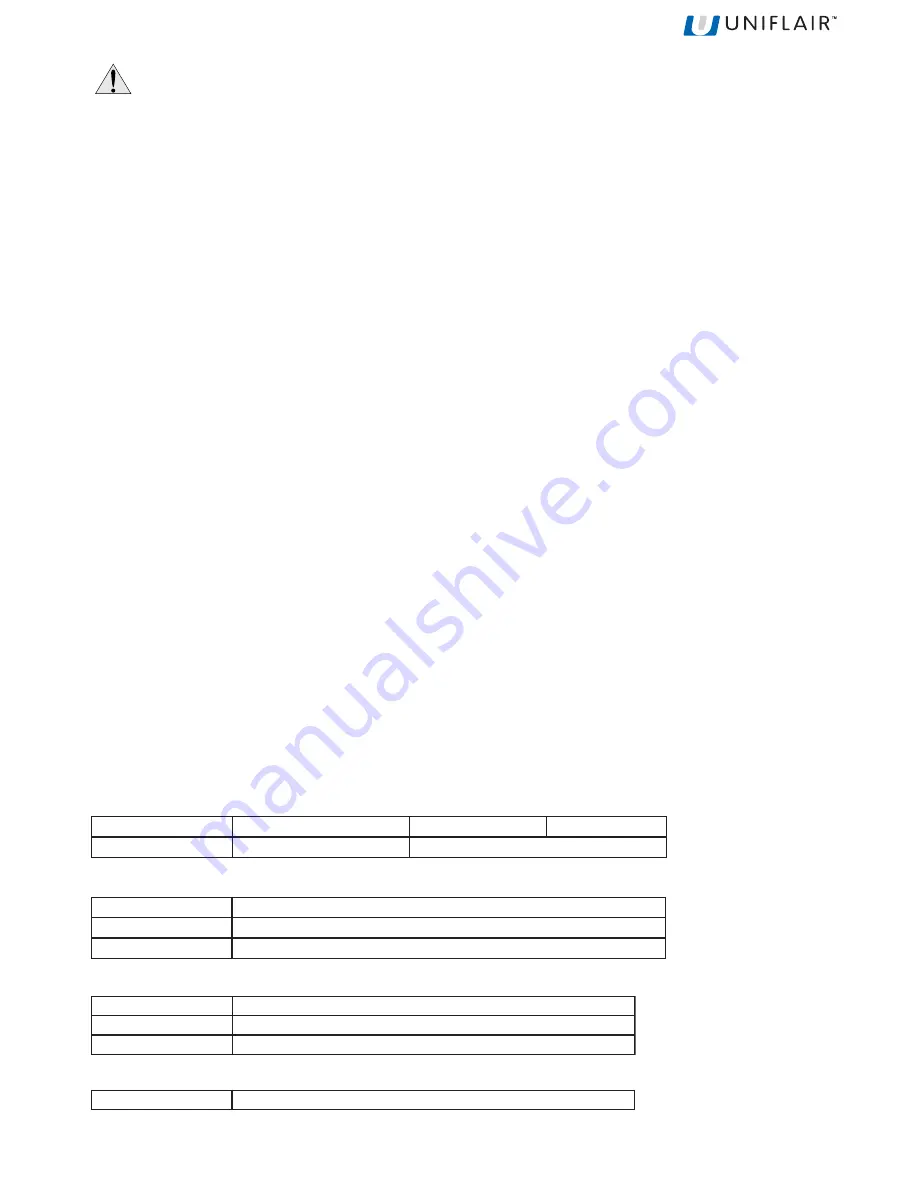
29
Evacuation of the refrigeration circuit and charging of refrigerant
WARNING! The charging and maintenance of the refrigeration circuit must only be carried out by a
qualified hydraulic technician.
The refrigeration circuit is pre-charged with nitrogen.
To load the refrigerant, carry out the following procedure:
R22
•
open any shut-off valves present in the machine to ensure
that all of the components will be evacuated;
•
connect a pump to empty the schrader connections
efficiently, or to the 1/4" SAE connections present on
the intake and delivery sides of the compressors;
•
connect the refrigerant cylinder to the loading
connections;
•
create a vacuum within the lines while maintaining the
pressure below 100 Pa absolute (0,7 mm Hg) for a long
time in order to evacuate the air as well as any traces of
humidity. It is preferable that the vacuum is reached
slowly and maintained for a long period of time;
•
wait for a build up period of 100 seconds and check that
the pressure has not exceeded 200 Pa absolute.
Generally, in the case of suspicion of strong hydration of
the circuit or an extremely extensive system, it will be
necessary to break the vacuum with anhydrous nitrogen
and then repeat the evacuation procedure as described;
•
break the vacuum by performing a preload from the R22
coolant cylinder;
•
after having started the compressor, slowly complete the
loading phase until the pressure within the lines has been
stabilised and the gaseous bubbles have disappeared
from the flow sight glass;
•
the loading process must be controlled in environmental
conditions with a delivery pressure of approximately 18
bar (equivalent to a saturated temperature of 48 °C); in
the case of units with ON/OFF condensation controls,
avoid switching the condenser fan on and off, which may
partially obstruct the intake surface. It is wise to check
that the sub-cooling of the liquid at the entry of the
thermostatic valve is between 3 and 5 °C below the
condensation temperature read on the scale of the
pressure gauge and that the overheating of the vapour at
the exit of the evaporator is equal to 5-8 °C.
R407C - R410A
•
open any shut-off valves present in the machine to ensure
that all of the components will be evacuated;
•
connect a pump to empty the schrader connections
efficiently, or to the 1/4" SAE connections present on
the intake and delivery sides of the compressors;
•
connect the refrigerant cylinder to the loading
connections;
•
create a vacuum within the lines whilst maintaining the
pressure below 10 Pa absolute (0,07 mm Hg) for a long
time in order to evacuate the air as well as any trace of
humidity. It is preferable that the vacuum is reached
slowly and maintained for a long period of time;
•
wait for a build up period of 100 seconds and check that
the pressure has not exceeded 200 Pa absolute.
Generally, in the case of suspicion of strong hydration of
the circuit or an extremely extensive system, it will be
necessary to break the vacuum with anhydrous nitrogen
and then repeat the evacuation procedure as described;
•
break the vacuum by performing a preload in liquid phase
from the R407C and R410A coolant cylinder;
•
after having started the compressor, slowly complete the
loading phase until the pressure within the lines has been
stabilised and the gaseous bubbles have disappeared
from the flow sight glass;
•
the loading process must be controlled in environmental
conditions with a delivery pressure of approximately 18
bar (equivalent to a dew temperature of 48 °C and a bubble
temperature of 43 °C); in the case of units with ON/OFF
condensation controls, avoid switching the condenser
fan on and off, which may partially obstruct the intake
surface. It is wise to check that the sub-cooling of the
liquid at the entry of the thermostatic valve is between 3
and 5 °C below the condensation temperature read on
the scale of the pressure gauge and that the overheating
of the vapour at the exit of the evaporator is equal to
approximately 5-8 °C.
Type of oil recommended with COPELAND compressors
Type of oil recommended with MANEUROP compressors
Type of oil recommended with SANYO compressors
Type of oil recommended with Scrolltech HCJ 072-HLJ 083 compressors
)
l
i
o
l
a
r
e
n
i
M
(
2
2
R
S
G
3
o
s
i
n
u
S
2
3
F
W
o
c
a
x
e
T
M
K
s
h
c
u
F
)
E
O
P
(
C
7
0
4
R
c
c
2
2
c
i
t
c
r
A
L
A
E
l
i
b
o
M
S
2
3
L
R
E
T
A
R
A
K
M
E
I
C
I
)
l
i
o
l
a
r
e
n
i
M
(
2
2
R
2
3
O
S
I
/
l
a
r
e
n
i
M
-
P
0
6
1
p
o
r
u
e
n
a
M
)
E
O
P
(
C
7
0
4
R
Z
S
0
6
1
p
o
r
u
e
n
a
M
)
E
O
P
(
A
0
1
4
R
Z
S
0
6
1
p
o
r
u
e
n
a
M
)
l
i
o
l
a
r
e
n
i
M
(
2
2
R
T
6
5
-
Y
A
S
)
E
V
P
(
C
7
0
4
R
S
8
6
V
F
)
E
V
P
(
A
0
1
4
R
S
8
6
V
F
)
E
V
P
(
A
0
1
4
R
D
8
C
V
F
E
V
P
e
n
h
p
a
D